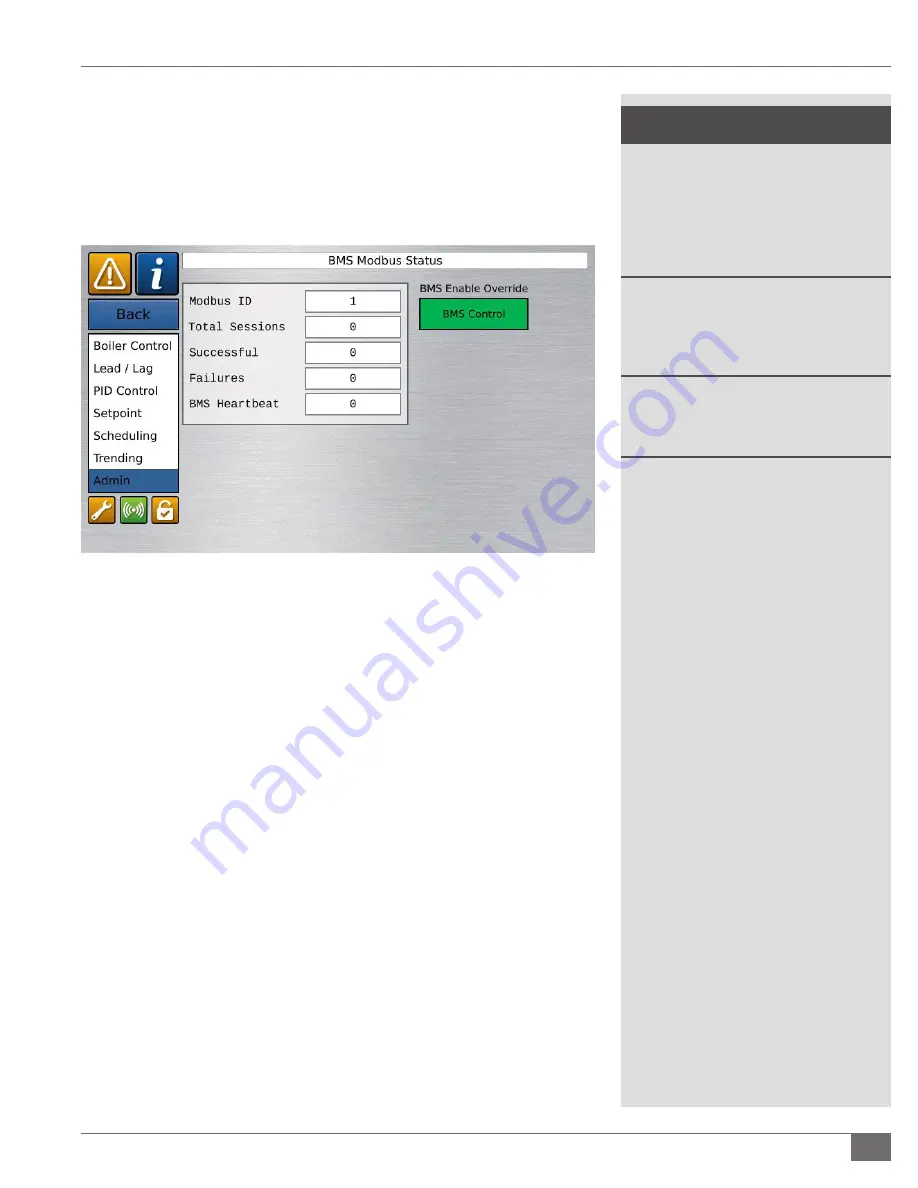
Questions? Please Contact Your Local Manufacturer’s Representative
3-51
SECTION 3
Hydronic-PURE-Control-UserManual-211214
CONTROL MENUS
!
WARNING
All information in this addendum is
for reference and guidance purposes,
and does not substitute for required
professional training, conduct, and strict
adherence to applicable jurisdictional/
professional codes or regulations.
Follow all proper lockout/tagout
procedures for service. Before beginning
any service, ensure area is free of
combustible materials and other dangers.
In order to meet warranty conditions,
ensure all appropriate maintenance
activities are performed.
BMS Network Status
Shows communication and status between the control and the BMS or other
connected Modbus device.
BMS Enable Override
provides a way to satisfy the BMS enable (Network or Dry
Contact) without needing to send a signal. This can be used if switching quickly to
Local/Standalone control or Troubleshooting purposes.
It is acceptable to wire a BAS Enable/Disable to one boiler Customer Connections
only and share this contact status over Universal Data to the Lead/Lag network.
Be advised that, per the intended Sequence of Operation, if the network is
dropped or lost, or the boiler sharing this parameter is powered off, the other
boilers will need to have the BMS Enable/Disable override button pressed to be
enabled for operation.
For situations where this is not the intended behavior, alternately the BAS Enable/
Disable can be wired in parallel across the contact of each boiler in the Leag/
Lag network. BMS communication can also be established with each respective
boiler for individual control over the BMS network (Modbus/Bacnet)