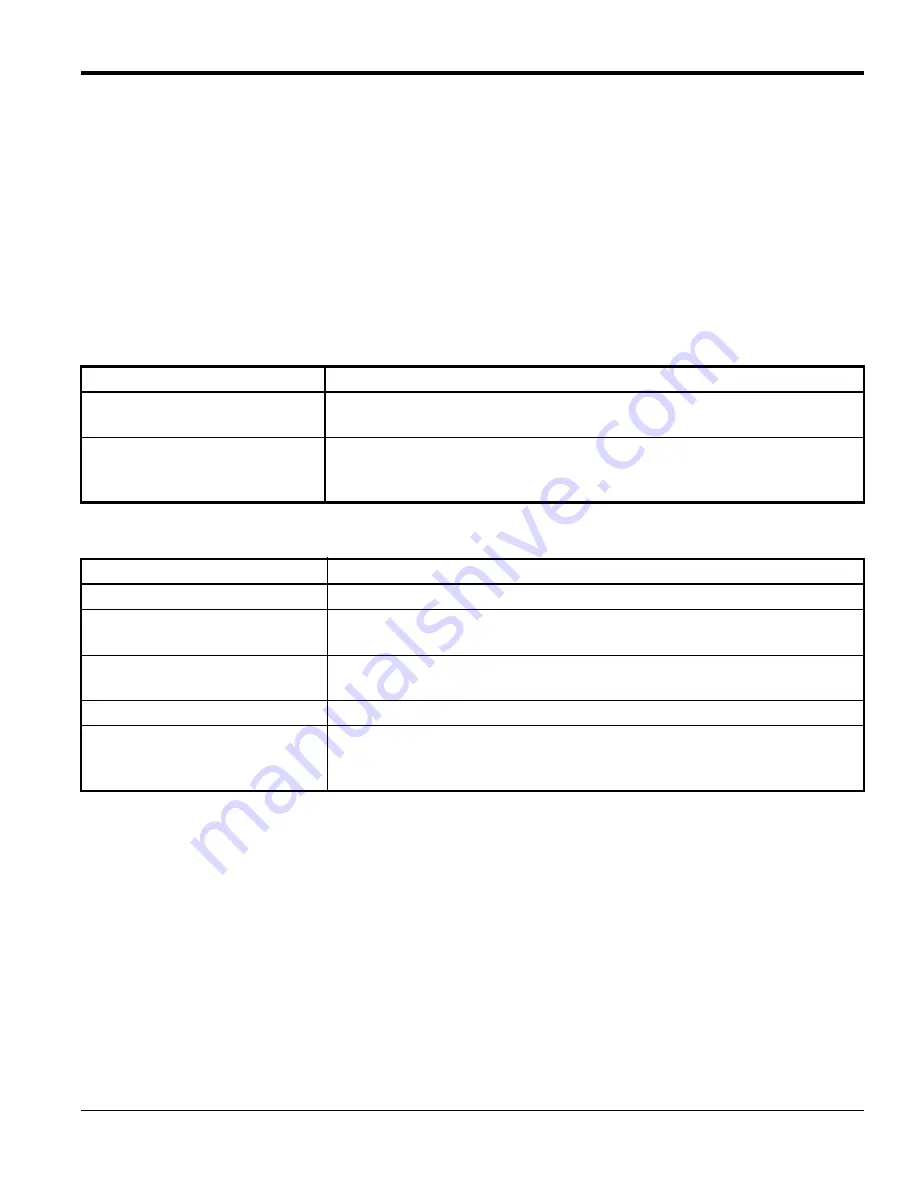
PanaFlow™ LC User’s Manual
49
Chapter 3. Programming
3.5.3b Setting up Frequency Output
To program a
Frequency Output
, use steps as in section “Log-in and Primary Pages” to navigate to the
Input/Output
settings page:
1.
In Meter Menu highlight
[Digital Output (Std)]
and press
[ENTER]
. Then highlight
[Frequency]
option
and press
[ENTER]
.
2.
Setup the
[Measurement], [Base Value], [Full Value], [Full Frequency]
and
[Error Handling]
options to
suit your needs. The Figure 59 below, shows the available options. Also refer to the Table 9 below to
understand each option.
For measurement options available on Frequency Output refer to Table 8.
Table 8: Measurement options for Frequency Output
Measurement Channel
Measurement Options for Frequency Output
Composite
Velocity, Actual Volumetric, Standard Volumetric, Mass Flow, Average
Volumetric Flow Rate, Sound speed, Reynolds #
Channel x
Velocity, Actual Volumetric, Standard Volumetric, Mass Flow, Average
Volumetric Flow rate, Sound speed, Standard Deviation of Gain, Gain
and SNR
Table 9: Frequency Output Options
Option
Functional Description
Measurement
Choose the channel and Measurement to output
Base Value
Enter measurement value that should correspond to the min. value of
the frequency range
Full Value
Enter measurement value that should correspond to the max. value of
the frequency range
Fspan
Enter the highest value of the Frequency range you want to output
Error Handling
Choose the Frequency output response during an error condition: Low,
High, Hold, or Other Value. During a meter error, the chosen Error
Handling value will be sent to the Frequency Output.
Summary of Contents for Baker Hughes PanaFlow LC XMT1000
Page 1: ...Flow 910 327 Rev A Sep 2019 bhge com PanaFlow LC User s Manual ...
Page 2: ......
Page 4: ...ii no content intended for this page ...
Page 10: ...Contents viii PanaFlow LC User s Manual ...
Page 14: ...Preface xii PanaFlow LC User s Manual no content intended for this page ...
Page 142: ...Appendix E CE Mark Compliance 128 PanaFlow LC User s Manual no content intended for this page ...
Page 182: ...Warranty 168 PanaFlow LC User s Manual no content intended for this page ...
Page 189: ......