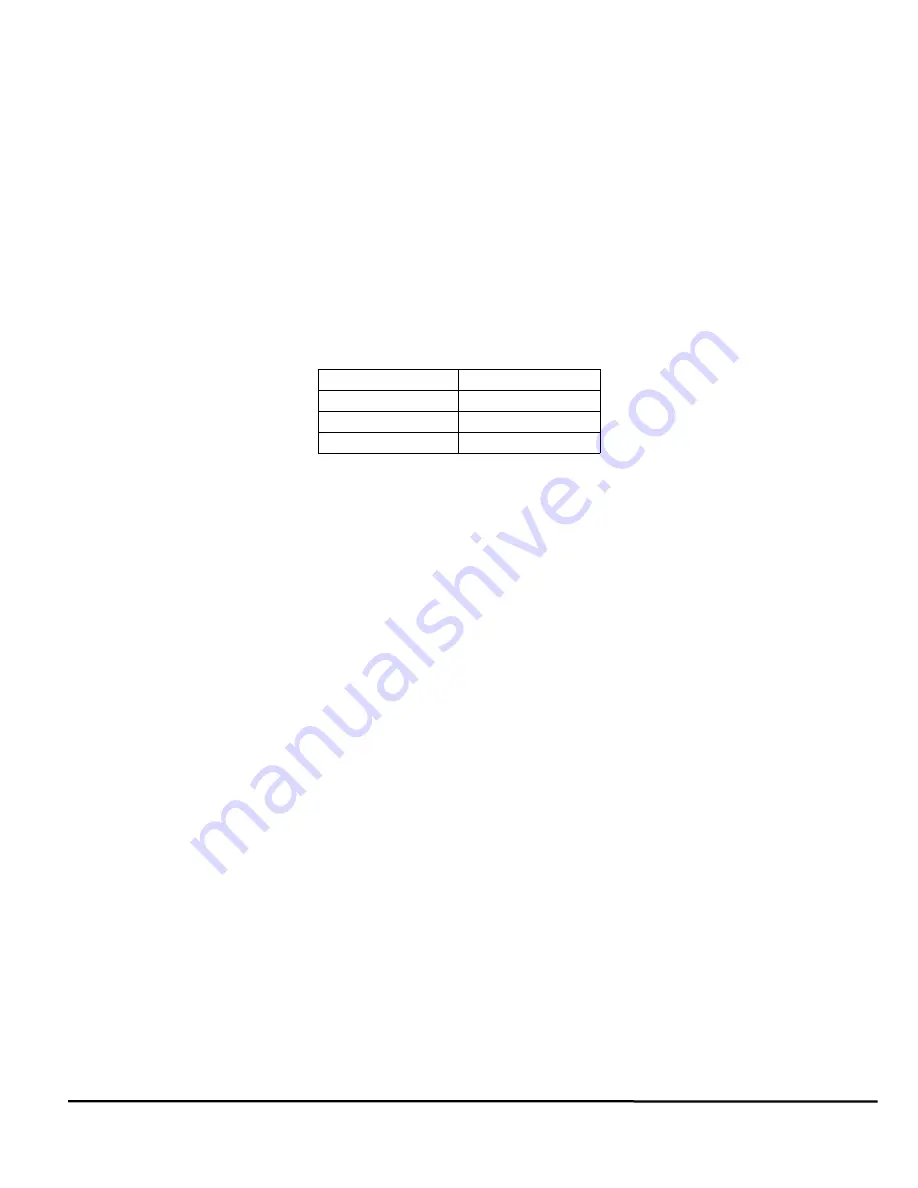
Epsilon EP-P Drive Reference Manual
57
Revision A4
www.controltechniques.com
activate. As the motor continues in the same direction, the PLS.#.Status will deactivate when feedback position reaches or
exceeds the OffPosn. If motor travel changes to the negative direction, the PLS.#.Status will activate when feedback position
reaches the OffPosn, and will deactivate when it continues past the OnPosn.
PLS.#.Status will be active if:PLS.#.OnPosn < Feedback Position
PLS.#.OffPosn
If using negative values for your OnPosn and OffPosn, the most negative value should go in the OnPosn parameter, and the
least negative value should go in the OffPosn.
If the PLS has a rollover point, and the OnPosn is greater than the OffPosn, the PLS will be active whenever the position
feedback is not between the On and Off positions, and in-active whenever the position feedback is between the two positions.
However, the PLS.#.Status will not turn on until it reaches the OnPosn the first time.All on/off positions are defined in user
units.
Direction
This parameter (PLS.#.Direction) specifies the direction of motion that a particular PLS output will function. If set to Both, the
PLS will activate regardless of whether the motor (or master motor) is moving in the positive or negative direction. If set to
Plus, the PLS will activate only when the motor is moving in the positive direction. If set to Minus, the PLS will activate only
when the motor is moving in the negative direction.
Example:
A flying cutoff or flying shear application may use this feature to activate the PLS to fire the knife only when the axis is
moving in the positive direction.
If accessing this parameter from a network, the following table displays the value for this 16-bit integer.
Rotary Enable
This parameter (PLS.#.RotaryRolloverEnable) is used to enable the RotaryRolloverPosn for this PLS.
Rollover Point
This parameter (PLS.#.RotaryRolloverPosn) is the absolute position of the first repeat position for this PLS. When enabled it
causes the PLS to repeat every time this distance is passed. The repeating range begins at an absolute position of zero and
ends at the RotaryRolloverPosn.
For example, in a rotary application a PLS could be setup with an OnPosn of 90 degrees and an OffPosn of 100 degrees. If
the RotaryRolloverPosn is set to 360 degrees the PLS would come on at 90, go off at 100, go on at 450 (360+90), go off at 460
(360+100), go on at 810 (2*360+90), go off at 820 (2*360+100), and continue repeating every 360 degrees forever.
Example: if the source of the PLS is FreeRunTime, this parameter is the time of the first repeat for this PLS. When enabled it
causes the PLS to repeat every time this time is passed. The repeating range begins at the beginning of the trajectory update
rate and ends at the RotaryRolloverPosn.
3.20
Capture View
Many applications require the ability to accurately capture a position at an exact moment in time so that the motion profile can
be repeatably time accurate. The Epsilon EP-P drive allows for this by using the Capture component. The Capture component
is fully controlled by the user through the Assignments View or through the Programs View. When the capture is activated, the
following parameters are captured and stored: Time, Command Position, Feedback Position, and Master Feedback Position.
0
N/A
1
Both
2
Plus
3
Minus
Summary of Contents for Epsilon EP-P
Page 2: ......
Page 124: ...110 Epsilon EP P Drive Reference Manual www controltechniques com Revision A4...
Page 200: ...186 Epsilon EP P Drive Reference Manual www controltechniques com Revision A4...
Page 218: ...204 Epsilon EP P Drive Reference Manual www controltechniques com Revision A4...
Page 238: ...224 Epsilon EP P Drive Reference Manual www controltechniques com Revision A4...
Page 244: ...230 Epsilon EP P Drive Reference Manual www controltechniques com Revision A4...
Page 247: ......