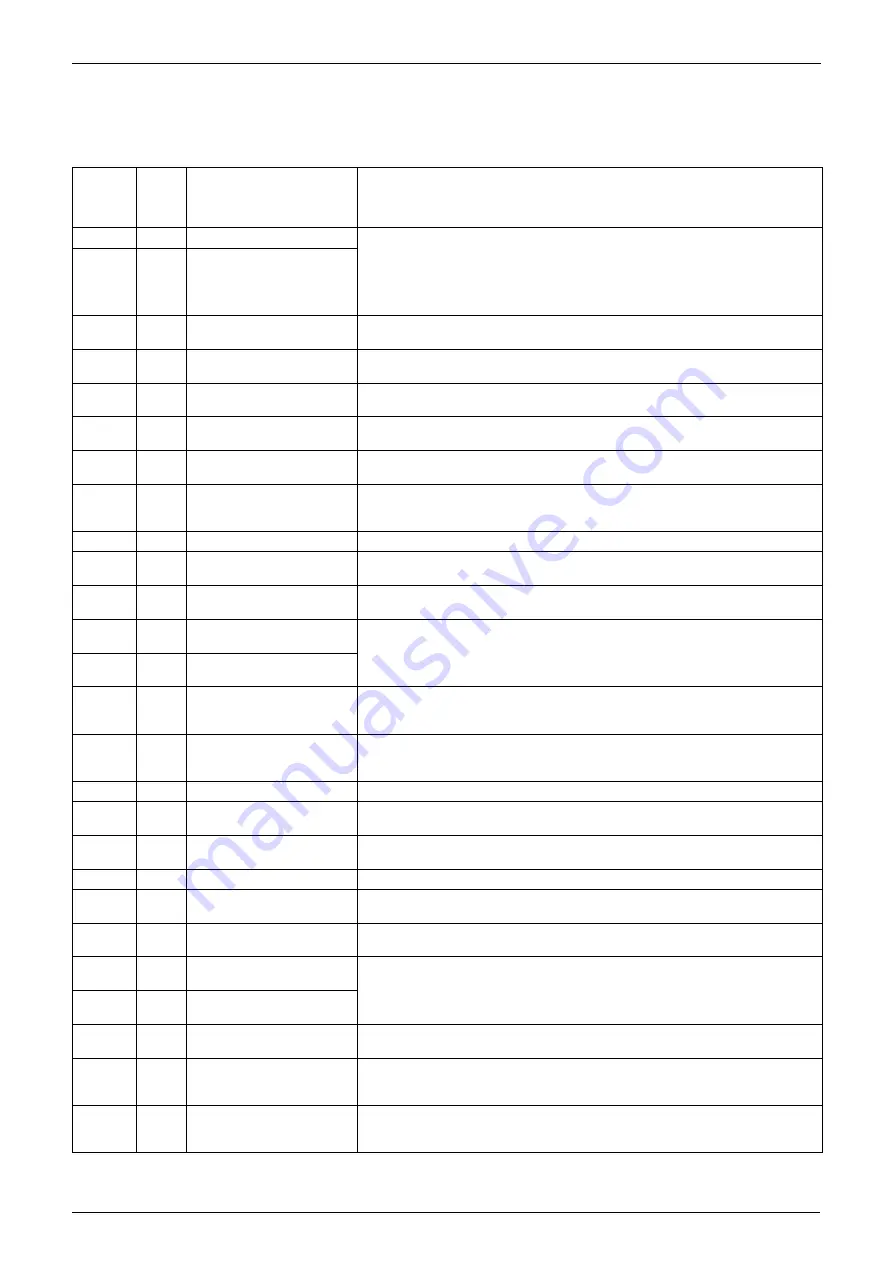
Refrigerant Circuit
Si39-502A
44
Refirgerant Circuit
1.
Refrigerant Circuit
1.1
RXYQ8M, 10M
No. in
refrigerant
system
diagram
Symbol
Name
Major Function
A
M1C
Inverter compressor (INV)
Inverter compressor is operated on frequencies between 52 Hz and 210 Hz
by using the inverter, while Standard compressor is operated with
commercial power supply only. The number of operating steps is as follows
when Inverter compressor is operated in combination with Standard
compressor.
RXYQ8, 10M: 37 steps
B
M2C
Standard compressor 1
(STD1)
D
M1F
Inverter fan
Since the system is of air heat exchanging type, the fan is operated at 9-step
rotation speed by using the inverter.
E
Y1E
Electronic expansion valve
(Main: EV1)
While in heating operation, PI control is applied to keep the outlet
superheated degree of air heat exchanger constant.
F
Y2E
Electronic expansion valve
(Subcool: EV2)
PI control is applied to keep the outlet superheated degree of subcooling
heat exchanger constant.
G
Y1S
Solenoid valve (Hot gas:
SVP)
Used to prevent the low pressure from transient falling.
J
Y2S
Solenoid valve (Receiver
gas discharging: SVG)
Used to collect refrigerant to receiver.
L
Y3S
Solenoid valve (Non-
operating unit liquid pipe
closing: SVSL)
Used to prevent the accumulation of refrigerant in non-operating outdoor
units in the case of multi-outdoor unit system.
M
Y4S
4-way valve
Used to switch the operation mode between cooling and heating.
N
S1NP
H
High pressure sensor
Used to detect high pressure.
O
S1NP
L
Low pressure sensor
Used to detect low pressure.
P
S1PH
HP pressure switch (For
INV compressor)
In order to prevent the increase of high pressure when a malfunction occurs,
this switch is activated at high pressure of 4.0 MPa or more to stop the
compressor operation.
Q
S2PH
HP pressure switch (For
STD compressor 1)
S
—
Fusible plug
In order to prevent the increase of pressure when abnormal heating is
caused by fire or others, the fusible part of the plug is molten at a
temperature of 70 to 75°C to release the pressure into the atmosphere.
U
—
Pressure regulating valve
2 (Liquid pipe to receiver)
This valve opens at a pressure of 2 to 2.7 MPa for prevention of pressure
increase, thus resulting in no damage of functional parts due to the increase
of pressure in transportation or storage.
V
—
Piping heat exchanger
Used to heat the gas refrigerant from the liquid receiver.
W
—
Capillary tube
Used to return the refrigerating oil separated through the oil separator to the
INV compressor.
X
—
Capillary tube
Used to return the refrigerating oil separated through the oil separator to the
STD1 compressor.
Y
—
Capillary tube
Used to add the refrigerant flow capacity to Y1E.
1
R1T
Thermistor (Outdoor air:
Ta)
Used to detect outdoor temperature, correct discharge pipe temperature, and
others.
2
R2T
Thermistor (Suction pipe:
Ts)
Used to detect suction pipe temperature, keep the suction superheated
degree constant in heating operation, and others.
3
R31T
Thermistor (INV discharge
pipe: Tdi)
Used to detect discharge pipe temperature, make the temperature protection
control of compressor, and others.
4
R32T
Thermistor (STD1
discharge pipe: Tds1)
6
R4T
Thermistor (Heat
exchanger deicer: Tb)
Used to detect liquid pipe temperature of air heat exchanger, determine
defrosting operation, and others.
7
R5T
Thermistor (Subcooling
heat exchanger gas pipe:
Tsh)
Used to detect gas pipe temperature on the evaporation side of subcooling
heat exchanger, keep the superheated degree at the outlet of subcooling
heat exchanger constant, and others.
8
R6T
Thermistor (Receiver
outlet liquid pipe: Tl)
Used to detect receiver outlet liquid pipe temperature, prevent the drift
between outdoor units while in heating operation in the case of multiple-
outdoor-unit system, and others.
Summary of Contents for VRV II RXYQ8MY1K
Page 53: ...Specifications Si39 502A 42 Specifications...
Page 143: ...Field Setting Si39 502A 132 Test Operation...
Page 258: ...Si39 502A Wiring Diagrams for Reference Appendix 247 FXCQ40M 50M 80M 125MVE 3D039557A...
Page 260: ...Si39 502A Wiring Diagrams for Reference Appendix 249 FXKQ25M 32M 40M 63MVE 3D039564A...
Page 264: ...Si39 502A Wiring Diagrams for Reference Appendix 253 FXMQ40M 50M 63M 80M 100M 125MVE 3D039620A...
Page 265: ...Wiring Diagrams for Reference Si39 502A 254 Appendix FXMQ200M 250MVE 3D039621A...
Page 266: ...Si39 502A Wiring Diagrams for Reference Appendix 255 FXHQ32M 63M 100MVE 3D039801C...
Page 267: ...Wiring Diagrams for Reference Si39 502A 256 Appendix FXAQ20M 25M 32M 40M 50M 63MVE 3D034206A...
Page 269: ...Wiring Diagrams for Reference Si39 502A 258 Appendix FXUQ71M 100M 125MV1 3D044973...
Page 270: ...Si39 502A Wiring Diagrams for Reference Appendix 259 FXAQ20MH 25MH 32MH 40MH 50MHV1 3D046348A...
Page 271: ...Wiring Diagrams for Reference Si39 502A 260 Appendix FXLQ20MH 25MH 32MH 40MH 50MHV1 3D046787A...
Page 272: ...Si39 502A Wiring Diagrams for Reference Appendix 261 BEVQ50MVE 3D046579A Notes...
Page 273: ...Wiring Diagrams for Reference Si39 502A 262 Appendix BEVQ71M 100M 125MVE 3D044901A Notes...
Page 285: ...Piping Installation Point Si39 502A 274 Appendix...
Page 293: ...Method of Replacing The Inverter s Power Transistors and Diode Modules Si39 502A 282 Appendix...
Page 307: ...Si39 502A iv Index...