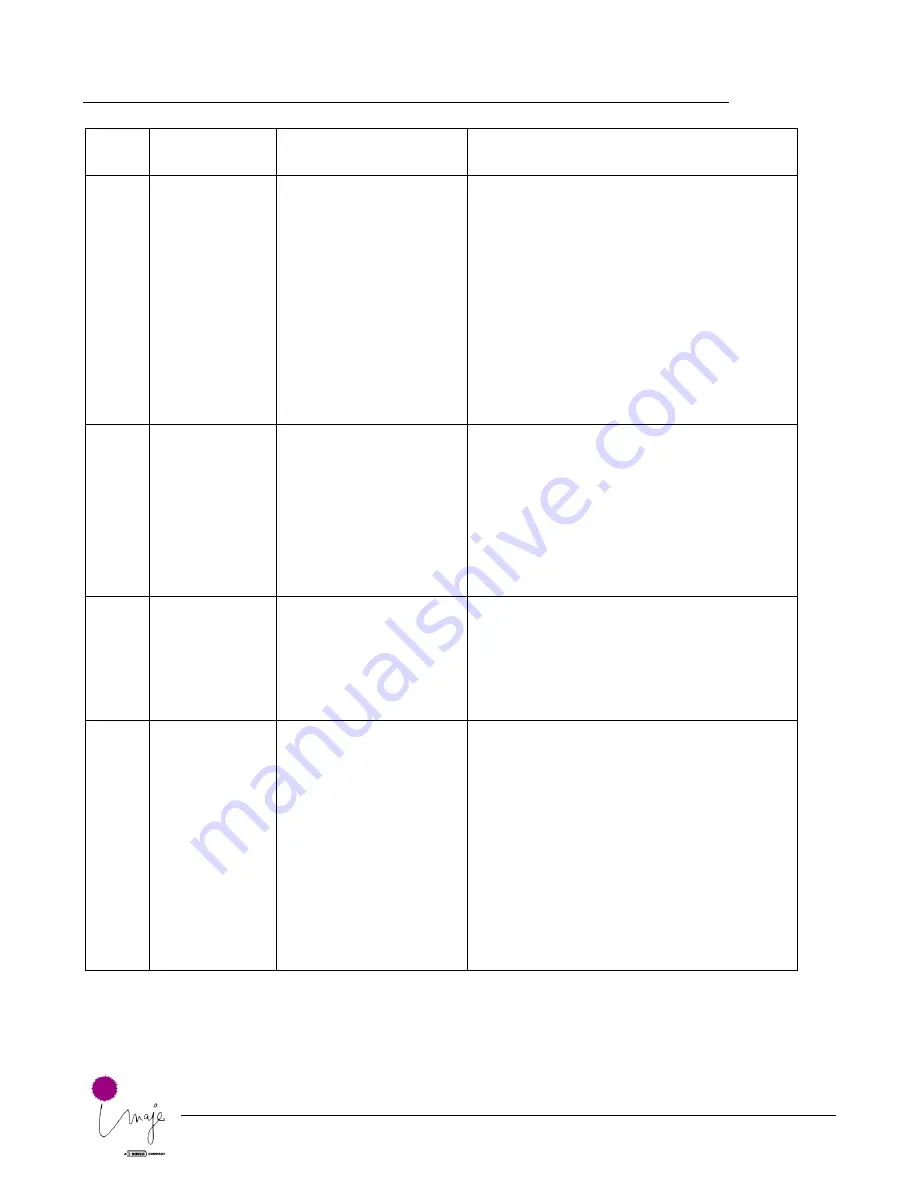
Troubleshooting
SECTION 06 Troubleshooting
12/54
A / D
No.
Description Context
Consequences
Check / Cause / Remedy / Solution
73
D
Ink transfer
timeout
The time needed at start-up
and during operation for the
condenser to drain to the
accumulator via SVs 4 and 3,
or for the accumulator to
drain to the buffer tank via
the conduit, is too long.
Consequences:
The IMM
stops and printing is
disabled.
1- Condenser vent.
Clean
2- Test solenoid valves 2, 3 and 4.
3- Test solenoid valves 11, A and B.
4- 200 µ leak along entire modulation
assembly.
Clean or replace the modulation assembly
5- Drain or pressure hose folded between IMM
and conduit.
Auto-calibration?
74
A
Air inflation
timeout
The time needed to blow air
into the accumulator during
start-up, draining or rinsing is
too long.
Consequences:
The printer
remains ready.
If the air
pocket is too small, the
pressure fluctuates and the
print quality varies and drops.
1- Test solenoid valves 3 and 4
2- Condenser vent.
3- Make sure the motor is running
4-
Make sure there is no ink in the air pump.
(Kapsto 6?)
75
A
Air pocket
management
incorrect
The difference in pressure in
the accumulator is too high
or too low during operation.
Consequences:
The print
quality is inconsistent and
drops.
1- Test solenoid valves 3 and 4
2- Condenser vent.
3- Drain the printer
4- IMM
76
A
Jet refreshment
timeout
At the end of jet start-up, the
pressure in the accumulator
must drop below a
determined value during
draining.
Consequences:
The printer
remains ready.
1- Test solenoid valves 11, A and B
2- 200 µ leak along entire modulation
assembly.
Clean or replace the modulation assembly
3- Drain or pressure hose folded between IMM
and conduit.
4- 14 µ screen between accumulator and
solenoid valve 11.
Rinse and drain the printer then check the 14 µ
screen.
5-
IMM