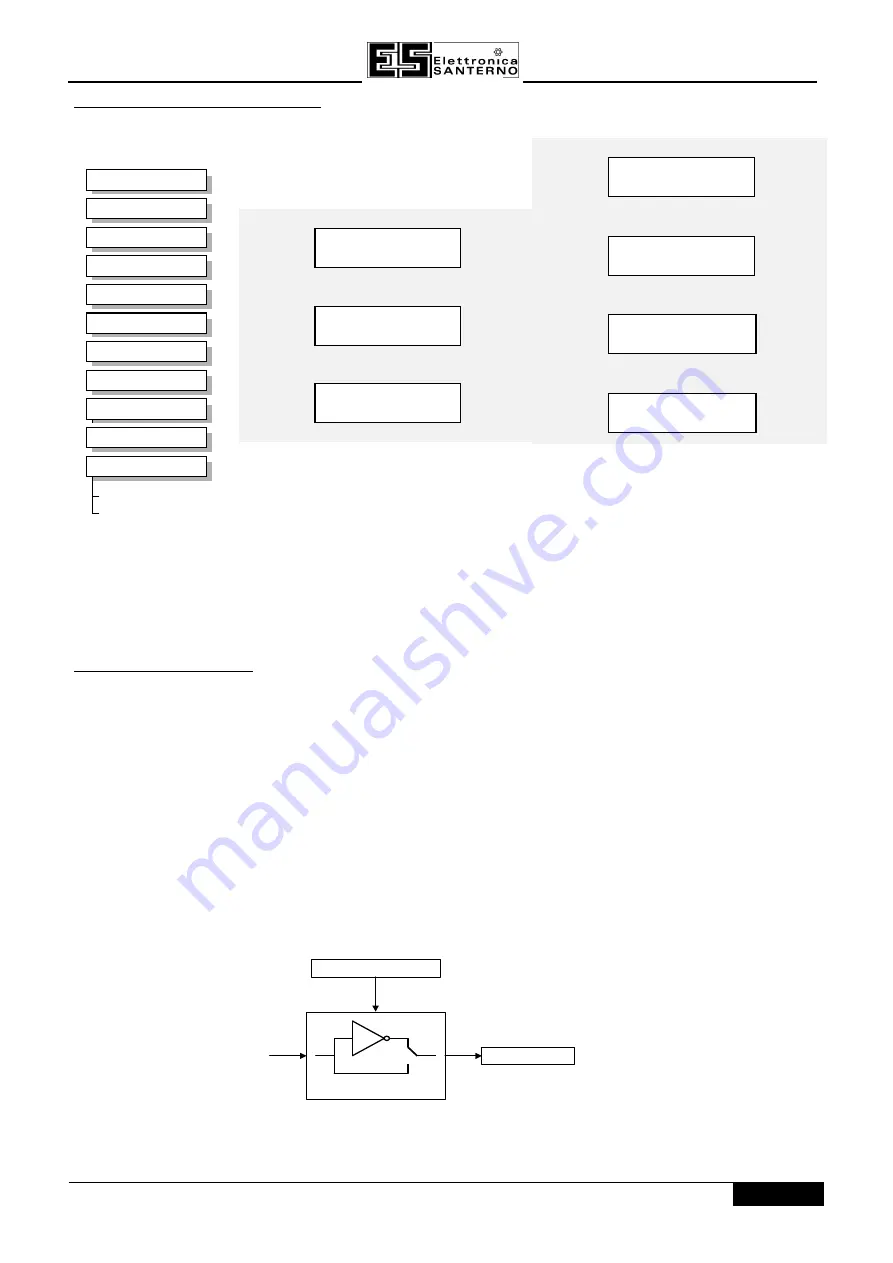
SINUS/ISD
15P0082B8
6 - 23
6.4.1.12
Functional Description
The Inverter has seven digital inputs. There is a DIGITAL INPUT function block associated with each of these:
DIGITAL INPUT 2 is associated with terminal 8
DIGITAL INPUT 3 is associated with terminal 9
DIGITAL INPUT 5 is associated with terminal 11
DIGITAL INPUT 6 is associated with terminal 16
The input electronics of the Inverter converts the input signal to a TRUE or FALSE logic value. The digital input
block takes this value and optionally inverts it before providing the VALUE output.
7
SETUP PARAMETERS
2
3
4
5
5
5
5
5
5
5
DIN 7 INVERT
Parameter Descriptions
INVERT
Range: FALSE / TRUE
VALUE
Range: FALSE / TRUE
INPUT
VALUE
INVERT
UNPROCESSED
DIGITAL INPUT 2
VALUE [ 34]
–
FALSE
FALSE – [ 33] INVERT
–
DIGITAL INPUT 4
VALUE [ 40]
–
FALSE – [ 39] INVERT
–
DIGITAL INPUT 6
VALUE [726]
–
FALSE – [725] INVERT
–
DIGITAL INPUT 1
DIGITAL INPUT 1
VALUE [ 31] –– FALSE
FALSE
[ 30] INVERT
––
DIGITAL INPUT 3
VALUE [ 37] –– FALSE
FALSE – [ 36] INVERT
–
DIGITAL INPUT 5
DIGITAL INPUT 5
[ 43] –FALSE
– [ 42]
––
DIGITAL INPUT 7
DIGITAL INPUT 7
VALUE [728] –FALSE
FALSE [727] INVERT
––
Summary of Contents for SINUS/ISD 200 S-0.75
Page 56: ...15P0082B8 USER MANUAL SINUS ISD 5 14 14...
Page 144: ...15P0082A8 USER MANUAL SINUS ISD 8 2 2...
Page 166: ...15P0082B8 USER MANUAL SINUS ISD 10 16 16...
Page 180: ...15P0082B8 USER MANUAL SINUS ISD 12 8 8...
Page 184: ...15P0082A8 USER MANUAL SINUS ISD 14 2 2...
Page 186: ...15P0082B8 USER MANUAL SINUS ISD 15 2 12 MACRO1 MACRO1...
Page 188: ...15P0082B8 USER MANUAL SINUS ISD 15 4 12 MACRO2 MACRO2...
Page 190: ...15P0082B8 USER MANUAL SINUS ISD 15 6 12 MACRO3 MACRO3...
Page 192: ...15P0082B8 USER MANUAL SINUS ISD 15 8 12 MACRO4 MACRO4...
Page 194: ...15P0082B8 USER MANUAL SINUS ISD 15 10 12...
Page 195: ...SINUS ISD 15P0082B8 USER MANUAL 15 11 12...
Page 196: ...15P0082B8 USER MANUAL SINUS ISD 15 12 12...
Page 200: ...15P0082B8 USER MANUAL SINUS ISD 16 4 10...