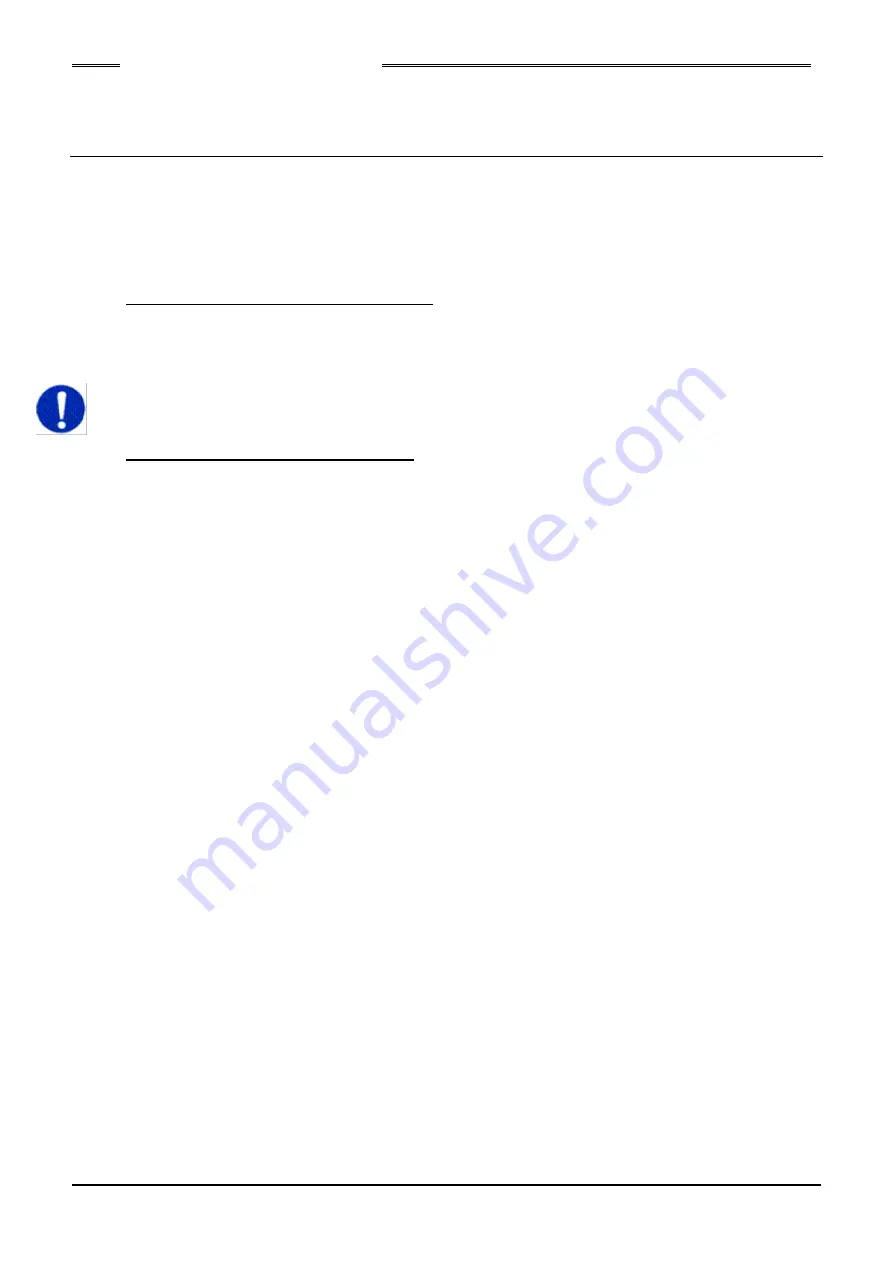
Chapter 6 Fastening Operation
PAGE 6-38
Tubenut Head Operation
When using a Tubenut head, a special function is required to re-align the socket after normal fastening
operations and allow the socket to be placed onto the nut to be fastened. The start trigger must be held
“ON” for the complete fastening of the part. If the trigger is released during the fastening cycle, the
fastening will stop. The fastening can be re-started by simply squeezing the trigger again. Use the
procedures below to re-align the Tubenut socket.
First Time Power-Up / Socket Re-alignment
If the Tubenut socket is not aligned use the following procedure to re-align the open socket.
▪
Select / Press the “Reverse” tool function (Tool RED / GREEN LED’S will flash)
▪
Press the start trigger
▪
Hold the start trigger until the socket is re-aligned and the tool shuts off (tool automatically
shuts off)
NOTE
: If the socket is turning in the wrong direction to re-align the head (Re-alignment must turn CCW for
proper operation), the Gear Head Selection is wrong ([SYS], [D-No]-036).
Return to Home Position after Fastening
After fastening a part, the tubenut socket must be re-aligned in order to remove it from the part. Use the
procedure above to re-align the socket if removal is desired.
Use this procedure to re-align the socket and remove the head from the part after a complete fastening.
▪
Hold down start trigger until fastening is complete
▪
While still HOLDING the start trigger after fastening is complete, lift socket off of the nut being
fastened
▪
Release start trigger and the socket will re-align automatically.
▪
If the trigger is inadvertently released before the socket is re-aligned, follow the procedure
above to re-align the socket.
Summary of Contents for Handheld Nutrunner HFC3000
Page 2: ...www fec usa com Copyright 2017 FEC AUTOMATION SYSTEMS All Rights Reserved ...
Page 14: ...Notes ...
Page 15: ...Chapter 1 Outline PAGE 1 1 Chapter 1 Outline 1 ...
Page 21: ...Chapter 2 Specifications PAGE 2 1 Chapter 2 Specifications 2 ...
Page 28: ...Chapter 2 Specifications PAGE 2 8 Blank Page ...
Page 29: ...Chapter 3 Sysytem Description PAGE 3 1 Chapter 3 System Description 3 ...
Page 36: ...Chapter 3 System Description PAGE 3 8 Memo ...
Page 37: ...Chapter 4 Installation and Wiring PAGE 4 1 Chapter 4 Installation Wiring 4 ...
Page 67: ...Chapter 5 Power Up and Operational Tests PAGE 5 1 Chapter 5 Power Up and Operational Tests 5 ...
Page 71: ...Chapter 6 Fastening Operation PAGE 6 1 Chapter 6 Fastening Operation 6 ...
Page 151: ...Chapter 7 Troubleshooting PAGE 7 1 Chapter 7 Troubleshooting 7 ...
Page 169: ...Chapter 8 Options PAGE 8 1 Chapter 8 Options 8 ...
Page 181: ...Chapter 9 Fieldbus I O Interfaces PAGE 9 1 Chapter 9 Fieldbus I O Interfaces 9 ...
Page 229: ...Chapter 9 Fieldbus I O Interfaces PAGE 9 49 Blank Page ...
Page 230: ......
Page 231: ......