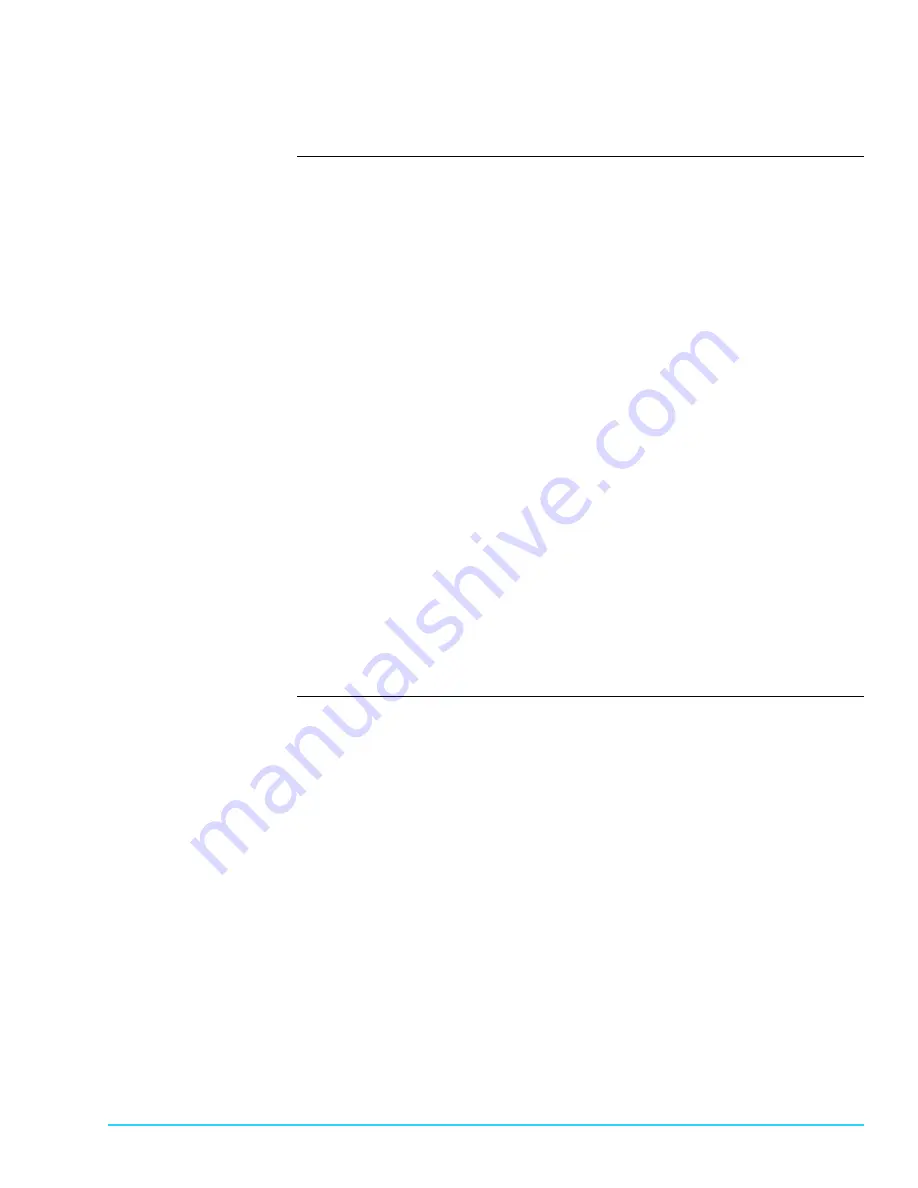
. . . . .
A C C O M P L I S H I N G T H E R E F L O W P R O C E S S
Solder Paste Considerations
2-9317-372-00-0
Bravo™ 8105 Programming and Operations Guide
11-115
Solder Paste Considerations
Factors to Consider
When considering a solder paste, there are five (5) factors to take into
consideration:
• Solder Alloy
• Powder Type
• Metal Percent
• Flux Type
• Packaging Requirements
The weight ratio of powder to flux is the metal percent and determines the paste
viscosity.
Ninety percent (90%) of surface mount applications use a eutectic alloy
containing 63 percent tin and 37 percent lead (Sn63/Pb37).
The size of the spheres in solder paste is often referenced by a mesh size. Solder
is sifted through meshes of known size, and categorized accordingly. If a solder
can pass through a 200 mesh screen (a screen that has 200 openings per inch),
the solder is referred to as minus that screen size, or –200. If the solder is too big
to fit through the screen, it is described as plus that screen size. So if the solder
wouldn’t pass, for example, through a 500 mesh screen, the solder is referenced
as +500. Therefore a solder that passed through a 325 mesh screen but not a
400 mesh screen would be categorized as –325/+500. If a solder sphere passes
through a 200 mesh screen (a screen that has 200 openings per inch), the solder
is referred to as minus that screen size, or –200. If the solder is too big to fit
through the screen, it is described as plus that screen size. So if the solder
wouldn’t pass, for example, through a 500 mesh screen, the solder is referenced
as +500. Therefore a solder that passed through a 325 mesh screen but not a
400 mesh screen would be categorized as –325/+500.
Before Using Solder
Paste
Check the labels of the paste to ensure it is correct, and ensure that the date is
within allocated time. If the solder is packaged a jar check for separation,
skinning, and lumps.
Separation is not normally a problem if it’s possible to mix the flux back into the
balance of the material. Each solder paste has a temperature that causes it to
separate (necessary for proper reflow during the heating process).
Separation is more of a problem in a cartridge because it’s difficult to remix the
solder paste. Large amounts of separated flux need to be reported to the supplier.
Alternate packing or shipping practices may alleviate the problem.
A hard crust formation on the surface of the solder paste is referred to as
skinning. It flakes or chunks when probed with a utensil. Skinning is irreversible.
It is a by–product of oxygen reacting with the rosin in the paste. Unless the entire
surface label is able to be removed, the contents are useless.
Lumps can be caused by several things, and the effect on the solder paste varies.
Lumps caused by thickening of the flux is generally not a problem. Simply stirring
the paste should make it smooth again. Lumps from congealed flux, undissolved
flux components, skinning that was mixed in, or other contaminants, presents
more of a problem. It is recommended to contact the supplier.