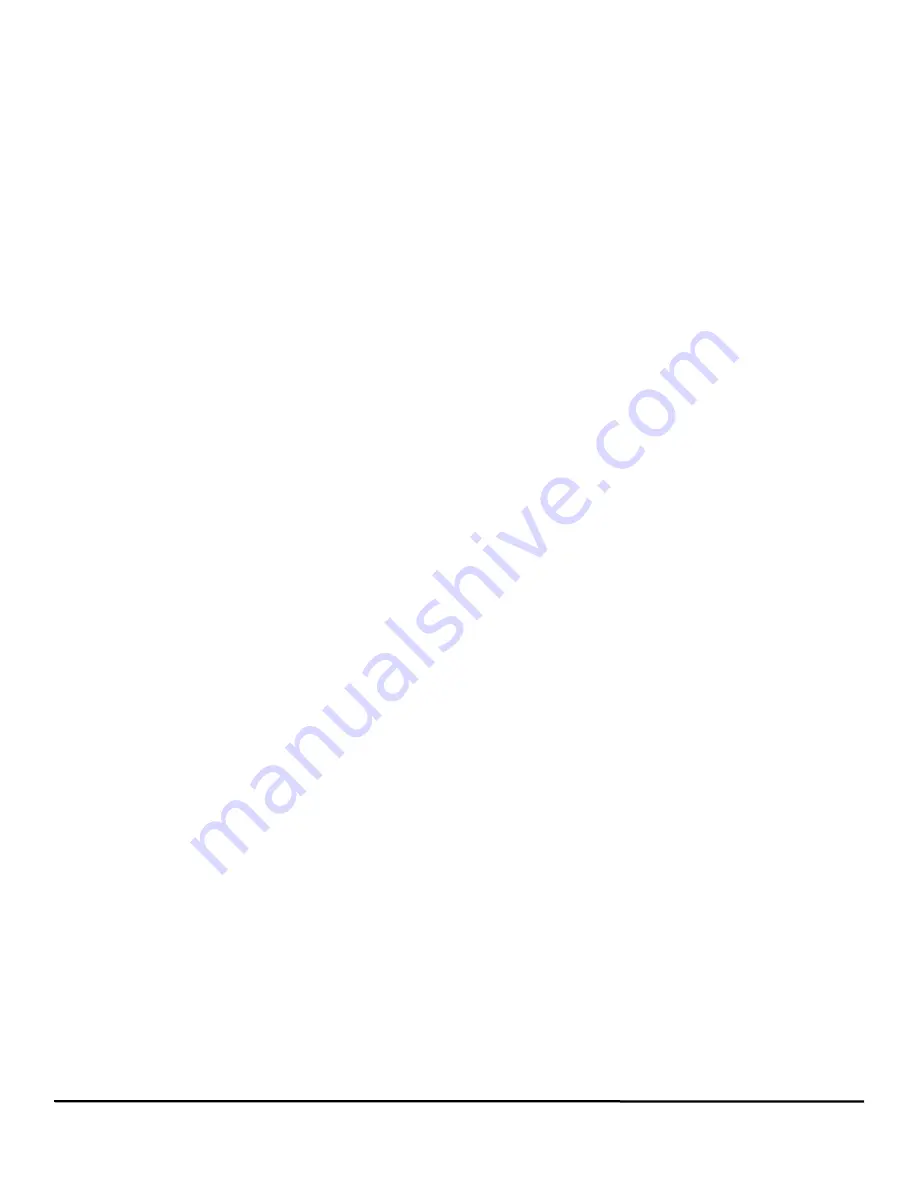
30
Epsilon EP-P Drive Reference Manual
www.controltechniques.com
Revision: A4
2.
Create a custom motor that has not been used before.
When selecting option 1 from above (use an existing motor), the user simply selects one of the motors from the Motor Type list at the top of the
Motor view. Once the user selects a motor from the Motor Type list, the data for that motor is read from the pertinent .ddf file and then is
displayed in the Motor Parameters column on the Motor view (see Figure 37). The parameters in this column will be dimmed and unavailable
because the motor information comes directly from the .ddf file.
If the user wishes to edit one or more of the parameters read from the .ddf file, it is necessary to clear the “User Motor Data From .ddf File”
check box. Clearing the check box will break the “link” between the motor data displayed on this view, and the motor data in the .ddf file. This
is necessary because as soon as the user changes any of the values, it no longer matches the .ddf file, and is now in effect a “custom motor”.
When the “User Motor Data From .ddf File” check box is cleared, all of the values in the Motor Parameters column will become available, and
the Motor Name will be changed to “New Motor” so that there is no association with the existing motor that was previously selected. The user
can now change any of the values as desired and give the motor a new name. Once the values have been changed, the motor data only exists
within the active configuration. To save the new values into the .ddf file, the user must click on the Save .ddf Values button on the right side of
the view.
3.4.3
Motor Parameters Column
Motor Parameters column is a column of data displayed on the Motor view under the Setup view (See Figure 37). This column of data contains
the values for each of the motor data parameters. The values in this column are unavailable for edit if the “Use Motor Data From .ddf File”
check box is selected. This means that since the data is associated with the .ddf file, it cannot be changed. The values in this column become
available when the “Use Motor Data From .ddf File” check box is cleared. The user can then change one or more of the parameter values
because there no longer is a link to the data in the .ddf file.
If the user does edit motor parameter values on this view, those values are only stored within that particular configuration file. In order to save
the values to the .ddf file, the user must click the “Save .ddf Values” button on the right side of the view. Below are the motor parameter with a
brief description.
Motor Name
The motor name is limited to 12 characters and must begin with an alpha character (non-numeric character). This is the motor name that will
appear in the “Motor Type” list box above.
Peak Current
Specifies the peak current allowed by the motor. The motor manufacturer typically provides the peak current data.
If a system is “drive limited” (meaning that the motor can handle more current than the drive can deliver), the peak current actually used by the
system may be lower than the value specified here.
Continuous Current Rating
Specifies the continuous current allowed by the motor. It is used to determine the drive continuous current and peak current limits. The drive
can also limit the continuous current to the motor based on the drive capacity. The motor manufacturer typically provides the continuous
current data.
If a system is “drive limited” (meaning that the motor can handle more current than the drive can deliver), the continuous current actually used
by the system may be lower than the value specified here.
Motor Poles
Specifies the number of magnetic pole pairs (N-S) on the motor. The supported values are 2, 4, 6, 8, 10, 12, 14 and 16 poles. The motor
manufacturer typically provides the motor pole information.
Rotor Inertia
This parameter specifies the inertia of the motor rotor. The drive uses this parameter to interpret the “Inertia Ratio” parameter. “Inertia Ratio” is
specified as a ratio of reflected load inertia to motor inertia.
Motor KE
Specifies the Ke of the motor. The units are Vrms/ kRPM. The line-to-line voltage will have this RMS value when the motor is rotated at 1000
RPM. The range is 5.0 to 500.0 Vrms/ kRPM. The motor manufacturer will typically provide the Ke data.
Phase Resistance
Specifies the phase-to-phase resistance of the motor. This value is determined by measuring the resistance between any two motor stator
terminals with an ohm meter. The range is.1 to 50 ohms.
Phase Inductance
Specifies the phase-to-phase inductance of the motor.
Max Operating Speed
This parameter specifies the maximum speed of the motor when used with a variable speed drive to achieve velocities over the rated base
speed of the motor.
Encoder Lines/Rev
Specifies a coefficient for determining the number of encoder lines per mechanical revolution. The supported values are 1 to 16383. The
equation for determining the total number of encoder lines per revolutions is:
nLines = n*10x
where:
nLines = Total number of Encoder Lines
n = Motor Encoder Lines per Rev Coefficient
x = Motor Encoder Exponent
The total number of encoder lines is used both for commutation and for position/velocity control. To properly commutate the motor, the drive
Summary of Contents for Epsilon EP-P
Page 2: ......
Page 124: ...110 Epsilon EP P Drive Reference Manual www controltechniques com Revision A4...
Page 200: ...186 Epsilon EP P Drive Reference Manual www controltechniques com Revision A4...
Page 218: ...204 Epsilon EP P Drive Reference Manual www controltechniques com Revision A4...
Page 238: ...224 Epsilon EP P Drive Reference Manual www controltechniques com Revision A4...
Page 244: ...230 Epsilon EP P Drive Reference Manual www controltechniques com Revision A4...
Page 247: ......