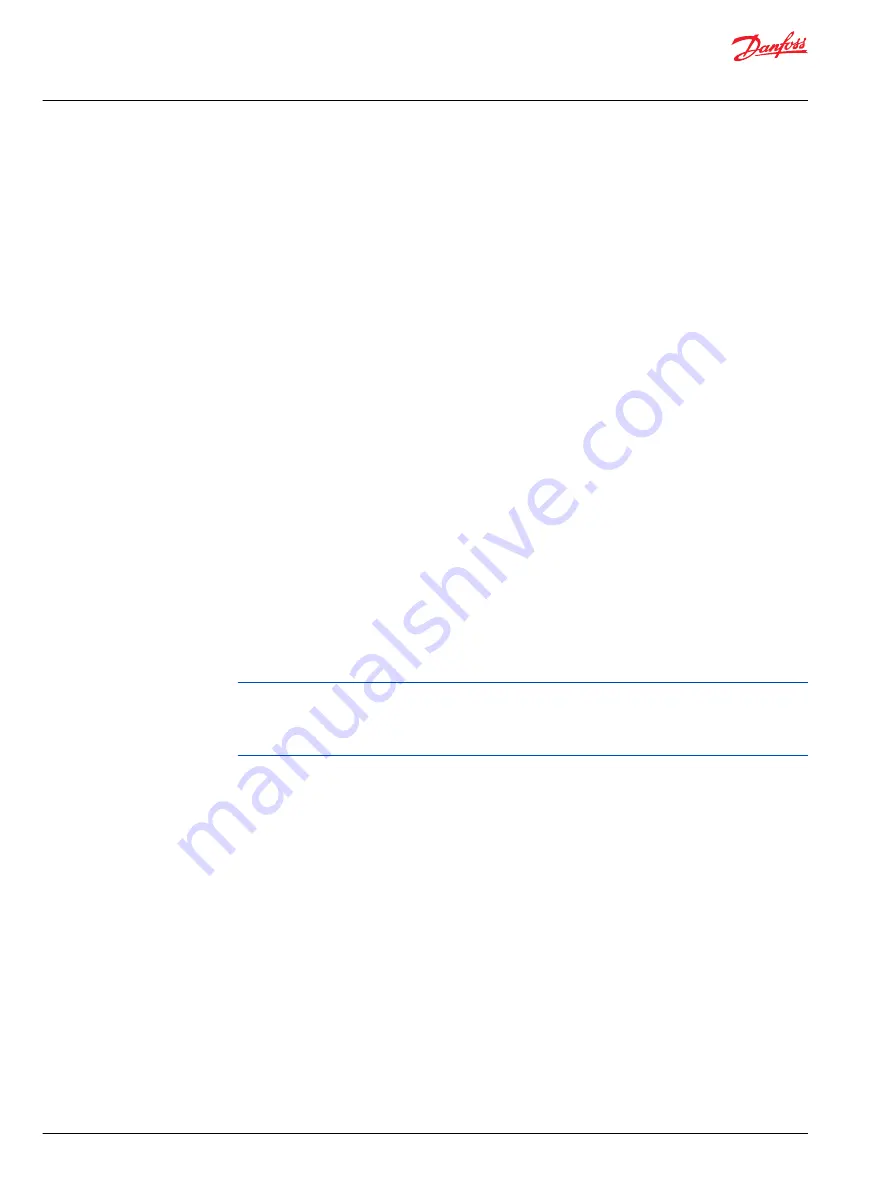
Valve calibration methods
The PVED-CL can be calibrated to a valve in three possible ways:
•
Use conservative software dead-band values
•
Manual software dead-band calibration
•
Valve auto-calibration
Method 1: Conservative software dead-band values
This method does not require any specific sensor or measurement equipment. The principle in this
method is to set the open-loop and closed-loop software dead-bands sufficiently low and high,
respectively, and let these dead-bands be valid for an entire series of valve units.
1. The open-loop dead-bands are determined based on the minimum hydraulic dead-band tolerances
for a particular valve.
2. The closed loop dead-bands are determined by setting the ClosedLoopXspOffset parameter, based
on knowledge to the maximum hydraulic dead-band tolerances for a particular valve and adding
some margin, to always have a correcting flow available.
Example: Determine the general software dead-bands for a series of PVED-CL / EH valve with a
dynamic spool:
•
All dead-band values are in scaled spool position set-points, Xsp.
•
From the
on page 24 we get the minimum hydraulic dead-band to 77 and a
maximum hydraulic dead-band equal to 108.
•
Xspl_0 and Xspr_0 are set to ±70 to have a small overlap (±7) to the minimum hydraulic dead-band.
•
To ensure enough flow for e.g. auto-steering, ClosedLoopXspOffset is set equal to the maximum
hydraulic dead-band plus a little margin to guarantee a flow.
•
In this example a margin equal 25 is chosen which result in a ClosedLoopXspOffset equal to (108 +
25) – 70 = 63.
•
Xspl_1000 and Xspr_1000 are set to 430 to operate the EH valve in its full range.
Using conservative dead-band values will create steering performance which will vary slightly from
valve to valve. E.g. for variable steering ratio applications, the dead-band and steering ratio will vary
slightly. Similarly in auto-steering mode, the flow for correcting the steered wheels may vary from
smooth corrections to more jerky corrections.
Method 2: Manual software dead-band calibration
The principle in this method is to match the PVED-CL software dead-bands to the hydraulic dead-band
for the particular valve it is controlling. This kind of calibration will reduce the impact of mechanical
tolerances and thus reduce the valve-to-valve performance differences.
This method does not require any specific sensor but requires a service tool to be connected to the PVED-
CL. The operator performing the calibration must be able to observe a movement of the steering actuator
or steered wheels during the procedure and read out main spool set-points.
For production, calibration and field service purposes, the PVED_CL allows direct control of the main
spool. On reception of a SetSpoolPosition message (see
PVED-CL Communication Protocol
, 11079551),
the main spool can be commanded to a specific set-point position. Manual software dead-band
calibration can only be performed when the PVED-CL is in calibration mode. See section
EnterCalibrationMode in
PVED-CL Communication Protocol
, 11079551 on how to run the PVED-CL in
calibration mode.
The procedure requires a service tool to set the PVED-CL in calibration mode and to control the main
spool set-point. The procedure is:
1. Find the hydraulic dead-band by gradually increasing the main spool set-point in small steps (5 – 10),
until steered wheel movement is observed. Must be done for both left and right direction.
2. Determine Xspl_0 and Xspr_0 by subtracting 10-25 from the detected hydraulic dead-bands. This
shall ensure that the open-loop dead-bands are inside the hydraulic dead-band with an over-lap.
Operation Manual
PVED-CL Controller for Electro-Hydraulic Steering, Version 1.38
Installation
26 |
©
Danfoss | May 2016
11025583 | AQ00000216en-US0302