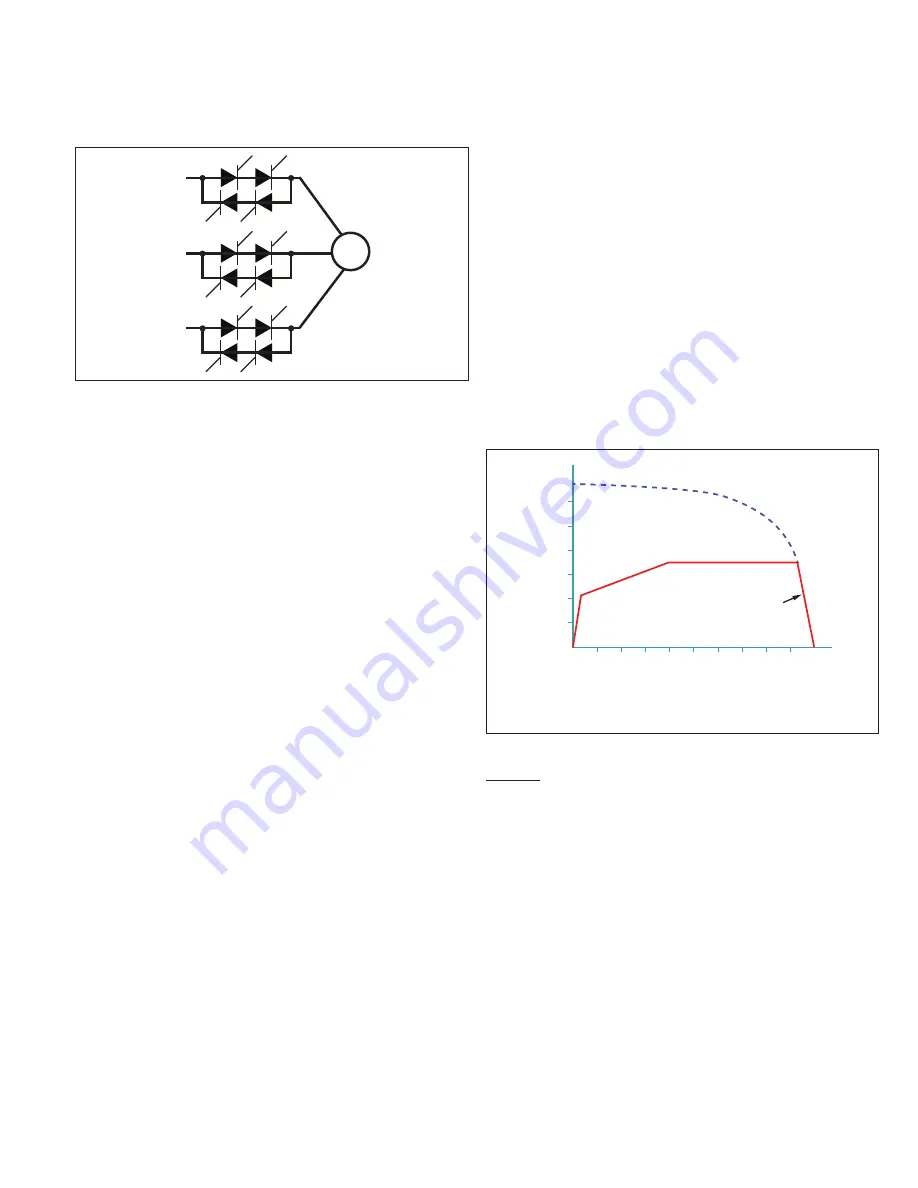
15
EATON
www.eaton.com
Instruction Booklet
IB020003EN
Effective January 2021
AMPGARD RVSS
Reduced Voltage Soft-Starter
User Manual
A complete soft starter SCR truck has all three phases included, and
is connected to the motor in this way:
Figure 4.
anode
cathode
gate
SCRs wired for three-phase soft start operation.
Additional SCRs may be wired in series-parallel for greater
operational voltage or current. Firing control of the SCRs is achieved
by fan-out and gate-drive boards that distribute the fiber optic gating
signals from the low voltage control components to the SCR gates.
See
and
.
1.4.4.2
SCR ratings when used in soft starters
RVSS soft starters operate as starters, not continuous duty power
converters, and they are cooled by convection. Their power ratings
reflect the thermal limitations of their SCRs. SCR temperature rise
limitations determine how long the SCR truck can be operated
during a start. Factors that will affect the time an SCR truck can
operate are, besides the ambient temperature and altitude,
•
motor FLA current
•
current required at the start
•
time spend during the start cycle
•
number of starts per hour
•
rest (cooldown) interval between starts.
1.4.4.2
Soft starter control operation
The power of the soft starter is in the controller DSP, a
microprocessor based protection and control system for the motor
and starter assembly. The DSP uses Phase Angle Firing of the SCRs
to apply a set initial voltage to the motor, and then increases motor
torque through control of the voltage and current until full speed
is reached. This starting method lowers the motor starting current,
reducing electrical stresses on the motor and power system. It
also reduces starting torque stresses on both the motor and load
mechanical components, promoting longer service life and less
downtime.
The starting sequence for the starter is:
1. The main contactor closes and the SCRs are gated on to
provide controlled voltage to the motor, with overload,
overcurrent and instantaneous overcurrent protection.
2. When the motor nears full speed, and the motor current
begins to decline, the starter closes the Bypass contactor,
shunting line voltage around the SCR bridge and directly to
the motor. The SCRs are switched off. The start sequence is
complete.
The RVSS can be configured for operation using any one of several
starting and stopping modes. The starting modes include Voltage
Ramp with Current Limit, Current Ramp, Pump Start, Kick Start, Jog
Forward, Jog Reverse, Emergency Full Voltage Start, and Voltage
Ramp with Limited Voltage Sag. The stopping modes include Coast
Stop and Linear Deceleration.
1.5 Starting modes
The AMPGARD RVSS can be configured for different starting
modes, depending upon the needs of the application. Following are
descriptions of these modes.
1.5.1 Voltage ramp with current limit
The factory default starting mode, Voltage Ramp with Current Limit
combines two control profiles.
With this starting method, the main contactor closes and the SCRs
deliver voltage to the motor that follows a set program of Initial
Voltage, Start Ramp Time, and Current Limit operation. At first, the
starter puts out a voltage chosen to just get the motor turning (Initial
Voltage).
The starter then increases its output voltage following a
programmed rate (Start Ramp Time) until either the motor reaches
the Bypass time or the motor current reaches the set Current Limit
value. At that point, output voltage is programmed to hold the motor
current at the current limit value as the motor accelerates until the
motor reaches the transition current threshold %.
If the motor reaches the transition current threshold % before the
Voltage Ramp has completed, the RVSS will transition to Bypass and
complete the start. See
Figure 5.
Voltage R
amp
Motor Speed %
Motor Cur
rent
% of F
ull L
oad
Current at Full Voltage
Preset Current Limit
Initial
Voltage
Voltage Ramp with Current Limit Mode
10
20
30
40
50
60
70
80
90 100
700
600
500
400
300
200
100
Transition Current
Threshold %
(default 185% - aka
UTSD up-to-speed
detection)
Voltage ramp with current limit mode.
Kick Start
Kick start is a selectable option for Voltage ramp with current limit.
Kick start begins the start, not with the Initial Voltage used in the
basic Voltage Ramp with current limit, but instead with a pulse of
voltage of a much higher value for a short time. After the short
voltage pulse, the output voltage is reduced to the initial voltage
value, and the start progresses with a voltage ramp to current limit
(see
)
The value of Kick Start voltage is often determined by experiment,
during commissioning, by jogging the motor at gradually increasing
jog voltage settings until the motor and load break away and start to
rotate.
When configuring the Kick Start function, the RVSS controller will
need the Kick Start voltage needed, and a value for how long the
kick is to be applied. This time is expressed in cycles of line voltage.
This function should be used only when necessary, and approached
with caution. The value of Kick Start voltage can be set near to full
voltage, and Current Limit is inhibited, which would result in initial
motor currents very near what it would see with an across the line
start.