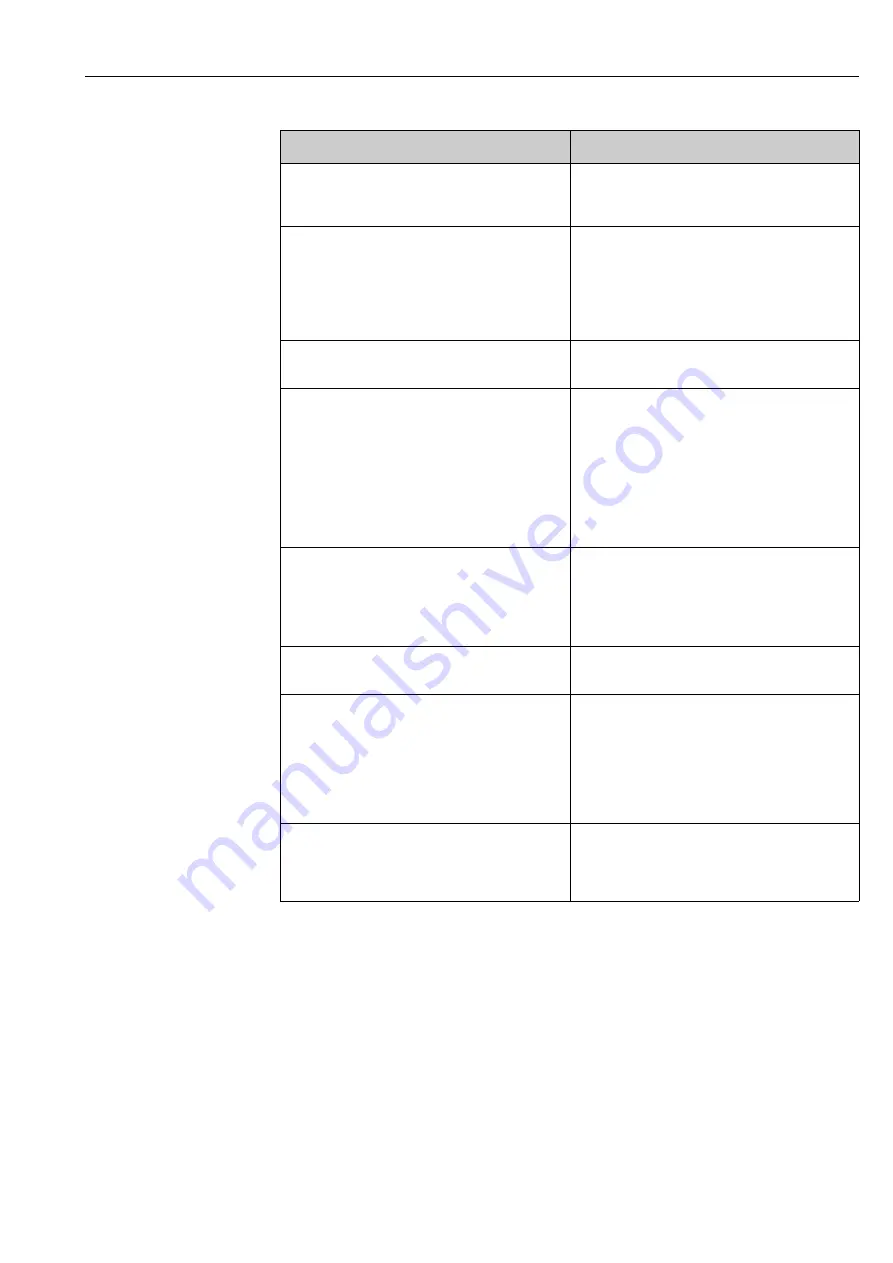
Promag 50
Troubleshooting
Hauser
93
Removing the electrode
Installing the electrode
1
Loosen Allen screw (1) and remove the cover.
1
Insert new electrode (5) into retaining cylinder (7)
from below. Make sure that the seals at the tip of the
electrode are clean.
2
Remove electrode cable (3) secured to handle (2).
2
Mount handle (2) on the electrode and insert
locking pin (8) to secure it in position.
"
Caution!
Make sure that coil spring (11) is inserted. This is
essential to ensure correct electrical contact and
correct measuring signals.
3
Loosen knurled nut (4) by hand.
This knurled nut acts as a locknut.
3
Pull the electrode back until the tip of the electrode
no longer protrudes from retaining cylinder (7).
4
Remove electrode (5) by turning handle (2). The
electrode can now be pulled out of retaining cylinder
(7) as far as a defined stop.
#
Warning!
Risk of injury.
Under process conditions (pressure in the piping
system) the electrode can recoil suddenly against its
stop. Apply counter-pressure while releasing the
electrode.
4
Screw the retaining cylinder (7) onto ball-valve
housing (9) and tighten it by hand.
Seal (10) on the cylinder must be correctly seated
and clean.
!
Note!
Make sure that the rubber hoses on retaining
cylinder (7) and stop cock (6) are of the same color
(red or blue).
5
Close stop cock (6) after pulling out the electrode as
far as it will go.
#
Warning!
Do not subsequently open the stop cock, in order to
prevent fluid escaping.
5
Open stop cock (6) and turn handle (2) to screw the
electrode all the way into the retaining cylinder.
6
Remove the electrode complete with retaining
cylinder (7).
6
Screw knurled nut (4) onto the retaining cylinder.
This firmly locates the electrode in position.
7
Remove handle (2) from electrode (5) by pressing
out locking pin (8). Take care not to lose coil spring
(11).
7
Use the Allen screw to secure electrode cable (3) to
handle (2).
"
Caution!
Make sure that the machine screw securing the
electrode cable is firmly tightened. This is essential
to ensure correct electrical contact and correct
measuring signals.
8
Remove the old electrode and insert the new
electrode.
Replacement electrodes can be ordered separately
from Hauser.
8
Reinstall the cover and tighten Allen screw (a).