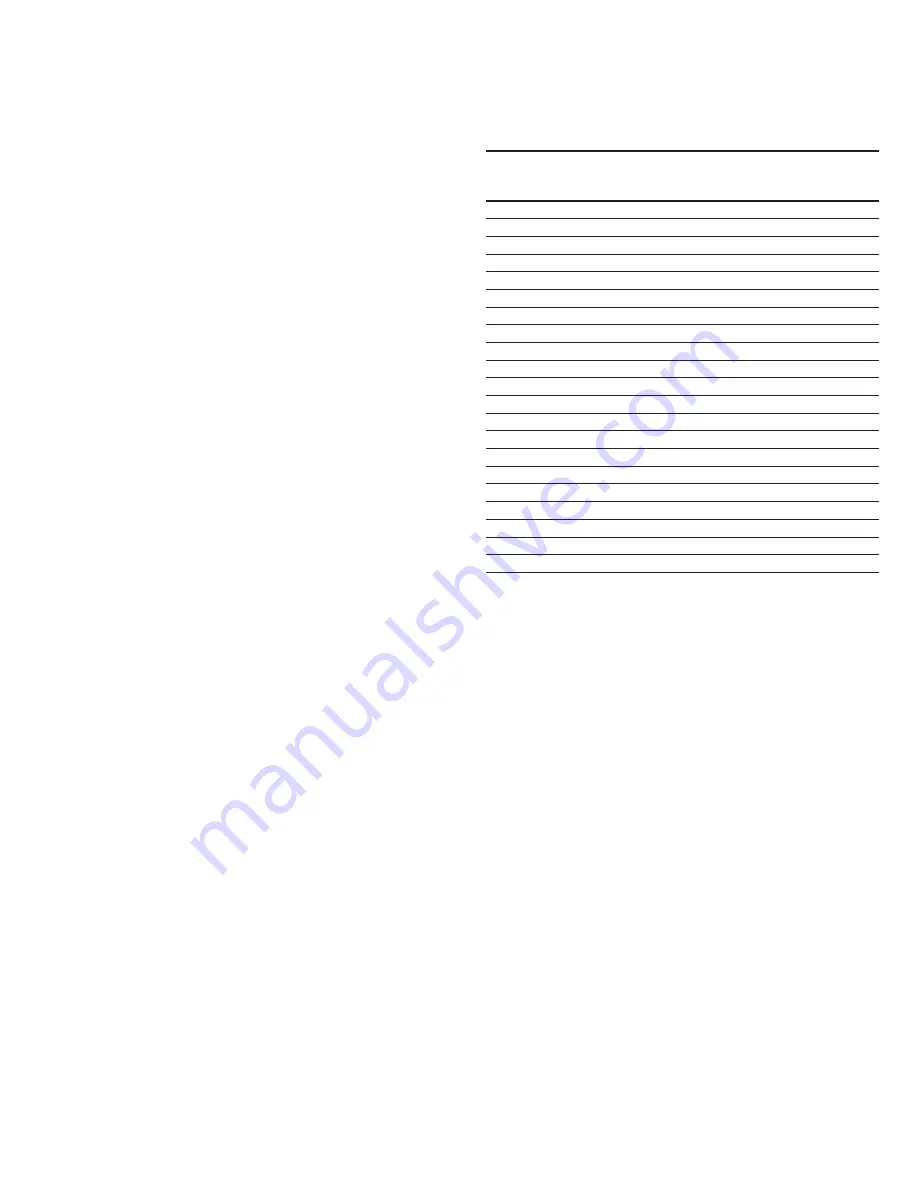
21
EATON
www.eaton.com
Instruction Booklet
IB020003EN
Effective January 2021
AMPGARD RVSS
Reduced Voltage Soft-Starter
User Manual
Section 2: Protection and diagnostics
2.1 Signals
The RVSS controller needs feedback signals in order to properly
control the SCRs in the SCR truck. These signals include current
feedback, and voltage feedback for line phase relationships.
Current feedback for all three phases is provided by current
transformers in a Current Transformer module that is part of the
Ampgard starter cell. The CT secondary signals are connected to
the RVSS current feedback RF filter and routed to the Input/Output
Board for signal conditioning and use. The CT signals may also be
wired to a Motor Protective Relay if furnished.
Voltage feedback for all three phases is obtained from the starter cell
potential transformer. The potential transformer steps primary line
voltage down to 120 VAC and is wired to the Input/Output Board.
These signals may also be wired to a Motor Protective Relay if
furnished.
Control (start, stop) signals are received from one of two sources:
•
Local (defined during configuration),
•
Remote (defined during configuration).
In general, the Local control source is the MUI, the Monitoring User
Interface. During configuration, the Local control source must be
selected from a list of potential local control sources.
The Local and Remote Control Place is configured in the parameters.
Local Control can be No Local Control (to force Remote), Monitor
User Interface (MUI), or Field-Wire. The Remote Control can be No
Remote Control (to force Local), Field-Wire, or FieldBus. When the
unit is in Remote control the PC Power xPert inControl control panel
can be used to Start and Stop the Starter.
2.2 Protection
In addition to providing status information for RVSS control, voltage
and current feedback signals are used for RVSS system and motor
protection.
RVSS protection features are an inherent part of the system, and are
available whether or not the RVSS has been furnished with a Motor
Protective Relay. The protective features include E-Stop detection,
RVSS Instantaneous Overcurrent, Motor Jam, Pre-Start Check
Fault, Overload, Incomplete Sequence, RVSS Overtemperature,
Starts Limit Exceeded, Undervoltage, Overvoltage, Overfrequency,
Underfrequency, Phase Rotation Mismatch, Main Contactor Failed to
Close, Bypass Contactor Failed to Close, No Ramp Type is Selected,
and Motor Instantaneous Overcurrent.
shows the protections provided in the AMPGARD RVSS,
their ANSI fault codes and their application during various operation
modes.
Table 4. RVSS protection
Protection
ANSI
code
Fault
code Motor control states
St
an
dby
Pre
-
St
ar
t
St
ar
t
ram
p
Cl
os
e
by
pa
ss
St
op
ram
p
E-stop
1
1
X
X
X
X
X
RVSS instantaneous Overcurrent
50/51
2
X
X
X
X
Motor Jam
50/51
22
X
Pre-Start check fault
86
4
X
Overload
49
5
X
X
X
X
Incomplete sequence
48
6
X
RVSS overtemperature
23
7
X
X
X
Starts limit exceeded
66
8
X
Undervoltage
27
9
X
X
X
X
X
Overvoltage
59
10
X
X
X
X
X
Overfrequency
81
11
X
X
X
X
X
Phase rotation mismatch
46, 47
13
X
X
X
X
Main contactor failed to close
4/39
14
X
X
X
Bypass contactor failed to close
4/39
15
X
X
X
X
No ramp type is selected
34 (?)
18
X
Residual ground fault
51G
12
X
X
X
Truck overload
49
19
X
X
Voltage 1ph/unbalance
47
20
X
X
X
X
X
Current 1ph/unbalance
46
21
X
X
X
X
Motor jam IOC
51
22
X
External fault
23
X
X
X
X
X
2.2.1 E-stop
External signals can initiate an RVSS emergency stop. Emergency
stop immediately opens the main (starter cell) contactor so that
the motor coasts to a stop. The external signals that can initiate an
E-stop include:
•
a local pushbutton, or
•
a normally-closed external contact that opens when an E-stop is desired.
E-stops inhibit all RVSS functions. The BCM must be reset (E-stop
signal no longer present, all permissives satisfied) before an RVSS
start can be initiated once again.
2.2.2 RVSS Instantaneous overcurrent
The RVSS controller utilizes a hard-coded SCR truck instantaneous
overcurrent trip set at 550% of the RVSS continuous RMS rating
for one cycle, and is not dependent upon motor FLA. A detected
overcurrent in any of the phases will immediately trip the RVSS
and starter and provide fault information on the MUI graphic user
interface.
2.2.3 Motor jam
Jam detection is a motor current monitoring function that looks for
overcurrents in the range of 90% - 300% of motor FLA. It is enabled
whenever the RVSS has completed a start and is running in Bypass.
If such a load is detected, a settable delay timer is invoked. If the
overcurrent exceeds the monitoring threshold for longer than the
set time delay, the RVSS is fault stopped and an alarm message is
displayed.
2.2.4 Pre-Start check faults
Whenever a start is initiated, if starting permissives are satisfied,
the main contactor closes and the RVSS performs a series of tests
to determine system integrity. This patented Pre-Start check process
addresses the SCR truck power components and includes tests for
SCR short-circuit fault,
•
Load side single line to ground fault,