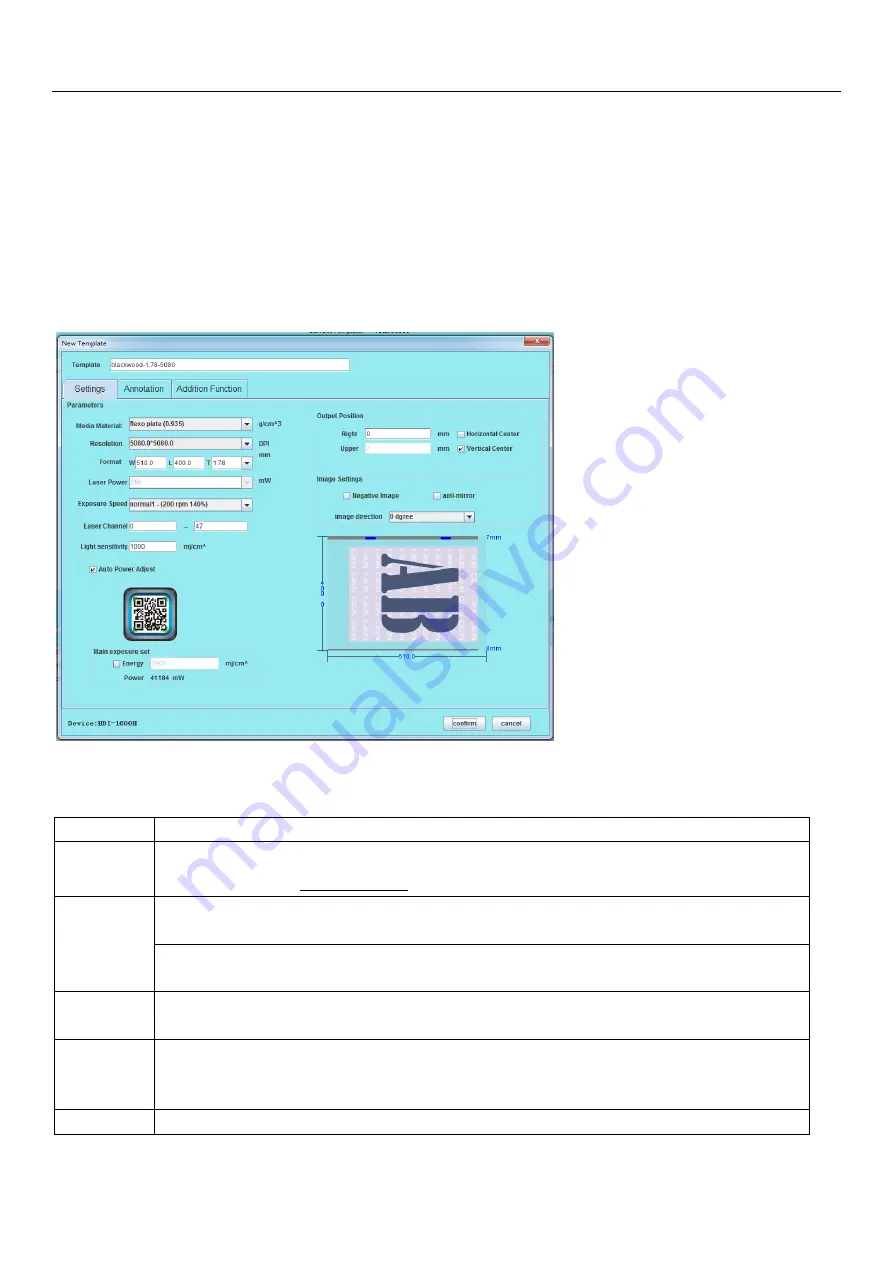
Operation Instructions
22
/
55
5.4 Create work template
Once device’s parameter valueis correctly loaded into LaBoo-HDI software, you can proceed with the
software for further operation;
5.4.1 Create new job template: Click the "New Template" button to bring up the new template dialog
box. According to the actual work needs, setup a job template, in this case we have added a 510x400 PS
platetemplate for the operation; confirm setup once done to establish of a hot folder that can facilitate
subsequent jobs that relevant to this template settings.
Table 5.1:Term Explanation
Field
Description
Template
Set the template name; Recommended naming conventions: plate brand model - thickness -
resolution.Example: Flexo-1.78-5080
Media
Material
Set the material used in the template. Support materials: PS plate, film, flexo. (Different
model’s configuration, available material selection may be different).
Note: Material setting incorrect will cause out of focus, device jitter and other issues, including
affecting the imaging quality.
Resolution
Set the resolution for the template to work with.(Different model’s configuration, available
resolution may be different).
Format
Set the plate size of the jobs template. Size direction refers to the lower right
diagram.Thickness should be in accordance with the actual measurement. (Available largest
and smallest format depends on HDI model).
Laser Power Laser power is set manually, in accordance with the energy needs of the plate, value should