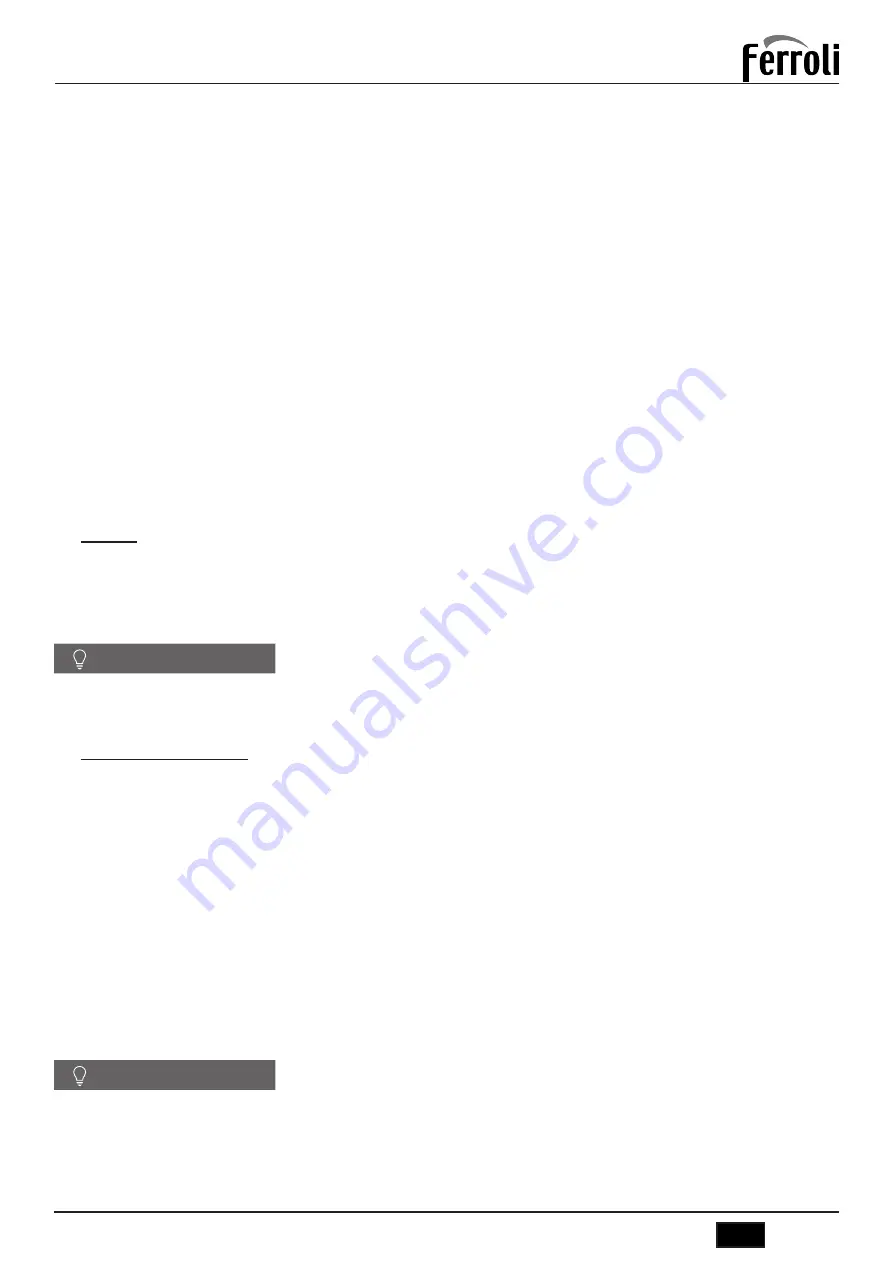
33
EN
Cod. 3542B230 - Rev. 00 - 02/2022
OMNIA S HYBRID H 3.2
The chemical conditioners must ensure complete deoxygenation of the water, they must contain specific protective properties
for yellow metals (copper and copper alloys), anti-scaling agents for limescale, neutral PH stabilisers and, in low-temperature
systems, specific biocides for use in heating systems.
Recommended chemical conditioners:
SENTINEL X100 and SENTINEL X200
FERNOX F1 and FERNOX F3
The appliance features an antifreeze system which activates the heat pump in heating mode when the system supply water
temperature drops below 4 °C. The device is not activated if the electric and/or gas supply to the appliance is removed. If
necessary, use a suitable antifreeze to protect the system which complies with the same requirements indicated previously
in line with the UNI 8065 standard.
If adequate chemical-physical treatments of both system and input water and frequent scheduled checks are carried that can
ensure the required parameters, for industrial process applications only, installation of the product in open vessel systems
is allowed with a hydrostatic pressure height of the vessel that ensures compliance with the minimum operating pressure
indicated in the product technical specifications.
The presence of deposits on the exchange surface of the indoor unit caused by the failure to comply with the above-
mentioned provisions will result in the warranty being voided.
7.5.3 Water filter
It is mandatory to install
a
water filter on the unit input
.
The unit is supplied as standard with two perpendicular taps. The valve with the blue handle has a filter (which can be removed by unscrewing the rear coupling) and
acts, therefore, as a shut-off valve and water filter; this valve should be installed on the system return connection (see detail 11 “fig. 7 - dimensional data and connec-
tions" on page 24). The valve with the red handle should be installed on the system delivery connection (see detail 10 “fig. 7 - dimensional data and connections"
on page 24).
NOTE
The presence of deposits on the indoor unit exchange surfaces due to non-compliance with the above requirements will involve non-recognition of the
warranty.
7.5.4 Tips for a successful installation
For a correct design and installation of the hydraulic plant comply the local laws governing safety matters and sound.
The following information is suggestion for a correct installation of the unit.
• Before connecting the unit to the plant wash adequately the pipes using clean water, filling and emptying and cleaning the filters.
• Only after that proceed connecting the unit to the plant; this operation is crucial to ensure proper start-up without the need to have repeated stops to clean the
filter, with the possible risk of damage to heat exchangers and other components.
• Check by qualified personnel the quality of the water or of the mixture used; avoid the presence of inorganic salts, biological load (seaweeds, etc.) suspended
solids, dissolved oxygen and the pH. Water with inadequate characteristics can cause a pressure drop increase due to a rapid fouling of the filter, energy efficiency
decrease and corrosive symptom increase that can damage the unit.
• The pipes must have the least possible number of bends to minimize load losses and must be adequately supported in order to prevent the connections of the
unit from being excessively stressed.
• Install on-off valves near components that need to be serviced to isolate them when maintenance work needs to be done and to allow them to be replaced without
having to discharge the plant.
• Before isolating the pipes and charging the system, carry out preliminary inspections to make sure that there are no leaks.
• Isolate all the chilled water pipes to prevent condensation from forming along the pipes themselves. Make sure that the material used is the steam barrier type,
failing this, cover the insulation with an appropriate protection. Also make sure that the air venting valves can be accessed through the insulation.
• The circuit can be maintained under pressure using an expansion vessel (present in the unit) and a pressure reducer. A system filling device can be used that
automatically, under a pressure value, provides for the loading and maintenance of the desired pressure.
• Check that all plant components are able to withstand the maximum static pressure (depending on the height of the building to be served).
NOTE
If there is no glycol in the system (antifreeze) or if the unit is not able to remain electrically powered for possible blackouts, in order to avoid possible ic-
ing problems, empty the water during winter.
The unit is only to be used in a closed water plant. Application in an open water circuit can lead to excessive corrosion of the water pipes.
Water connections must be made in accordance with the outlook diagram delivered with the unit, with respect to the water intake and water outlet.
If air, moisture or dust gets in the water circuit, problems may occur. Therefore, always take into account the following when connecting the water circuit.