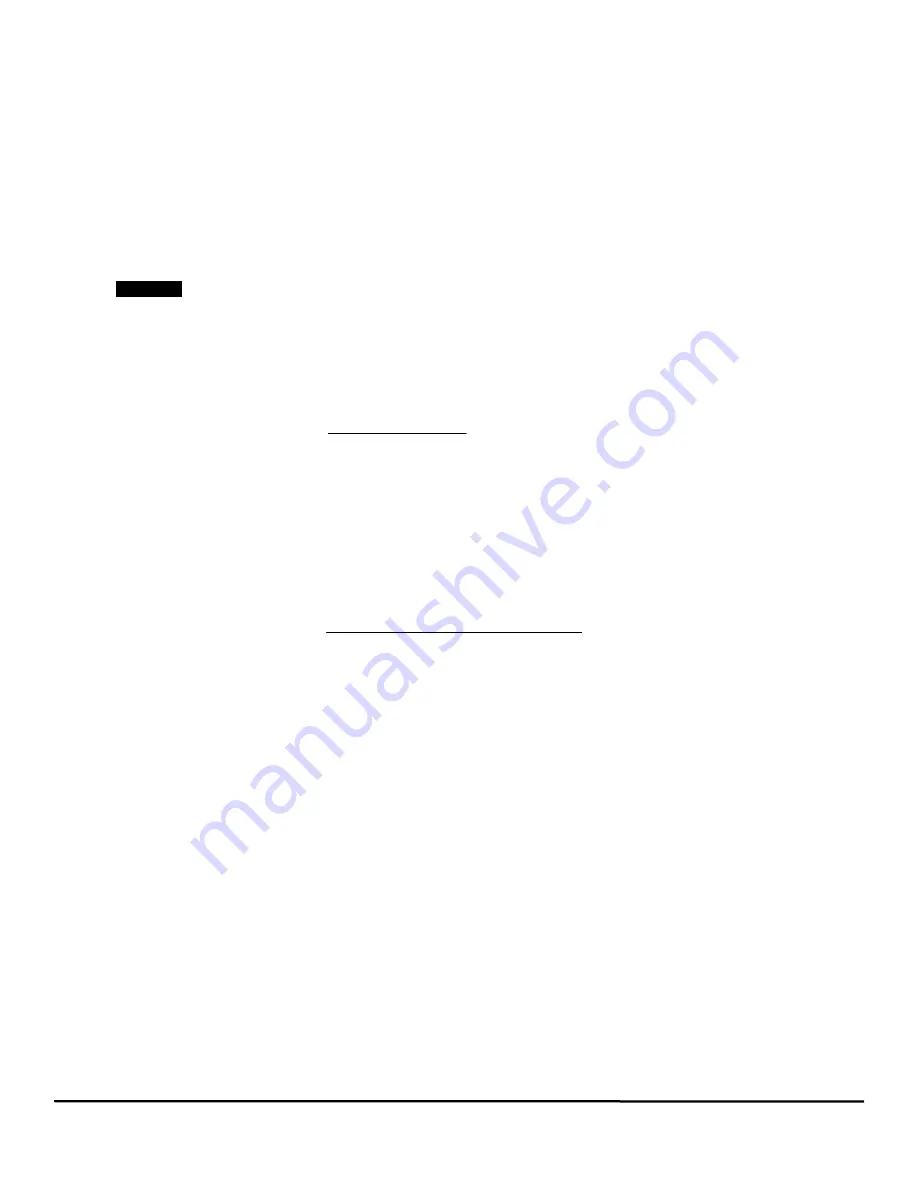
192
Epsilon EP-P Drive Reference Manual
www.controltechniques.com
Revision: A4
Consider the following before determining the inertia:
•
The accel and decel ramp should be aggressive enough to require at least 20 percent of continuous motor torque. The higher the torque
used during the ramp, the more accurate the final result will be.
•
With ramps that take less than 1/2 second to accelerate, use PowerTools graph to measure the Torque Feedback.
•
With ramps that take 1/2 second or longer to accelerate, read the Torque Command parameter on the Torque view, while online, or with
the Watch Window.
•
To best determine the inertia, use both acceleration and deceleration torque values. The difference allows you to drop the constant friction
out of the final calculation.
•
If your application exerts a constant “unidirectional loading” throughout the travel such as in a vertical axis, the inertia test profiles must be
performed in both directions to cancel out the unidirectional loading effect.
•
The Torque Command Limited and Velocity Feedback parameters can be measured using the drive’s Analog Outputs or PowerTools Pro
graph.
These will be needed for systems with limited travel moves and rapidly changing signals of torque and velocity.
Inertia Measurement Procedure:
NOTE
The test profile will need to be run a number of times in order to get a good sample of data.
1.
Enable the drives and run the test profiles.
2.
Note the Torque Command Limited value during acceleration and deceleration.
3.
Use the appropriate formula below to calculate the inertia.
For horizontal loads or counterbalanced vertical loads use the following formula:
Where:
IR = Inertia Ratio
R = ramp in ms/kRPM
Ta = (unsigned) percent continuous torque required during acceleration ramping (0 - 300)
Td = (unsigned) percent continuous torque required during deceleration ramping
(0 - 300)
Vm = MotorKt * System Continuous Current / Motor Inertia in Kg-cm
2
For un-counter balanced vertical loads use the following formula:
Where:
IR = Inertia Ratio
R = ramp in ms/kRPM
Vm = MotorKt * System Continuous Current / Motor Inertia in Kg-cm
2
Tau = (unsigned) percent continuous torque required during acceleration ramping while moving up (against the constant force)
Tdu = (unsigned) percent continuous torque required during deceleration ramping while moving up (against the constant force)
Tad = (unsigned) percent continuous torque required during acceleration ramping while moving down (aided by the constant force)
Tdd = (unsigned) percent continuous torque required during deceleration ramping while moving down (aided by the constant force)
1
2000
Td))
(Ta
Vm
(R
IR
1
4000
Tdd))
Tad
Tud
(Tau
Vm
(R
IR
Summary of Contents for Epsilon EP-P
Page 2: ......
Page 124: ...110 Epsilon EP P Drive Reference Manual www controltechniques com Revision A4...
Page 200: ...186 Epsilon EP P Drive Reference Manual www controltechniques com Revision A4...
Page 218: ...204 Epsilon EP P Drive Reference Manual www controltechniques com Revision A4...
Page 238: ...224 Epsilon EP P Drive Reference Manual www controltechniques com Revision A4...
Page 244: ...230 Epsilon EP P Drive Reference Manual www controltechniques com Revision A4...
Page 247: ......