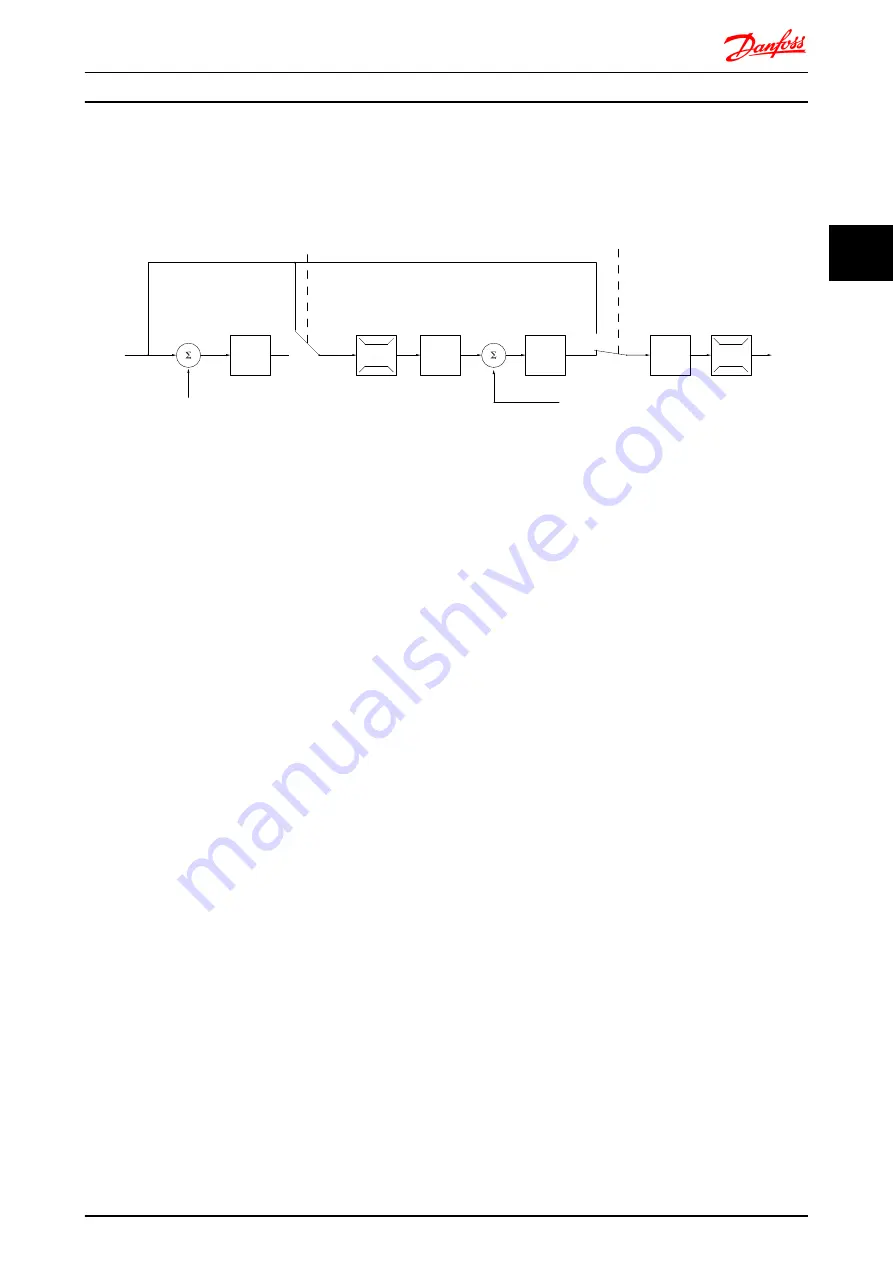
3.2.6 Control Structure in Flux with Motor Feedback
Control structure in Flux with motor feedback configuration (only available in FC 302):
130BA054.11
P 3-**
P 7-0*
P 7-2*
+
_
+
_
P 7-20 Process feedback
1 source
P 7-22 Process feedback
2 source
P 4-11 Motor speed
low limit (RPM)
P 4-12 Motor speed
low limit (Hz)
P 4-13 Motor speed
high limit (RPM)
P 4-14 Motor speed
high limit (Hz)
High
Low
Ref.
Process
PID
Speed
PID
Ramp
P 7-00
PID source
Motor
controller
-f max.
+f max.
P 4-19
Max. output
freq.
P 1-00
Config. mode
P 1-00
Config. mode
Torque
In the shown configuration,
1-01 Motor Control Principle
is set to “Flux w motor feedb [3]” and
1-00 Configuration Mode
is set
to “Speed closed loop [1]”.
The motor control in this configuration relies on a feedback signal from an encoder mounted directly on the motor (set in
1-02 Flux Motor Feedback Source
).
Select “Speed closed loop [1]” in
1-00 Configuration Mode
to use the resulting reference as an input for the Speed PID
control. The Speed PID control parameters are located in parameter group 7-0*.
Select “Torque [2]” in
1-00 Configuration Mode
to use the resulting reference directly as a torque reference. Torque control
can only be selected in the
Flux with motor feedback
(
1-01 Motor Control Principle
) configuration. When this mode has been
selected, the reference will use the Nm unit. It requires no torque feedback, since the actual torque is calculated on the
basis of the current measurement of the frequency converter.
Select “Process [3]” in
1-00 Configuration Mode
to use the process PID control for closed loop control of e.g. speed or a
process variable in the controlled application.
Introduction to FC 300
FC 300 Design Guide
MG.33.BD.02 - VLT
®
is a registered Danfoss trademark
21
3
3