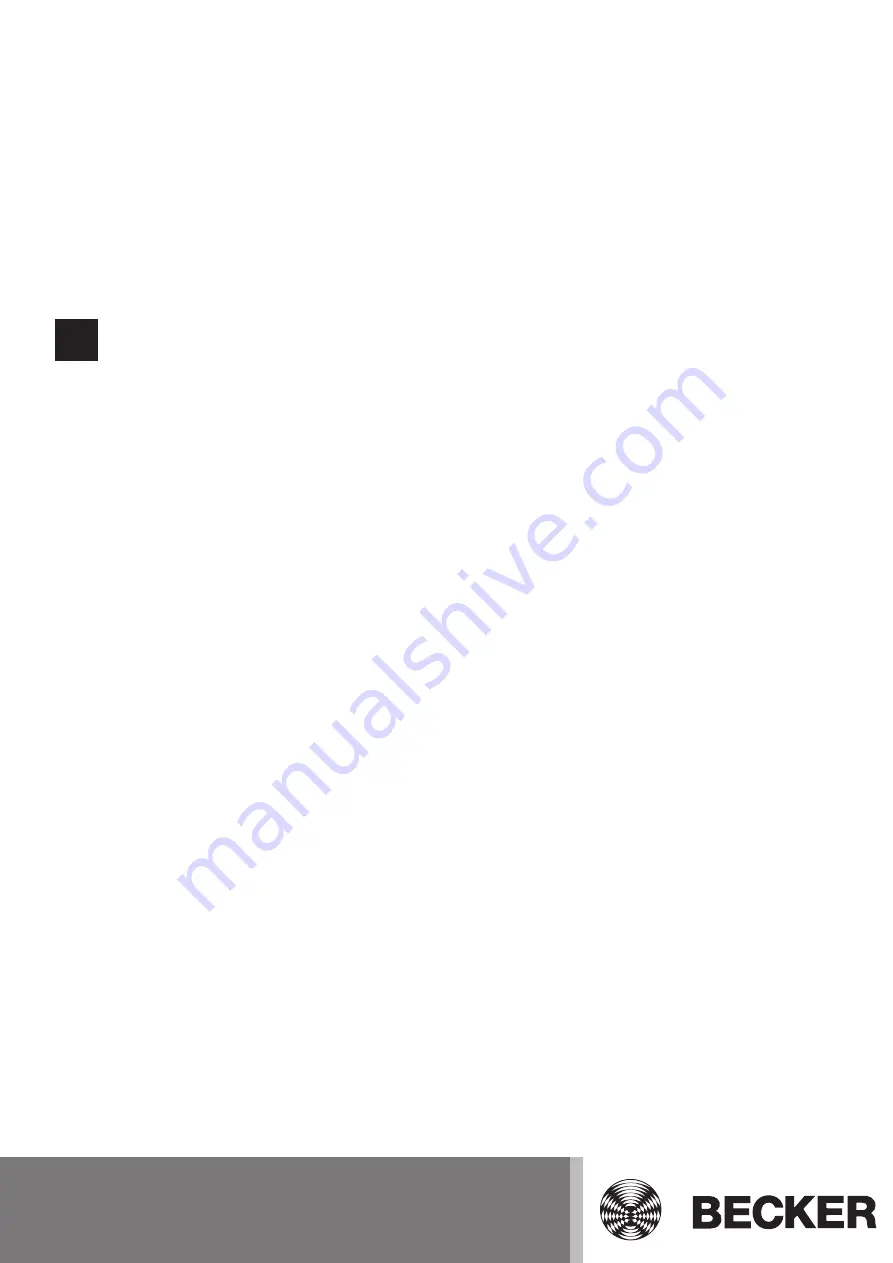
P5-20...R40-17
Model: C18
en
Assembly and Operating Instructions
Tubular drive with integrated radio receiver for ZIP
systems
Important information for:
• Fitters / • Electricians / • Users
Please forward accordingly!
These instructions must be kept safe for future reference.
Becker-Antriebe GmbH
Friedrich-Ebert-Straße 2-4
35764 Sinn/Germany
www.becker-antriebe.com
2010 300 901 0b 14/07/2022
Summary of Contents for C18
Page 19: ...Sample wiring diagram N L PE Electronics Black Brown Blue Green yellow 19 en ...
Page 20: ...Declaration of conformity 20 en ...
Page 21: ...21 ...
Page 22: ...22 ...
Page 23: ...23 ...
Page 24: ......