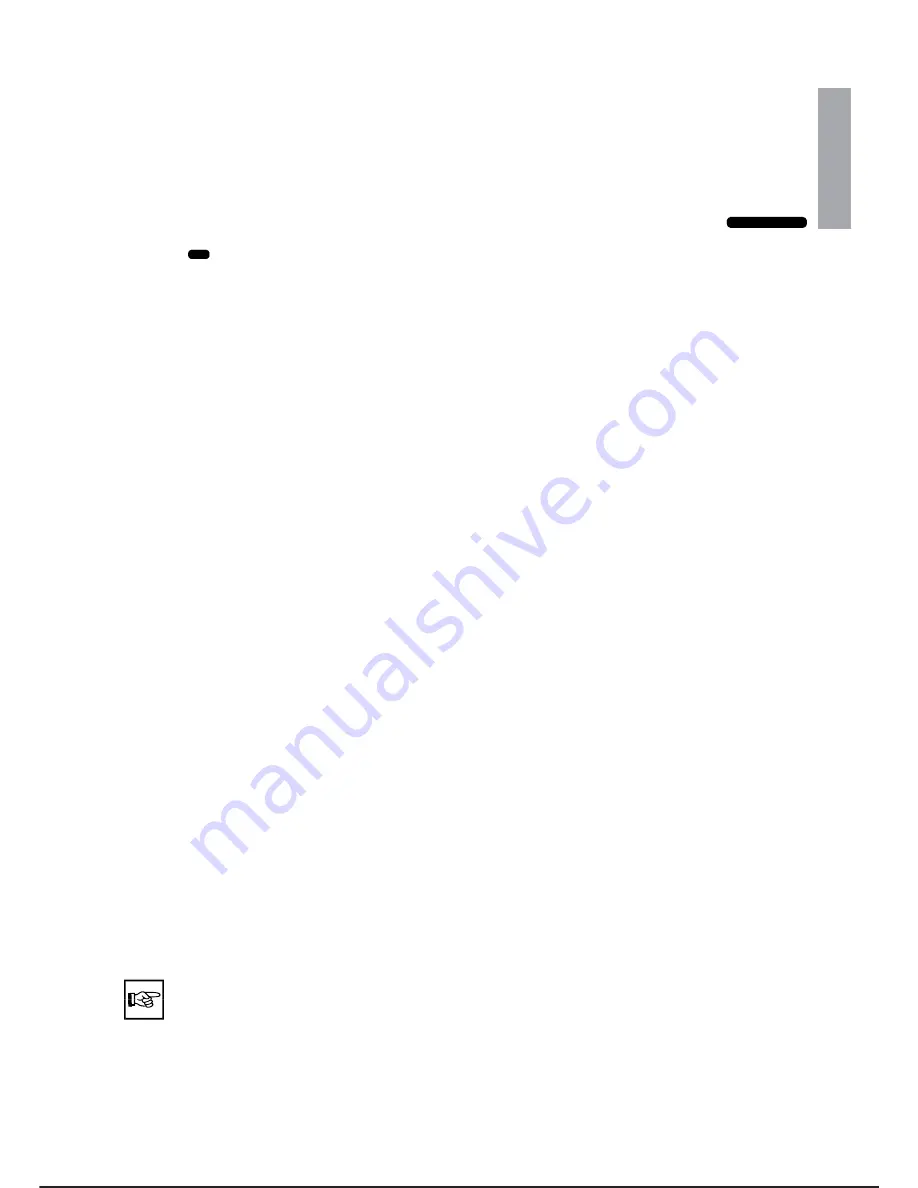
The calibration constants are stored in the variable $ARM_DATA[arm_num].CAL_DATA, in the ASCII
calibration file, in the C3G.SYS file, in the Flash Eprom on SAU2 or RPT (optional).
For robots with particular mechanical structures (e.g. TRICEPT HP1) specific calibration programmes
are foreseen.
The calibration command also allows other options (which can be activated by pressing the
and
keys on the programming terminal together).
Example:
a.
/Learn
This option makes it possible to define a user calibration position. The operator must move the robot
to the required position and invoke the CAC/L command. At this point the calibration position is
stored in the system variable $ARM_DATA[arm_num].CAL_USER.
System calibration must be carried out prior to this operation.
b.
/User
This
option
calibrates
on
the
position
stored
in
the
system
variable
$ARM_DATA[arm_num].CAL_USER.
Once this operation has been performed, the calibration error is stored in the same system variable
dedicated to the system calibration error.
·
TURN-SET
This operation must be performed if the control unit knows the calibration constants but has lost the in-
formation about the number of resolver revolutions. The information is lost by the control unit if, at re-
start, the RPT module (if present) does not provide the number of resolver revolutions correctly, or due
to resolver errors, and/or due to slipping of the axes with the controller off without RPT.
The operator must move the robot onto the reference indexes as accurately as possible: if the robot is
not positioned correctly, the system alerts the operator with the 59409 SAX: joint position not suffi-
ciently accurate error and then with the 59421 SAX: positive adjustment is required error and/or
with the 59422 SAX: negative adjustment is required error. Once the robot is positioned the operator
must invoke the CAT (Configure Arm Turn-set) command.
Following this command the system recalculates the correct number of resolver revolutions. This operation
must be performed only on the axis for which the count has been lost; if several axes are found to be in the
above situation, it is advisable to perform the turn-set operation on one axis at a time. In particular, if there
are axes that influence each other, operate first on the influencing axis and then on the influenced axis.
The Turn-set command has two options:
a.
/Current
This option is enabled only if the RPT device is present.
If the resolver revolution count has been lost with the controller on, it is possible to pre-set the
number of resolver revolutions using the current robot position, with the Configure Arm
Turn-set/Current (CAT/C) command.
Do not switch the control unit off since when you have noticed that the revolver revolution
count has been lost till commanding the Turn-set .
b.
/User
The User option allows recalculation of the number of resolver revolutions with reference to user
calibration.
C3G
Plus
MAIN OPERATIONS FOR SYSTEM USE
07/1200
5-15
CALIBRATION
SHIFT
/
9
Summary of Contents for C3G Plus
Page 6: ...This page has been intentionally blank UPDATING LIST C3G Plus D 08 0702 ...
Page 14: ...This page has been intentionally blank Operations and Maintenance Manual C3G Plus ...
Page 24: ...This page has been intentionally blank Operations and Maintenance Manual C3G Plus ...
Page 26: ...This page has been left intentionally blank INSTALLATION C3G Plus 2 ii 01 0498 SUMMARY ...
Page 48: ...This page has been intentionally blank Operations and Maintenance Manual C3G Plus ...
Page 122: ...This page has been intentionally blank Operations and Maintenance Manual C3G Plus ...
Page 127: ...C3G Plus INTEGRATION GUIDE 06 0400 4 5 SYSTEM I O ...
Page 160: ...This page has been intentionally blank Operations and Maintenance Manual C3G Plus ...
Page 182: ...This page has been intentionally blank Operations and Maintenance Manual C3G Plus ...
Page 188: ...This page has been intentionally blank Operations and Maintenance Manual C3G Plus ...
Page 190: ...This page has been left intentionally blank MAINTENANCE C3G Plus 7 ii 00 1097 GENERAL RULES ...
Page 225: ...X30 connector test device C3G Plus MAINTENANCE 01 0498 7 35 diagnostic ...
Page 264: ...This page has been intentionally blank 7 74 08 0702 MAINTENANCE C3G Plus LIST OF SPARE PARTS ...
Page 265: ...OPERATOR S NOTES C3G Plus NOTES ...
Page 266: ...C3G Plus NOTES ...