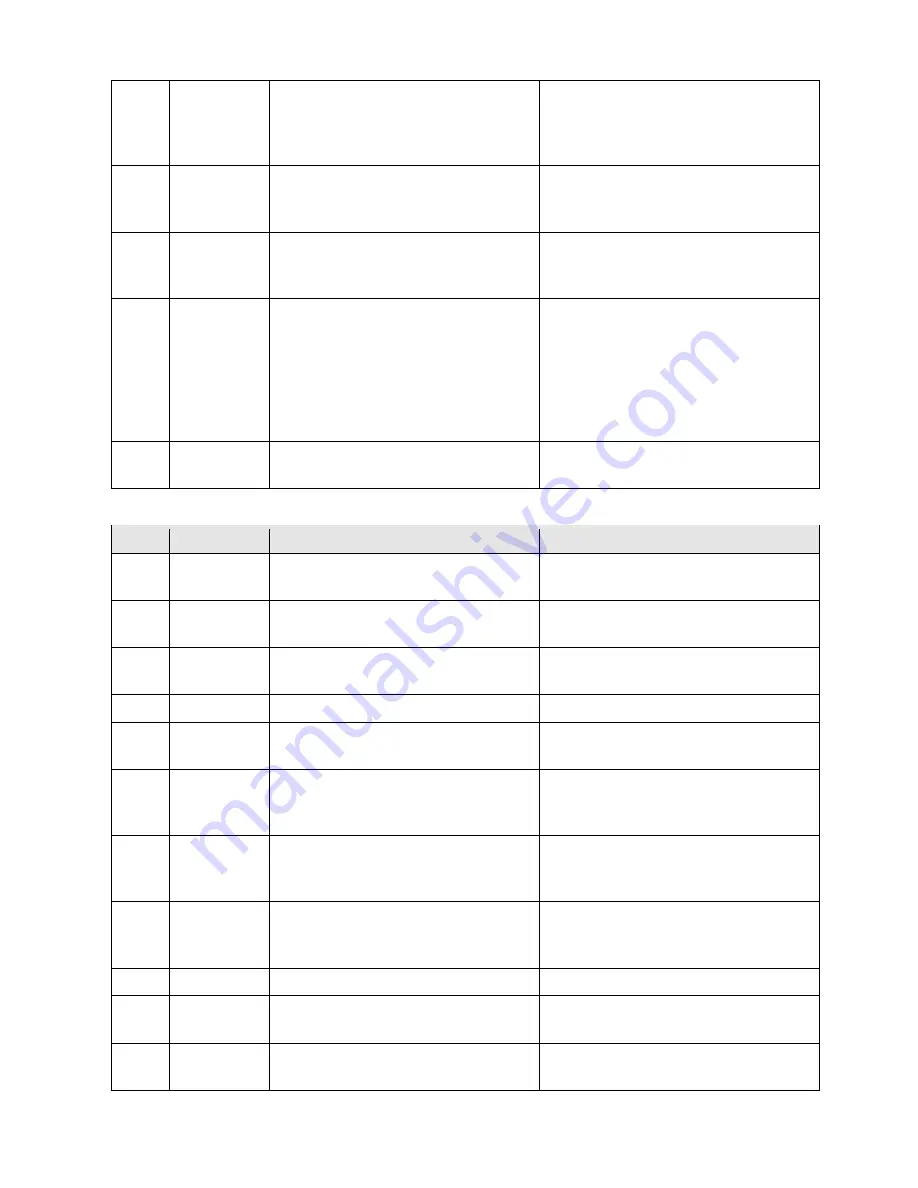
74
Machine equipment stuck or excessive
friction.
Duty cycle of motor overload exceeds the
motor rated performance
is enabled.
Eliminate the problem of mechanical sticking,
add lubricate.
Reduce the acceleration or load inertia.
100.0
Over
frequency
External input pulse frequency is too high.
Reduce pulse frequency.
Increase the value of Frequency_Check
(d3.38).
200.0
Motor
temperature
The motor temperature exceeds the specified
value.
Reduce ambient temperature of the motor and
improve cooling conditions or reduce
acceleration and deceleration or reduce load.
400.0
Encoder
information
1. Communication is incorrect when the
encoder is initialized.
2. The encoder type is wrong, e.g. an
unknown encoder is connected.
3. The data stored in the encoder is wrong.
4. The controller can’t support the current
encoder type.
Check and solve according to the reasons.
800.0
EEPROM data
Data is damaged when the power is turned
on and data is read from the EEPROM.
Data is damaged when data is read from the
EEPROM when the power is turned on.
Table 8-2: Alarm codes of Error_State2 (extended)
Alarm
Name
Reason
Trouble shooting
000.1
Current sensor Current sensor signal offset or ripple too big
Circuit of current sensor is damaged, please
contact the supplier.
000.2
Watchdog
Software watchdog exception
Please contact the supplier and try to update
the firmware.
000.4
Wrong
interrupt
Invalid interrupt exception
Please contact the supplier and try to update
the firmware.
000.8
MCU ID
Wrong MCU type detected
Please contact the supplier.
001.0
Motor
configuration
Motor type is not auto-recognized, no motor
data in EEPROM / motor never configured
Install a correct motor type to the controller
and reboot.
010.0
External
enable
DIN function “pre_enable” is configured, but
the input is inactive when the controller is
enabled or should become enabled
Solve according to the reason.
020.0
Positive limit
Positive position limit (after homing), position
limit only causes error when Limit_Function
(2010.19) is set to 0.
Exclude the condition which causes the limit
signal
040.0
Negative limit
Negative position limit (after homing),
position limit only causes error when
Limit_Function (2010.19) is set to 0.
Exclude the condition which causes the limit
signal
080.0
SPI internal
Internal firmware error in SPI handling
Please contact the supplier.
200.0
Closed loop
direction
Different direction between motor and
position encoder
Change the encoder counting direction
800.0
Master
counting
Master encoder counting error
Ensure that the ground connection and the
encoder shield work well.