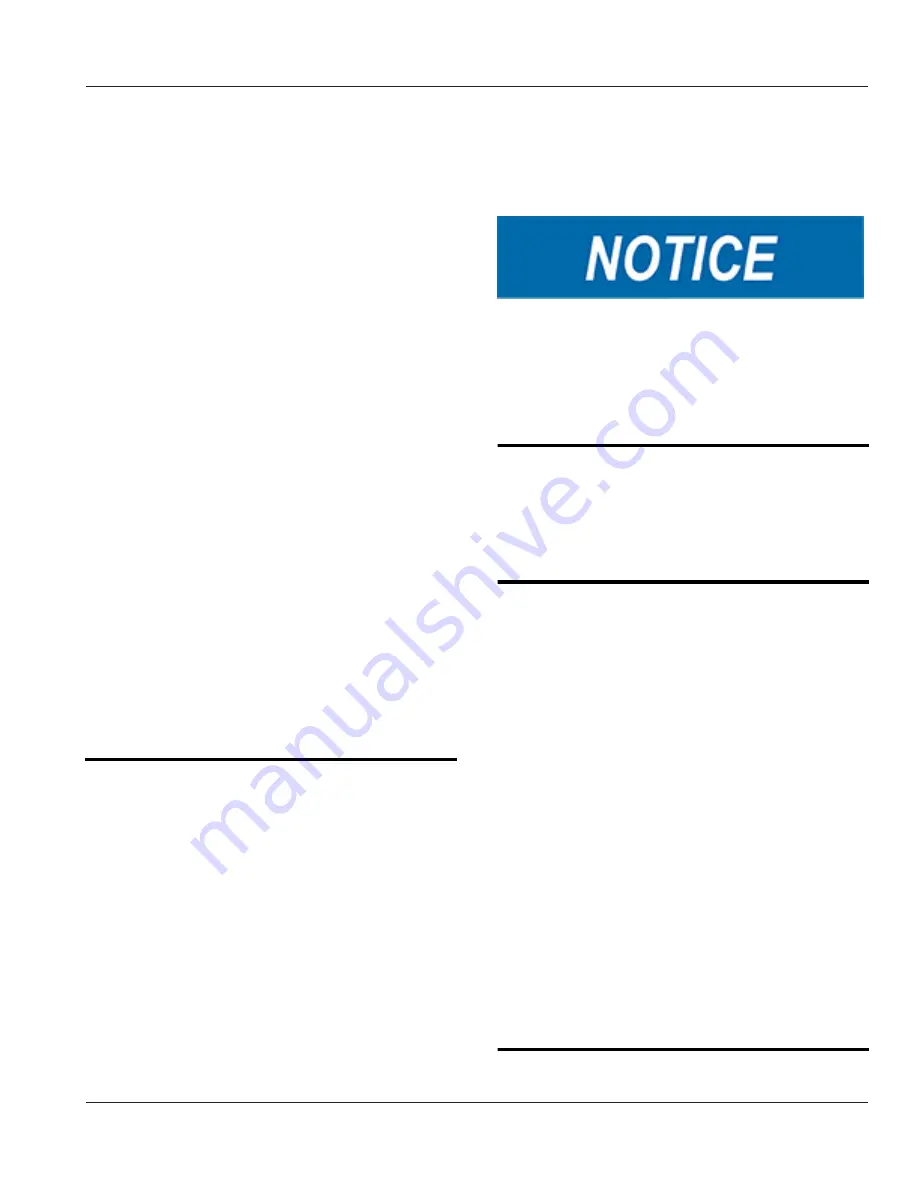
9 Maintenance
Date May 2020
Page 9-5
Operations Manual
CR 820 T
Systems
Electronic Controlled Fuel System
The engine control system is an electronically op-
erated fuel control system that also provides many
operator and equipment features.
The base functions of the control system include
fueling and timing control, limiting the engine speed
operating range between low and high-idle set
points, and reducing exhaust emissions while op
-
timizing engine performance.
The control system uses inputs from the operator
and its sensors to determine the fueling and timing
required to operate at the desired engine speed.
The control system also utilizes a number of sen-
sors to provide information on engine operating pa-
rameters.
The electronic control module (ECM) is the control
center of the system. It processes all of the inputs
and sends commands to the fuel system and en-
gine and equipment control devices.
The ECM performs diagnostic tests on most of its
circuits and will activate a fault code if a problem
is detected in one of these circuits. Along with the
fault code identifying the problem, a snapshot of
the engine’s operating parameters at the time of
fault activation is also stored in memory.
Some fault codes will cause a diagnostic icon to
activate to signal the operator.
Engine Protection System
The engine is equipped with an engine protection
system which monitors critical engine temperatures
and pressures and will log diagnostic faults when
an over or under normal operation condition oc-
curs. If an out-of-range condition exists and engine
derate action is to be initiated, the operator will be
alerted by a WARNING icon. The WARNING lamp
will blink or flash when out-of-range conditions
continue to worsen. When the STOP lamp is illu-
minated, the operator must pull to the side of the
work area, when it is safe to do so, to reduce the
possibility of engine damage.
Engine power and speed will be gradually reduced
depending on the level of severity of the observed
condition until the engine shuts down.
Hydraulic Fluid Reservoir
All filter elements and suction hose fittings should
be checked and tightened regularly to avoid leaks
and prevent air from entering the hydraulic system.
Prolonged operation with air in a hydraulic system
will result in damage to a pump and poor system
performance.
A drain hose is connected to the reservoir to make
changing the hydraulic fluid convenient. The hose
is mounted to the rear bulkhead of the paver. When
draining the reservoir, remove as much of the old
fluid as possible.
Rubber Track Hydraulic System
The rubber track hydraulic system maintains a con-
stant volume of pressurized oil to the piston ends of
track tension cylinders. Each track is independent
and supplied by the auxiliary pump.
When the paver is started, oil is directed from the
auxiliary pump to the pressure reducing valves. Oil
pressure is reduced from 2,500 psi (17,237 kPa)
to 1,900 psi (13,100 kPa) and directed on to the
take-up valves where two separate sections, a
charging/isolation cartridge and a direction sensing
cartridge, route the oil to the track tension release
valves connected to the track tensioning cylinders.
A check valve and accumulator for each track are
placed between the take-up valve charging/isola-
tion cartridge and the piston side of the track ten-
sion release valve. The accumulator is pre-charged
with dry nitrogen at 1,800 psi (12,410 kPa) to allow
the track tensioning cylinders to retract and return if
a severe impact is encountered.
Summary of Contents for Bomag CR 820 T Tier 4
Page 2: ...Intentionally Left Blank ...
Page 3: ...Table of Contents Date May 2020 Page 1 Operations Manual CR 820 T TABLE OF CONTENTS ...
Page 10: ...Table of Contents Operations Manual CR 820 T Date May 2020 Page 8 Intentionally Left Blank ...
Page 11: ...1 INTRODUCTION Date May 2020 Page 1 1 Operations Manual CR 820 T 1 INTRODUCTION ...
Page 16: ...1 INTRODUCTION Operations Manual CR 820 T Date May 2020 Page 1 6 Intentionally Left Blank ...
Page 17: ...2 Safety Date May 2020 Page 2 1 Operations Manual CR 820 T 2 SAFETY ...
Page 38: ...2 Safety Operations Manual CR 820 T Date May 2020 Page 2 22 Intentionally Left Blank ...
Page 39: ...3 Technical Data Date May 2020 Page 3 1 Operations Manual CR 820 T 3 TECHNICAL DATA ...
Page 41: ...4 Operator Controls Date May 2020 Page 4 1 Operations Manual CR 820 T 4 OPERATOR CONTROLS ...
Page 99: ...9 Maintenance Date May 2020 Page 9 1 Operations Manual CR 820 T 9 MAINTENANCE ...
Page 126: ...9 Maintenance Operations Manual CR 820 T Date May 2020 Page 9 28 Intentionally Left Blank ...
Page 127: ...10 Storage Date May 2020 Page 10 1 Operations Manual CR 820 T 10 STORAGE ...
Page 129: ...Intentionally Left Blank ...