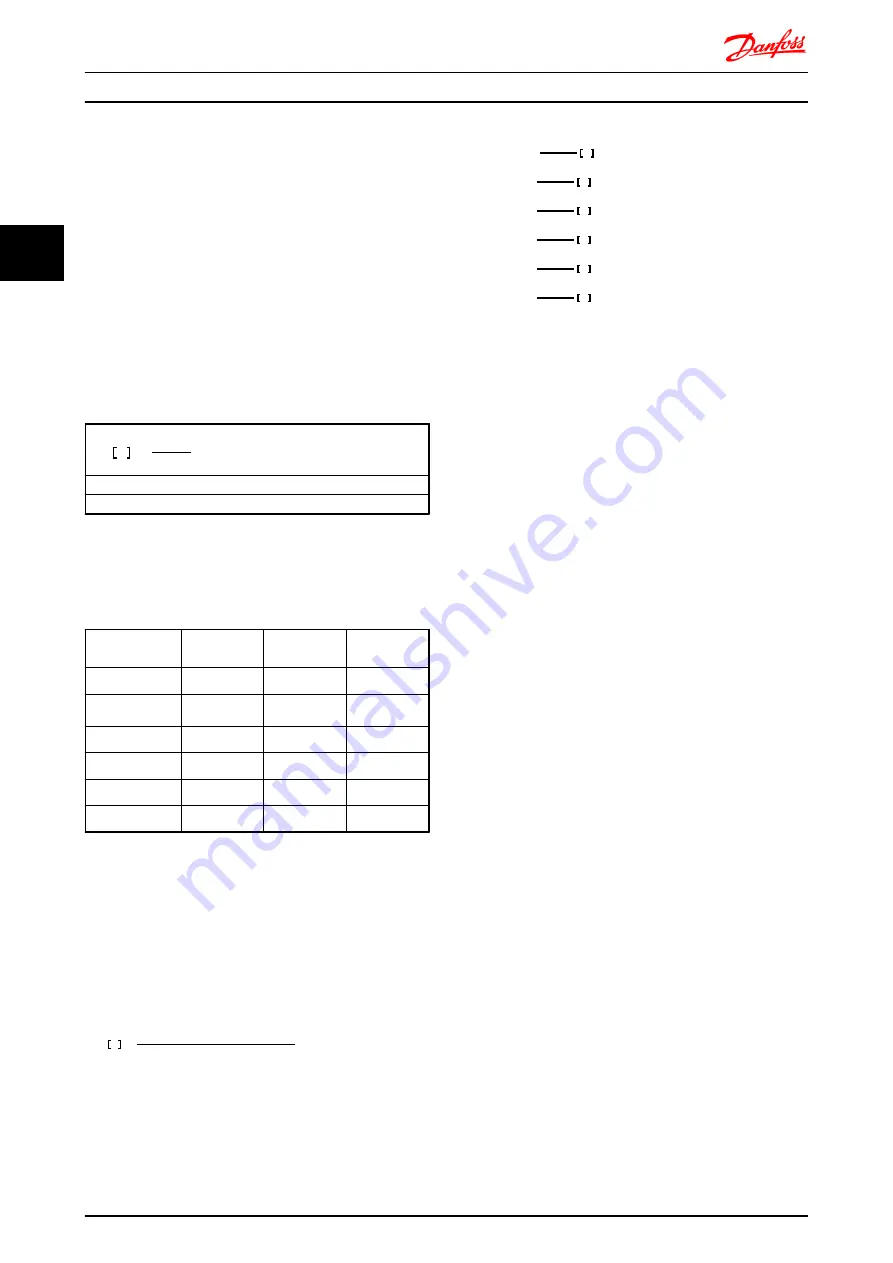
Danfoss offers brake resistors with duty cycle of 5%, 10%
and 40%. If a 10% duty cycle is applied, the brake resistors
are able to absorb brake power for 10% of the cycle time.
The remaining 90% of the cycle time will be used on
dissipating excess heat.
Make sure the resistor is designed to handle the required
braking time.
The max. permissible load on the brake resistor is stated as
a peak power at a given intermittent duty cycle and can
be calculated as:
The brake resistance is calculated as shown:
Rbr Ω =
Udc
2
Ppeak
where
P
peak
= P
motor
x M
br
[%] x η
motor
x η
VLT
[W]
As can be seen, the brake resistance depends on the
intermediate circuit voltage (U
dc
).
The FC 301 and FC 302 brake function is settled in 4 areas
of mains.
Size
Brake active Warning
before cut
out
Cut out (trip)
FC301/302 3 x
200-240 V
390V (UDC)
405V
410V
FC301 3 x 380-480
V
778V
810V
820V
FC302 3 x 380-500
V*
810V/ 795V
840V/ 828V
850V/ 855V
FC302 3 x 525-600
V
943V
965V
975V
FC302 3 x 525-690
V
1084V
1109V
1130V
* Power size
dependent
Check that the brake resistor can cope with a voltage of
410V, 820V, 850V, 975V or 1130V - unless Danfoss brake
resistors are used.
Danfoss recommends the brake resistance R
rec
, i.e. one that
guarantees that the frequency converter is able to brake at
the highest braking torque (M
br(%)
) of 160%. The formula
can be written as:
Rrec Ω =
Udc
2 x 100
Pmotor x Mbr (%) xηVLT x ηmotor
η
motor
is typically at 0.90
η
VLT
is typically at 0.98
For 200V, 480V, 500V and 600V frequency converters, R
rec
at 160% braking torque is written as:
200
V : Rrec =
107780
Pmotor
Ω
480
V : Rrec =
375300
Pmotor
Ω 1)
480
V : Rrec =
428914
Pmotor
Ω 2)
500
V : Rrec =
464923
Pmotor
Ω
600
V : Rrec =
630137
Pmotor
Ω
690
V : Rrec =
832664
Pmotor
Ω
1) For frequency converters ≤ 7.5 kW shaft output
2) For frequency converters 11 - 75 kW shaft output
NOTE
The resistor brake circuit resistance selected should not be
higher than that recommended by Danfoss. If a brake
resistor with a higher ohmic value is selected, the 160%
braking torque may not be achieved because there is a risk
that the frequency converter cuts out for safety reasons.
NOTE
If a short circuit in the brake transistor occurs, power
dissipation in the brake resistor is only prevented by using
a mains switch or contactor to disconnect the mains for
the frequency converter. (The contactor can be controlled
by the frequency converter).
NOTE
Do not touch the brake resistor as it can get very hot
while/after braking. The brake resistor must be placed in a
secure environment to avoid fire risk
D-F size frequency converters contain more than one brake
chopper. Consequently, use one brake resistor per brake
chopper for those frame sizes.
3.8.4 Control with Brake Function
The brake is protected against short-circuiting of the brake
resistor, and the brake transistor is monitored to ensure
that short-circuiting of the transistor is detected. A relay/
digital output can be used for protecting the brake resistor
against overloading in connection with a fault in the
frequency converter.
In addition, the brake makes it possible to read out the
momentary power and the mean power for the latest 120
seconds. The brake can also monitor the power energizing
and make sure it does not exceed a limit selected in
2-12 Brake Power Limit (kW)
. In
2-13 Brake Power Monitoring
,
select the function to carry out when the power
transmitted to the brake resistor exceeds the limit set in
2-12 Brake Power Limit (kW)
.
Introduction to FC 300
FC 300 Design Guide
44
MG.33.BD.02 - VLT
®
is a registered Danfoss trademark
3
3