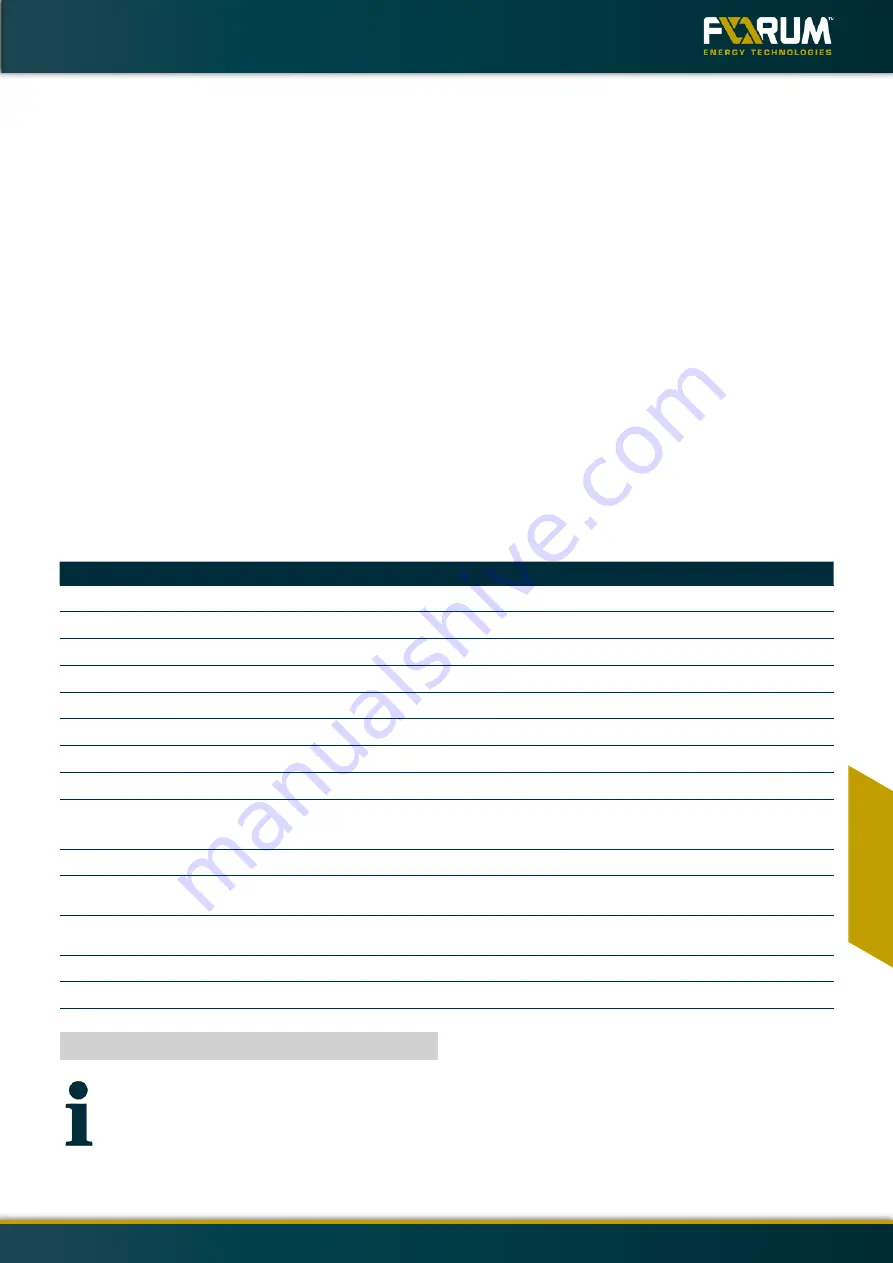
Operation Maintenance Manual
06-2018
PN 757000-D - Revision: 17 (up to SN 138212) Power Slip PS-500
137
IN
SP
EC
TI
O
N /
M
AI
N
TE
NAN
C
E
6.3
Inspection Categories
6.3.1
Inspection Category I
Observe the PS-500 during operation. Recognizing
inadequate performance and apparent defects is the goal
of this category.
Scope/Prerequisites/Procedure:
- Daily visual inspection of the PS-500 for damages and
defects during operation. Repair them if necessary.
- Functional test.
- A person with appropriate expertise must carry out the
test.
6.3.2
Inspection Category II
The inspection of category II includes all inspections of
inspection category I and additional tests.
Scope/Prerequisites/Procedure:
- Checking the state of lubrication, the condition of the
entire PS-500 and the settings of all valves.
- A person with appropriate expertise must carry out the
test.
6.3.3
Inspection Category III
The inspection of category III includes all inspections of
inspection category II and additional tests.
Scope/Prerequisites/Procedure:
- Non-Destructive Testing (NDT) of selected critical areas
and verification of all wear limits.
- Before carrying out an NDT test, remove all foreign
material such as dirt, paint, lubricants, oil and abrasion
from the affected parts. Use suitable methods such as
pickling, steam cleaning and sandblasting.
6.3.4
Inspection Category IV
The inspection of category IV includes all inspections of
inspection category III and additional tests.
Scope/Prerequisites/Procedure:
- Before carrying out an NDT test, remove all foreign
material such as dirt, paint, lubricants, oil and abrasion
from the affected parts. Use suitable methods such as
pickling, steam cleaning and sandblasting.
- Non-destructive material testing (NDT) of all critical
areas and replacement of selected consumables and
hydraulic components.
6.3.5
Inspection intervals and Inspection tasks
Pos. Task
Daily
Weekly Semiannually Annually
1
Function test and ongoing observation.
'
'
'
'
2
Functionality of Feedback.
'
'
'
'
3
Checks for cracks and loose fittings/hoses.
'
'
'
'
4
Checks for signs of deformations and leakages.
'
'
'
'
5
Check for signs of wear and corrosion.
'
'
'
'
6
Check for no loose components and presence of all warning signs.
"
'
'
'
7
Check for state of lubrication and conservation.
"
'
'
'
8
Check all possible settings (e.g. valves) on the PS-500.
"
'
'
'
9
Checking the condition of the overall structure (Rotary Table, hydraulic
system) and the interaction of all components and possible attachments
with the PS-500.
"
'
'
'
10
Checking wear limits (component measurement).
"
"
'
'
11
NDT tests of selected components
(PS-500 is largely assembled).
"
"
'
'
12
Complete NDT test of all critical areas
(PS-500 is completely disassembled).
"
"
"
'
13
Exchange of selected hydraulic components.
"
"
"
'
14
Replacement of wear-intensive components (recommended spare parts).
"
"
"
'
INFO
'
Necessary
"
Unnecessary
NDT Non-destructive testing
• Magnetic Particle Inspection (MPI)
• Ultrasonic Measurement Methods (UT)
• Eddy Current Testing (ET)
• Dye Penetrant Inspection (DPI)