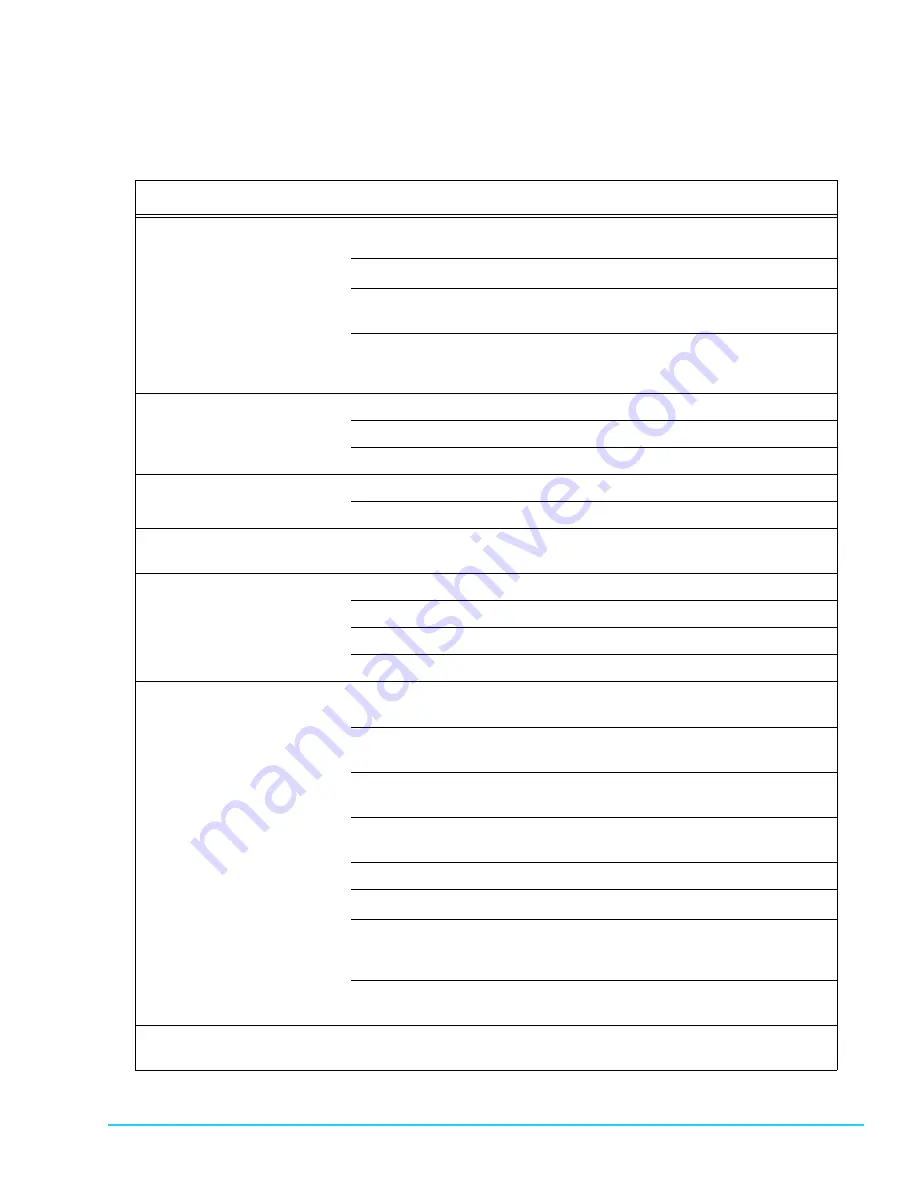
. . . . .
2-9317-372-00-0
Bravo™ 8105 Programming and Operations Guide
8-121
0
0
0
0
0
0
0
0
0
0
Section C: Reflow Process Troubleshooting Table
Problem
Possible Cause(s)
Uneven Soldering, Localized Cold
Joints
Large temperature differential
a
Insufficient heat; raising the maximum reflow temperature may resolve the problem.
b
Inadequate cleaning of the PCB prior to soldering may not allow fluxing action sufficient
for the soldering process
c
If a higher mass part does not solder, there may be insufficient time/temperature in the
soak zone.
d
Due to the larger mass, it has to have adequate thermal preparation for
reflow.
Incomplete Fillets
Excessive rate of heating
Insufficient solder paste
Low metal content in solder paste
Open Joints
Misaligned component
Screen/stencil may be clogged
Cracked and Damaged Chip Capaci-
tors and Connections
Cracking is typically caused by physical stress on the component from too much solder
in the leads, combined with rapid thermal cycling.
e
Grainy Solder
Leaching (Dissolution of a metal coating into liquid solder.)
Board or component contamination
Composition of paste alloy may be incompatible with process
Solder particle size may be too small for the process
Solder Balls
Inadequate fluxing activity due to elevated temperatures or excessive times at that tem-
perature
f
. A slower preheat rate and/or lower reflow peak may reduce the effect.
High–gloss solder mask
g
. Using a liquid photoimagable product may yield higher quailty
passes.
Ambient humidity
h
. Inspect to determine when the humidity causes unacceptable yields
and stop production or install environmental control equipment,
Too rapid rise in preheat temperature
i
; temperature ramp rate too high.
j
Note that too
slow of a preheat may cause the paste to oxidize.
Not reaching an adequate maximum temperature in preheat
Moisture–contaminated solder paste; analyze the alloy.
k
Solder paste viscosity may be too low, or the solder paste oxidized. Powder failure,
occurs when reactive and protective character of the flux is affected. Not recoverable.
l
Check the receiving report to ensure that the paste was properly handled.
Paste sat on boards too long before reflow and degraded. Use a newly printed board to
verify problem is corrected.
m
Solder Beading
Reflow profile ramp rate too low, which allows capillary action drawing the paste away.
Correct the ramp rate.
n