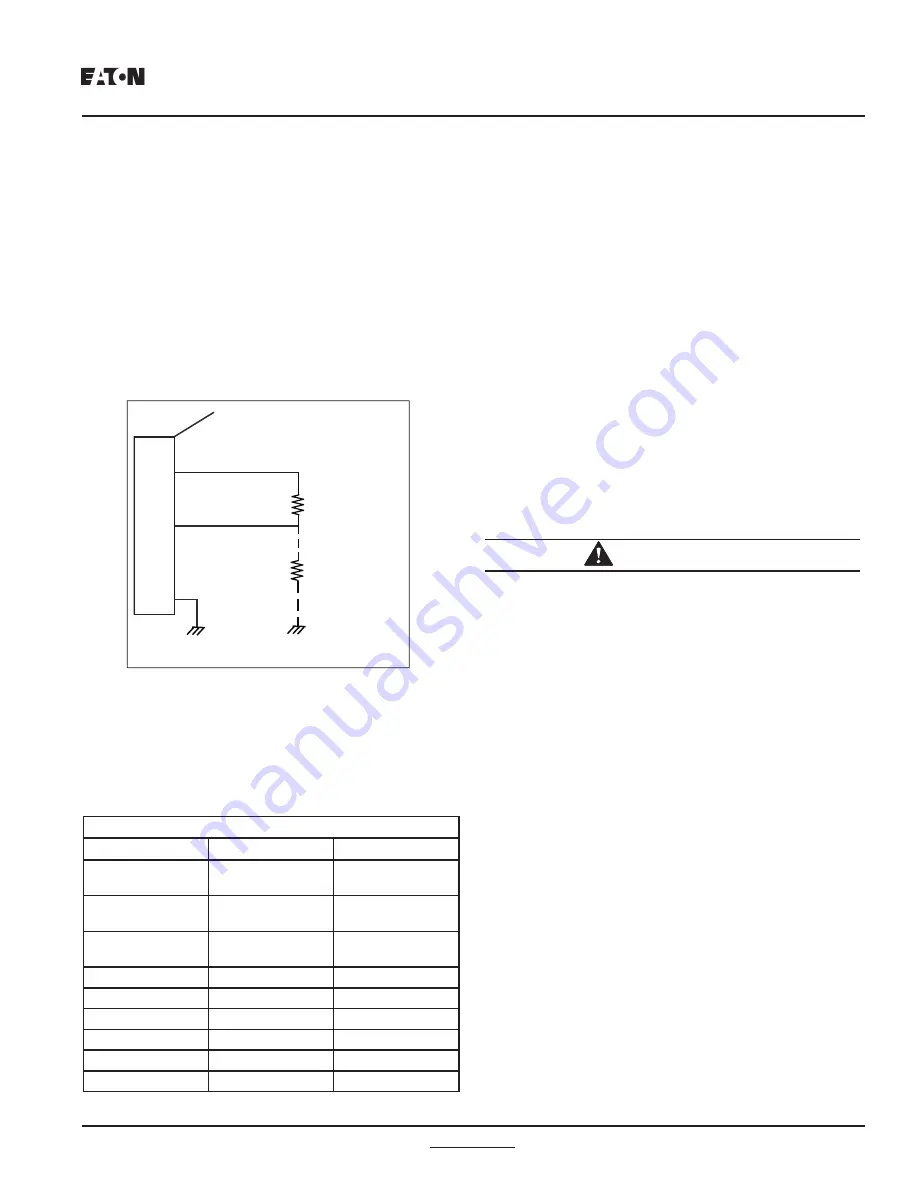
www.eaton.com
Page
6-3
MP-4000
IB02602002E
6.1.6
analog Output Wiring
Terminals 24 and 25 provide an isolated source of dc current between
4 and 20 mA, the exact value indicating an internal MP-4000 measure
-
ment. This current source, if used, is typically connected to a remote
panel meter or a programmable logic controller.
The measurement selection is made via an MP-4000 setting. Choices
include motor current, stator winding temperature, and fill level of the
rotor thermal model bucket between cool level and trip level (refer to
setting P11L1 in Section 5).
The burden of the connected current loop should be less than 1,000
ohms. See the Analog Output Technical Specification in Section 3 and
Figure 6.1.
NOTE:
The external device driven by the analog output must be fully
isolated. The resistance to ground of the circuit driven by the
analog output must be greater than 1 megohm. The accuracy
of the analog output decreases rapidly below 1 megohm.
6.1.7
URTD Wiring
Connect a source of 120 Vac only to the power terminals of connector
J3 on the URTD module. Connect either terminal 16 or terminal 32
(but not both) to a non-current-carrying safety ground.
Figure 6.10 shows connections between the URTD and the MP-4000.
Use either the optical fiber or the electrical 3-wire connection. It is not
necessary to connect both. If both are connected, the MP-4000 uses
data from the optical fiber. It defaults to the wired connection, only if
the fiber is removed or fails.
NOTE:
The optical fiber is the preferred method of transmitting tem
-
perature data from the URTD to the MP-4000. It is also easier
to install.
Preassembled plastic optical fibers with connectors can be ordered
from Eaton Inc., or from any distributor of Agilent Technologies
®
optical
fiber products. In addition, these same distributors offer long rolls of
cable with connectors that can be installed in the field. Some distribu
-
tors will make custom lengths to order.
The fiber length should not exceed 400 ft (121.9 m). For long runs
over 33 ft (10 m), be sure to use H-P extra low loss plastic fiber HBFR-
ELS or -EUS. Do not splice fiber. Maximum short-term pulling force is
11.3 lbf (50 N). Surplus length of a precut fiber causes no problems.
Simply coil and tie the excess fiber at a convenient point. Avoid high
tie pressure. The bending radius of the fiber should be greater than
2 in. (50.8 mm). The fiber terminations simply snap into or out of the
connectors of the URTD and MP-4000.
When using 3-wire shielded cable, wire according to the connection
guidelines in Table III of the Universal RTD Module IL 17367. The
3-wire shielded cable should be #16 AWG or #18 AWG (1.31 mm
2
or
0.823 mm
2
). Connect the cable shield
only
at the MP-4000 end, at ter-
minal 23. Insulate the shield, and do not connect it at the URTD end.
CaUTION
IF ThE MP-4000 IS SUPPlIED FROM 240 VaC, ThE URTD COM-
MUNICaTIONS COMMON TERMINal 22 IS aT 120 VaC WITh
RESPECT TO ThE SUPPly NEUTRal.
The maximum cable length is 500 ft (152 m).
6.1.8
Wiring RTDs to the URTD Module
Consult URTD Module Instruction Leaflet I.L.17367.
Three URTD terminals are provided for each RTD input. Terminals
1-15 and 17-19 are inputs for up to 6-winding RTDs. Terminals 20-25
accept up to two motor bearing RTDs. Terminals 26-31 accept up to
two load bearing RTDs. Terminals 33-35 accept an auxiliary RTD.
The three terminals for any unused RTD input channel should be
wired together. For example, if MW5 and MW6 are unused, MW5
terminals 13-15 should be wired together; and MW6 terminals 17-19
should be separately wired together.
Figure 6.12 shows the wiring of RTDs to the URTD inputs. Use
#18 AWG (0.823 mm
2
), three-conductor shielded cable. Note the con
-
nection rules in the figure. When making connections to a two-lead
RTD, connect two of the cable conductors to one of the RTD leads as
shown. Make this connection as close to the motor as possible. Con-
nect the third cable conductor to the remaining RTD lead.
Connect the shield and drain wire, along with the one cable conduc
-
tor, to the middle of the three RTD input channel terminals, as shown
in Figure 6.12. The RTD cable shield should be connected only at
the URTD end, and insulated at the RTD end. The RTDs themselves
must not be grounded at the motor.
Remember to set the URTD module DIP switches according to the
types of RTDs in each of the winding, motor bearing, load bearing,
and auxiliary groups. Refer to URTD Module Instruction Leaflet
I.L. 17367.
Table 6.1 Eaton Cutler-hammer agilent Technologies Cabling.
Length (Meters)
Catalog Number
Number
1
MPFO-1
HBFR-ELS001 or
HBFR-RLS001
5
MPFO-5
HBFR-ELS005 or
HBFR-RLS005
10
MPFO-10
HBFR-ELS010 or
HBFR-RLS010
25
MPFO-25
HBFR-ELS025
50
MPFO-50
HBFR-ELS050
75
MPFO-75
HBFR-ELS075
76
MPFO-76
HBFR-ELS076
100
MPFO-100
HBFR-ELS100
120
MPFO-120
HBFR-ELS120
+
Ω
1,000
-
25
24
R
burden
>1M
Ω
See Figure 6.6 for Terminals
00
04-
P
M
K
C
OL
B
LA
NI
M
RE
T
>
R
parasitic
NOTE: Rparasitic represents unintentional, parasitic resistance
to ground and is not an actual connection.
Figure 6.1 Max. Burden - Characteristics of
an attached Device.
Summary of Contents for MP-4000
Page 6: ...Page vi www eaton com IB02602002E MP 4000 This Page Intentionally Left Blank...
Page 56: ...Page 5 16 www eaton com IB02602002E MP 4000 This page intentionally left blank...
Page 60: ...Page 6 www eaton com IB02602002E MP 4000 Figure 6 2 Panel Cutout Dimensions...
Page 64: ...Page 6 www eaton com IB02602002E MP 4000 Figure 6 6 Rear Panel Terminals...
Page 67: ...www eaton com Page 6 11 MP 4000 IB02602002E Figure 6 11 Alternatives for Discrete Input Wiring...
Page 72: ...Page 7 www eaton com IB02602002E MP 4000 This Page Intentionally Left Blank...
Page 83: ...www eaton com Page 9 MP 4000 IB02602002E Figure 9 1 Rotor Temperature Tracking...
Page 84: ...Page 9 www eaton com IB02602002E MP 4000 Figure 9 2 Motor Protection Curve...
Page 85: ...www eaton com Page 9 MP 4000 IB02602002E Figure 9 3 Underload Jam Protection Curve...
Page 88: ...Page 9 12 www eaton com IB02602002E MP 4000 Figure 9 6 Motor Start and Run Cycles...
Page 110: ...Page 13 10 www eaton com MP 4000 IB02602002E This Page Intentionally Left Blank...
Page 111: ...www eaton com MP 4000 IB02602002E This Page Intentionally Left Blank...