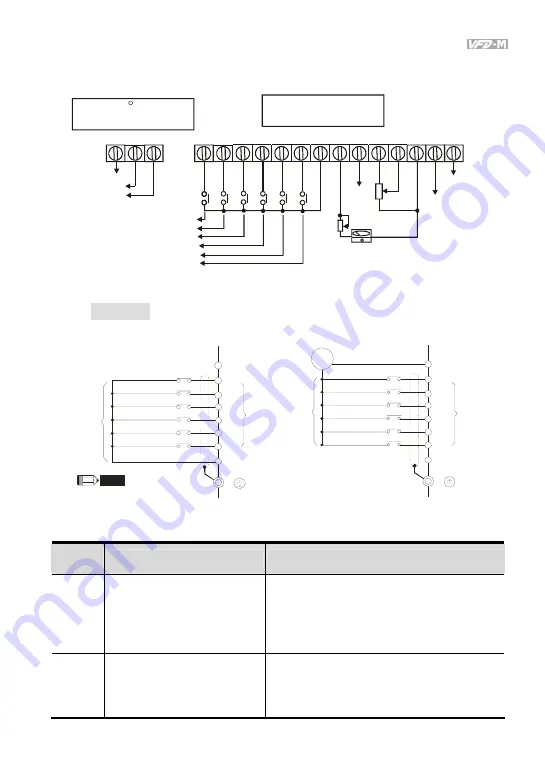
Chapter 2 Installation and Wiring
|
Revision May 2008, ME14, SW V3.04
2-9
2.4 Control Terminal Wiring (Factory Settings)
M0 M1 M2 M3 M4 M5 GND AFM
AVI
+10V
MCM
MO1
RA RB RC
Relay contactor
Output
Factory Setting
Bias
Potentiometer
Full scale voltmeter
0 to 10 VDC
Factory setting:
fault indication
Photo coupler
output
Forward/Stop
Reverse/Stop
Reset
Multi-step speed 1
Multi-step speed 2
Multi-step speed 3
ACI
GND
4~20mA
Wire Type: 75 C, Copper Only
Torque: 4kgf-cm (3.5 in-lbf)
Wire Gauge: 24-12 AWG
Wire Type: Copper Only
Torque: 2kgf-cm (1.73 in-lbf)
Wire Gauge: 22-16 AWG
NPN mo de wi thout ext ernal p owe r
M0
M1
M2
M3
M5
M4
E
GND
+24V
2 4
Vdc
-
+
NPN Mode
NOTE
M0
M1
M2
M3
M5
M4
E
GND
+2 4V
NPN mode wi th exte rnal pow er
Fa
c
to
ry
S
e
tt
ing
Fo rwa rd/St op
Reve rse /Sto p
Rese t
Mu lti -ste p 1
Mu lti -ste p 2
Mu lti -ste p 3
Common Si gnal
M
u
lt
i-
fu
n
c
ti
o
n
In
p
u
t
Te
rm
in
a
ls
Don' t a pply the mains voltage
directly to above t erminals.
Fa
c
to
ry
S
e
tt
ing
M
u
lt
i-
fu
n
c
ti
o
n
In
p
u
t
Te
rm
in
a
ls
Fo rwa rd/St op
Reve rse /Sto p
Rese t
Mu lti -ste p 1
Mu lti -ste p 2
Mu lti -ste p 3
Terminal symbols and functions
Terminal
Symbol
Terminal Function
Factory Settings (NPN mode)
RA
Multi-Function Relay Output
(N.O.) a
RA-RC
Resistive Load
5A(N.O.)/3A(N.C.) 277Vac;
5A(N.O.)/3A(N.C.) 30Vdc
Refer to P45 for programming.
RB
Multi-Function Relay Output
(N.C.) b
RB-RC
Resistive Load
5A(N.O.)/3A(N.C.) 277Vac;
5A(N.O.)/3A(N.C.) 30Vdc
Summary of Contents for VFD-M Series
Page 1: ......
Page 2: ......
Page 3: ......
Page 12: ...Chapter 1 Introduction Revision May 2008 ME14 SW V3 04 1 3 1 1 4 External Parts and Labels ...
Page 17: ...Chapter 1 Introduction 1 8 Revision May 2008 ME14 SW V3 04 This page intentionally left blank ...
Page 21: ...Chapter 2 Installation and Wiring 2 4 Revision May 2008 ME14 SW V3 04 Good Not allowed ...
Page 121: ...Chapter 4 Parameters 4 86 Revision May 2008 ME14 SW V3 04 This page intentionally left blank ...
Page 149: ...Appendix B Accessories B 4 Revision May 2008 ME14 SW V3 04 ...