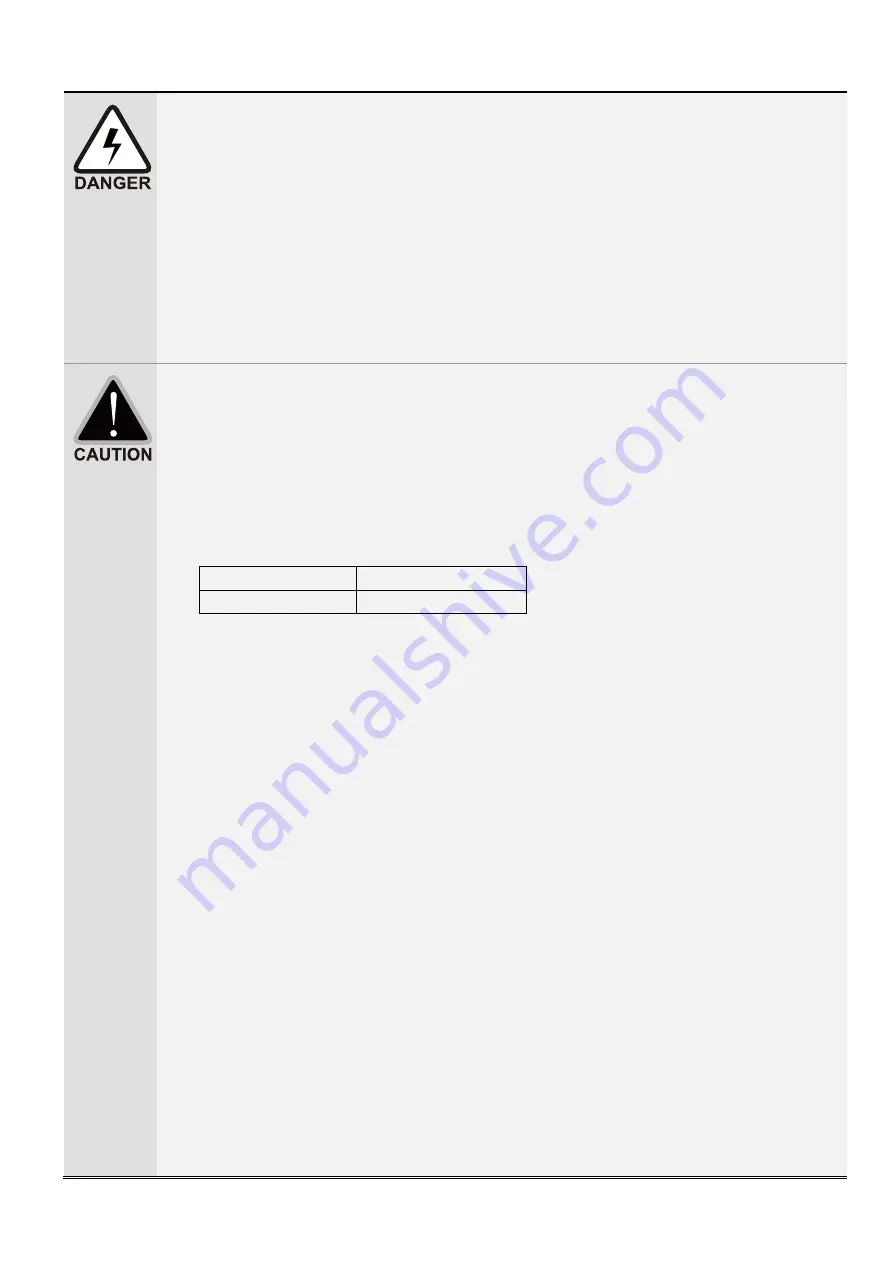
II
PLEASE READ PRIOR TO INSTALLATION FOR SAFETY.
Disconnect AC input power before connecting any wiring to the AC motor drive.
Even if the power has been turned off, a charge may still remain in the DC-link
capacitors with hazardous voltages before the POWER LED is OFF. Do NOT touch the
internal circuits and components.
There are highly sensitive MOS components on the printed circuit boards. These
components are especially sensitive to static electricity. Take anti-static measure before
touching these components or the circuit boards.
Never modify the internal components or wiring.
Ground the AC motor drive by using the ground terminal. The grounding method must
comply with the laws of the country where the AC motor drive is to be installed.
Do NOT install the AC motor drive in a location with high temperature, direct sunlight or
inflammable materials or gases.
Never connect the AC motor drive output terminals U/T1, V/T2 and W/T3 directly to the
AC mains circuit power supply.
After finishing the wiring of the AC motor drive, check if U/T1, V/T2, and W/T3 are
short-circuited to ground with a multimeter. Do NOT power the drive if short circuits occur.
Eliminate the short circuits before the drive is powered.
The rated voltage of power system to install motor drives is listed below. Ensure that the
installation voltage is in the correct range when installing a motor drive.
1. For 460V models, the range is between 323–528 V.
Refer to the table below for short circuit rating:
Model (Power)
Short circuit rating
230V / 460V
100 kA
Only qualified persons are allowed to install, wire and maintain the AC motor drives.
Even if the three-phase AC motor is stopped, a charge with hazardous voltages may still
remain in the main circuit terminals of the AC motor drive.
The performance of electrolytic capacitor will degrade if it is not charged for a long time. It
is recommended to charge the drive which is stored in no charge condition every 2 years
for 3–4 hours to restore the performance of electrolytic capacitor in the motor drive. Note:
When power up the motor drive, use adjustable AC power source (ex. AC
autotransformer) to charge the drive at 70%–80% of rated voltage for 30 minutes (do not
run the motor drive). Then charge the drive at 100% of rated voltage for an hour (do not
run the motor drive). By doing these, restore the performance of electrolytic capacitor
before starting to run the motor drive. Do NOT run the motor drive at 100% rated voltage
right away.
Pay attention to the following precautions when transporting and installing this package
(including wooden crate and wood stave)
1. If you need to deworm the wooden crate, do NOT use fumigation or you will damage
the drive. Any damage to the drive caused by using fumigation voids the warranty.
2. Use other methods, such as heat treatment or any other non-fumigation treatment, to
deworm the wood packaging material.
3. If you use heat treatment to deworm, leave the packaging materials in an environment
of over 56°C for a minimum of thirty minutes.
Connect the drive to a three-phase three-wire or three-phase four-wire Wye system to
comply with UL standards.
If the motor drive generates leakage current over AC 3.5 mA or over DC 10 mA on a
grounding conductor, compliance with local grounding regulations or IEC61800-5-1
standard is the minimum requirement for grounding.
Summary of Contents for CFP2000 Series
Page 3: ......
Page 12: ...Chapter 1 Introduction CFP2000 1 3 1 2 Model Name 1 3 Serial Number ...
Page 15: ...Chapter 1 Introduction CFP2000 1 6 Frame B RFI 1 RFI 1 RFI 1 RFI 2 RFI 2 RFI 2 Figure 1 5 ...
Page 37: ...Chapter 1 Introduction CFP2000 1 28 1 7 Digital Keypad KPC CC01 ...
Page 42: ...Chapter 3 Unpacking CFP2000 3 1 Chapter 3 Unpacking 3 1 Unpacking 3 2 The Lifting Hook ...
Page 54: ...Chapter 4 Wiring CFP2000 4 5 Figure 4 4 ...
Page 57: ...Chapter 4 Wiring CFP2000 4 8 4 4 Basic Waterproof Component Wiring Diagram Frame A Frame B ...
Page 58: ...Chapter 4 Wiring CFP2000 4 9 Frame C D0 ...
Page 75: ...Chapter 5 Main Circuit Terminals CFP2000 5 16 This page intentionally left blank ...
Page 120: ...Chapter 7 Optional Accessories CFP2000 7 35 Wall Mounting Embedded Mounting ...
Page 137: ...Chapter 7 Optional Accessories CFP2000 7 52 This page intentionally left blank ...
Page 173: ...Chapter 9 Specifications CFP2000 9 8 9 5 Efficiency Curve Figure 9 5 ...
Page 251: ...Chapter 11 Summary of Parameter Settings CFP2000 11 42 This page intentionally left blank ...
Page 304: ...Chapter 12 Description of Parameter Settings CFP2000 12 1 03 3 3 4 5 ...
Page 305: ...Chapter 12 Description of Parameter Settings CFP2000 12 1 03 4 6 7 8 ...
Page 306: ...Chapter 12 Description of Parameter Settings CFP2000 12 1 03 5 9 10 11 ...
Page 307: ...Chapter 12 Description of Parameter Settings CFP2000 12 1 03 6 12 13 14 ...
Page 308: ...Chapter 12 Description of Parameter Settings CFP2000 12 1 03 7 15 16 17 ...
Page 309: ...Chapter 12 Description of Parameter Settings CFP2000 12 1 03 8 18 19 20 ...
Page 310: ...Chapter 12 Description of Parameter Settings CFP2000 12 1 03 9 21 22 23 ...
Page 311: ...Chapter 12 Description of Parameter Settings CFP2000 12 1 03 10 24 25 26 ...
Page 312: ...Chapter 12 Description of Parameter Settings CFP2000 12 1 03 11 27 28 29 ...
Page 313: ...Chapter 12 Description of Parameter Settings CFP2000 12 1 03 12 30 31 32 ...
Page 314: ...Chapter 12 Description of Parameter Settings CFP2000 12 1 03 13 33 34 35 ...
Page 315: ...Chapter 12 Description of Parameter Settings CFP2000 12 1 03 14 36 37 38 ...
Page 326: ...Chapter 12 Description of Parameter Settings CFP2000 12 1 03 25 ...
Page 545: ...Chapter 14 Fault Codes and Descriptions CFP2000 14 50 This page intentionally left blank ...
Page 726: ...Chapter 16 PLC Function Applications CFP2000 16 153 ...
Page 728: ...Chapter 16 PLC Function Applications CFP2000 16 155 ...
Page 731: ...Chapter 16 PLC Function Applications CFP2000 16 158 This page intentionally left blank ...
Page 747: ...Chapter 17 Introduction to BACnet CFP2000 17 16 This page intentionally left blank ...