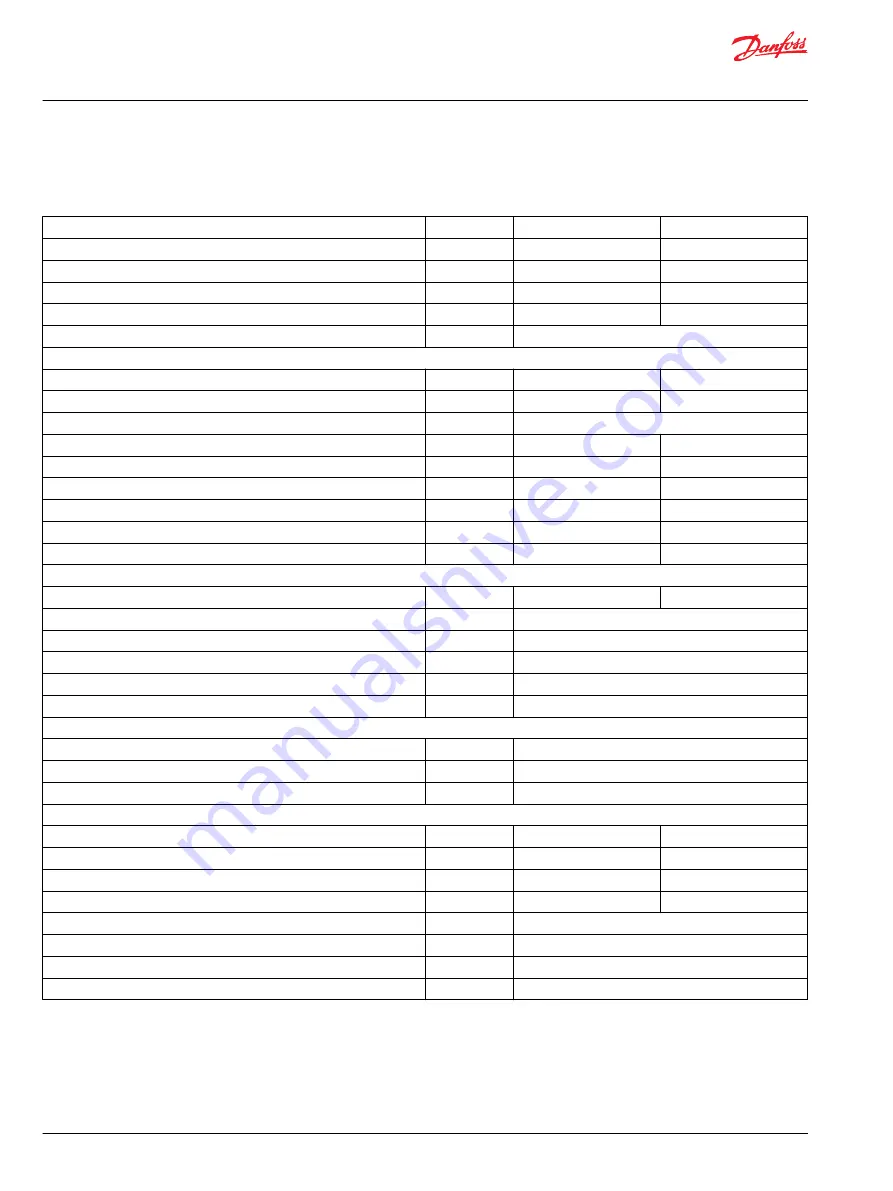
Technical Data
Technical Data
Electrical
Unit
Min
Max
Required supply voltage
V DC
11
32
Required current with magnetic valves enabled
A
1
0.3
Required current with magnetic valves disabled
A
0.1
0.03
Power consumption
W
7
10
Power consumption (magnetic valves off)
W
max 0.3
Hydraulic
Viscosity
Cst
21
460
Contamination level (ISO 4406)
-
21/19/16
Max EMC
V/m
max 100
Oil temperature
ºC
-30
90
Recommended oil temperature
ºC
30
60
Ambient Temperature
ºC
-30
60
Pilot flow with magnetic valves disabled
l/min
0.2
0.4
Pilot flow with magnetic valves enabled
l/min
0.2
1.1
Pilot pressure to PVED
bar
10
15
Signals
Stabilized voltage supply
V DC
4.80
5.20
Max current taken from stabilized voltage supply
mA
100
Digital conversion of signals at AD1 & 2
V DC
0 to 5 VDC into 0 – 1023 (10 bit)
Available baud rates to CAN
Kilo bit/s
125, 250, 500
AD1 & 2 input impedance
Approximately 1MOhm
Max analogue signal source impedance
<100 kOhm
Protection
Grade of enclosure (IEC 529) Connector
IP
66
Over voltage at 36 V DC
minutes
5
Reverse polarity
minutes
Infinite for all faults except: see
on page 23.
Performance
Spool position Hysteresis in % of full spool stroke
-
0.5
1
Inherent Ramp-up time from neutral to full open
ms
50
210
Inherent Ramp-down time from full open to neutral
ms
40
150
Boot time EHPS software
ms
1200
1500
Recognition time of incorrect voltage signals
ms
50
Recognition time of incorrect supply voltage
ms
200
Recognition time of incorrect CAN signals
ms
200
Recognition time of incorrect internal operations
ms
50 (watchdog)
Operation Manual
PVED-CL Controller for Electro-Hydraulic Steering, Version 1.38
Technical Specification
22 |
©
Danfoss | May 2016
11025583 | AQ00000216en-US0302