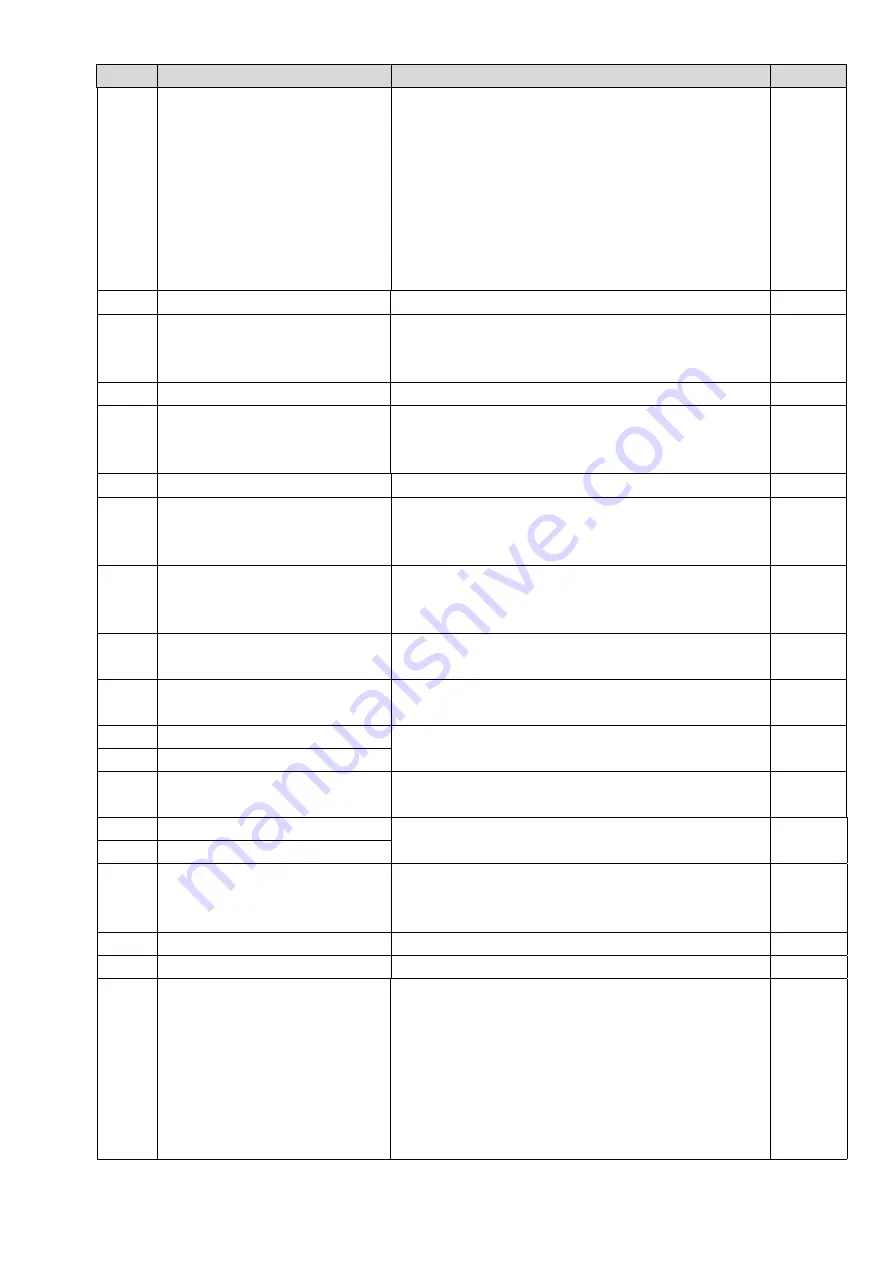
Chapter 11 Summary of Parameter Settings
CFP2000
11-15
Pr.
Parameter Name
Setting Range
Default
6: Power factor
7: Power
9: AVI1%
10: ACI%
11: AVI2%
20: CANopen analog output
21: RS-485 analog output
22: Communication card analog output
23: Constant voltage output
03-21 Analog output gain 1 (AFM1)
0.0–500.0%
100.0
03-22
Analog output 1 in REV direction
(AFM1)
0: Absolute value of output voltage
1: Reverse output 0 V; forward output 0–10 V
2: Reverse output 5–0 V; forward output 5–10 V
0
03-24 Analog output gain 2 (AFM2)
0.0–500.0%
100.0
03-25
Analog output 2 in REV direction
(AFM2)
0: Absolute value of output voltage
1: Reverse output 0 V; forward output 0–10 V
2: Reverse output 5–0 V; forward output 5–10 V
0
03-27 AFM2 output bias
-100.00–100.00%
0.00
03-28 AVI1 terminal input selection
0: 0–10 V
1: 0–20 mA
2: 4–20 mA
0
03-29 ACI terminal input selection
0: 4–20 mA
1: 0–10 V
2: 0–20 mA
0
03-30
PLC analog output terminal
status
Monitor the status of PLC analog output terminals
Read
only
03-31 AFM2 output selection
0: 0–20 mA output
1: 4–20 mA output
0
03-32 AFM1 DC output setting level
0.00–100.00%
0.00
03-33 AFM2 DC output setting level
03-34 AFM1 output selection
0: 0–20 mA output
1: 4–20 mA output
0
03-35 AFM1 filter output time
0.00–20.00 sec.
0.01
03-36 AFM2 filter output time
03-44
Multi-function MO output by AI
level source
0: AVI1
1: ACI
2: AVI2
0
03-45 AI upper level
-100.00–100.00%
50.00
03-46 AI lower level
-100.00–100.00%
10.00
03-50 Analog input curve selection
0: Regular curve
1: Three-point curve of AVI1
2: Three-point curve of ACI
3: Three-point curve of AVI1 & ACI
4: Three-point curve of AVI2
5: Three-point curve of AVI1 & AVI2
6: Three-point curve of ACI & AVI2
7: Three-point curve of AVI1 & ACI & AVI2
7
Summary of Contents for CFP2000 Series
Page 3: ......
Page 12: ...Chapter 1 Introduction CFP2000 1 3 1 2 Model Name 1 3 Serial Number ...
Page 15: ...Chapter 1 Introduction CFP2000 1 6 Frame B RFI 1 RFI 1 RFI 1 RFI 2 RFI 2 RFI 2 Figure 1 5 ...
Page 37: ...Chapter 1 Introduction CFP2000 1 28 1 7 Digital Keypad KPC CC01 ...
Page 42: ...Chapter 3 Unpacking CFP2000 3 1 Chapter 3 Unpacking 3 1 Unpacking 3 2 The Lifting Hook ...
Page 54: ...Chapter 4 Wiring CFP2000 4 5 Figure 4 4 ...
Page 57: ...Chapter 4 Wiring CFP2000 4 8 4 4 Basic Waterproof Component Wiring Diagram Frame A Frame B ...
Page 58: ...Chapter 4 Wiring CFP2000 4 9 Frame C D0 ...
Page 75: ...Chapter 5 Main Circuit Terminals CFP2000 5 16 This page intentionally left blank ...
Page 120: ...Chapter 7 Optional Accessories CFP2000 7 35 Wall Mounting Embedded Mounting ...
Page 137: ...Chapter 7 Optional Accessories CFP2000 7 52 This page intentionally left blank ...
Page 173: ...Chapter 9 Specifications CFP2000 9 8 9 5 Efficiency Curve Figure 9 5 ...
Page 251: ...Chapter 11 Summary of Parameter Settings CFP2000 11 42 This page intentionally left blank ...
Page 304: ...Chapter 12 Description of Parameter Settings CFP2000 12 1 03 3 3 4 5 ...
Page 305: ...Chapter 12 Description of Parameter Settings CFP2000 12 1 03 4 6 7 8 ...
Page 306: ...Chapter 12 Description of Parameter Settings CFP2000 12 1 03 5 9 10 11 ...
Page 307: ...Chapter 12 Description of Parameter Settings CFP2000 12 1 03 6 12 13 14 ...
Page 308: ...Chapter 12 Description of Parameter Settings CFP2000 12 1 03 7 15 16 17 ...
Page 309: ...Chapter 12 Description of Parameter Settings CFP2000 12 1 03 8 18 19 20 ...
Page 310: ...Chapter 12 Description of Parameter Settings CFP2000 12 1 03 9 21 22 23 ...
Page 311: ...Chapter 12 Description of Parameter Settings CFP2000 12 1 03 10 24 25 26 ...
Page 312: ...Chapter 12 Description of Parameter Settings CFP2000 12 1 03 11 27 28 29 ...
Page 313: ...Chapter 12 Description of Parameter Settings CFP2000 12 1 03 12 30 31 32 ...
Page 314: ...Chapter 12 Description of Parameter Settings CFP2000 12 1 03 13 33 34 35 ...
Page 315: ...Chapter 12 Description of Parameter Settings CFP2000 12 1 03 14 36 37 38 ...
Page 326: ...Chapter 12 Description of Parameter Settings CFP2000 12 1 03 25 ...
Page 545: ...Chapter 14 Fault Codes and Descriptions CFP2000 14 50 This page intentionally left blank ...
Page 726: ...Chapter 16 PLC Function Applications CFP2000 16 153 ...
Page 728: ...Chapter 16 PLC Function Applications CFP2000 16 155 ...
Page 731: ...Chapter 16 PLC Function Applications CFP2000 16 158 This page intentionally left blank ...
Page 747: ...Chapter 17 Introduction to BACnet CFP2000 17 16 This page intentionally left blank ...