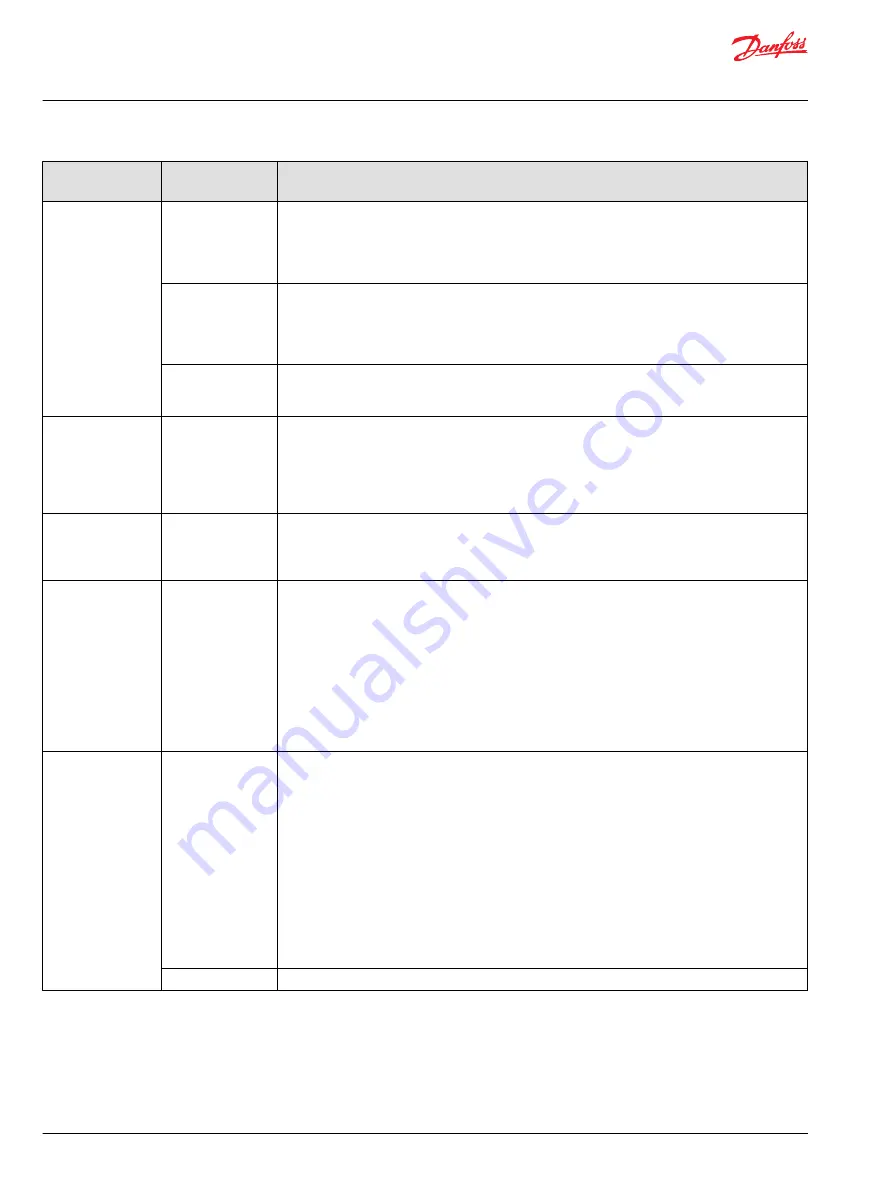
Symptom
PVED-CL
Operation Status
Cause/Solution
No actuation
(with high or low
priority steering
device or external set-
point controllers)
Operational
1. No or insufficient pressure is supplied to the valve.
2. No steering device is mapped.
3. Parameter Qm set to ~0
4. No or incorrect auto-steering message from external set-point controller
5. Spool sticks in neutral position
Fault
1. No or missing signal from steering signals at the AD1, AD2 or CAN interface.
2. Missing sensor signal (see
2. PVED-CL expects a different baud rate at network.
3. Insufficient electrical power supply to the PVED-CL.
4. PVED-CL has suffered a internal critical error.
No status available
1. CAN bus not operational. Check connection.
2. No electric power supply
3. PVED-CL is damaged. (see
Opposite actuation
Operational
1. Hoses between valve and steering actuator are swapped.
2. Steering wheel angle sensor (and possibly OSP) is incorrectly installed.
3. Steering device input transfer function is mirrored.
4. The InvertInputSignal program parameter is set incorrectly (see page 127).
5. The ValveType parameter is set incorrectly (see page 124).
6. Steered wheel sensor outputs a constant valid voltage/value (closed loop).
Slow actuation
responds (delays)
Operational
1. Air is trapped in the steering actuator or hoses.
2. Oil has high viscosity. Make sure to apply to the technical requirements listed in
page 22.
3. The requested pressure is supplied with some delay (Pump).
Self-steering
Operational
1. The parameters Xspr_0 and Xspl_0 in the PVED-CL are not correctly set relative to the mechanical
dead-band location in the spool-opening characteristic. Read more information in
on
page 23.
2. The actual neutral position and calibrated neutral position (steering devices such as joysticks, etc.) do
not match and causes a small output flow when the device is activated.
3. PVED-CL neutral spool position calibration is incorrect and needs re-adjusting (mechanical valve
defect).
4. Auto-steering is not disabled when a higher priority device is selected. Check if higher priority devices
are mapped.
5. Steering device dead-band is too small – noise may activate the device and cause the spool to jump
between left and right valve dead-band.
Actuation with low
gain
Operational
1. The amplification parameters (Sts) are set at a too low value (for steering devices) and too high for the
steering wheel sensor. Read more information on Select a fixed sensitivity.
2. The gain linearity index (Lx) is set at a high value.
3. Parameter “Vcap” is set greater than the true flow capacity of the valve.
4. Steering wheel angle sensor is installed upside down (causing a conflict with the OSP pilot signals).
5. The soft-stop functionality limits the flow because the steered wheel angle sensor input is not
correctly calibrated, mirrored or constant.
6. (Soft-stop). The steered wheels are being driven beyond the logical end-stop values (maximum output
flow in determined by the Off parameter.
7. The maximum flow parameter (Qm) is set too low for the particular program.
8. Then SASA sensor is not mapped as present – only the OSP is driving the valve.
9. The full range of a steering device relative to its calibration range is not being fully utilized.
10. If velocity dependent steering sensitivity is applied, the Sts settings may be incorrect or the vehicle
speed sensor outputs wrong data.
Fault
The hydraulic back-up system is active. The steering sensitivity is determined by the OSP.
J1939 Diagnostic Interface
There are two ways of accessing fault codes in the PVED-CL as outlined in a figure below.
•
Via J1939 diagnostic interface (SAE J1939-73)
•
Via J1939 proprietary protocol (PDU1 format)
Operation Manual
PVED-CL Controller for Electro-Hydraulic Steering, Version 1.38
Diagnostic & Troubleshooting
102 |
©
Danfoss | May 2016
11025583 | AQ00000216en-US0302