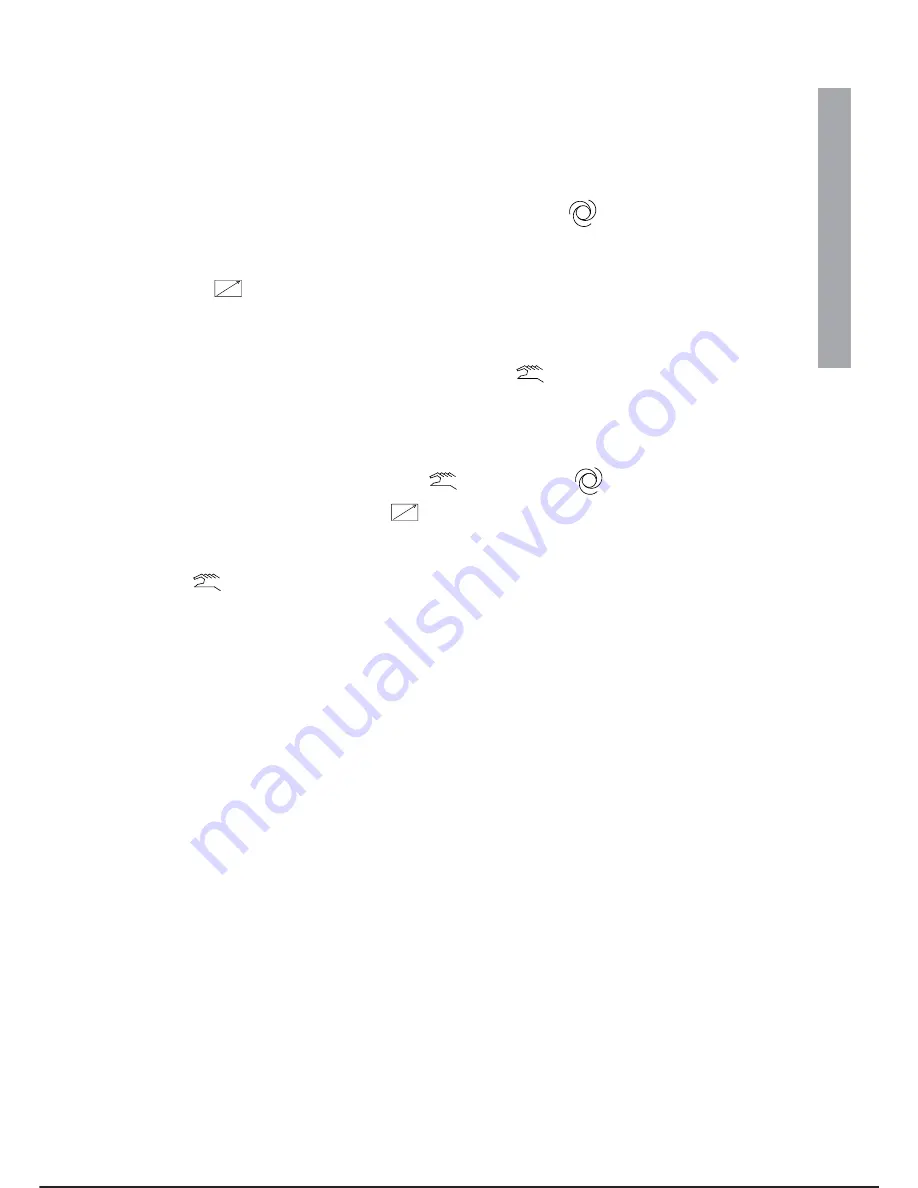
SYSTEM OPERATING MODES
The controller can work in three ways, which can be selected through the status selector on the control panel
of the controller: automatic local, automatic remote and programming.
The automatic local mode makes it possible to execute production programmes which, as they contain in-
structions for robot movement, can be started by pressing the START button on the PTU4 programming ter-
minal. The status selector should be set to the automatic local position
.
The automatic remote mode is similar to automatic local, but the commands for example for starting are sent
from a remote device, such as PLC or work station. The status selector should be set to the automatic re-
mote position
.
The programming mode is used when creating and checking the programmes. For safety reasons, robot
movements are performed at lower speed than in the automatic mode (the maximum speed of a robot al-
lowed during programming is 250 mm/sec on the centre of the flange).
The status selector should be set to the programming position
. Programmes can be developed using
the editor environment (for further information see the C3G Programming Guide). The points can be learnt
by the programming terminal moving the robot manually with the movement buttons, the programmes can be
fine-tuned using the debug tools offered by the system. During programming, to execute a movement in-
struction, the operator must press the START button and the enable button on the programming terminal.
When the status selector is set to programming
or automatic local
, operation is in the local mode.
When the selector is at automatic remote
, operation is remote.
Before being able to perform any operation requiring movement, the drives power has to be switched on.
This takes place pressing the DRIVE ON button on the programming terminal. If the status selector is at pro-
gramming
, the enable button should also be kept pressed to power the drives. To turn the drives off
and activate the brakes for all the robots connected to the controller, simply release the enable button.
SYSTEM STATUSES
The status the system is in mainly depends on:
·
the status selector on the control panel
·
the optional AUTO/MAN selector on the programming terminal
·
the DRIVE ON, DRIVE OFF and HOLD keys on the programming terminal
System transition from one status to the other is also affected by the enable button and the terminal on con-
trol unit button, both on the programming terminal.
The controller may be in one of the following four statuses:
·
AUTO: this is the status generally used for executing production programmes which control robot move-
ment.
·
PROG: in this status the robot can be moved manually using the jog keys or executing programme instruc-
tions (from editor environment or EXECUTE command). In the latter case, the START button and the enable
button must be kept pressed to be able to perform the movement.
If the C3G-CSM (Controlled Stop Module) is installed on the controller, in AUTO LOCAL and AUTO RE-
MOTE states, an emergency stop and/or opening of the safety gates causes controlled stopping of the robot
(EN 60204-1), category 1 stop). In this way, power is cut off (opening of the power contactor) after 1 second.
In PROGR. programming status, the power is cut off immediately (EN 60204-1, category 0 stop).
·
HOLD: in this status the arm is gradually decelerated until reaching the stopping point; the movement is
suspended and also execution of the movement programmes (called holdable). When all the conditions
necessary to exit the HOLD status are fulfilled, the system returns to the previous status (programming
or automatic) but, it is necessary to press the START button to resume execution of the movement
programmes.
C3G
Plus
MAIN OPERATIONS FOR SYSTEM USE
02/1198
5-1
SYSTEM
OPERATING
MODES
Summary of Contents for C3G Plus
Page 6: ...This page has been intentionally blank UPDATING LIST C3G Plus D 08 0702 ...
Page 14: ...This page has been intentionally blank Operations and Maintenance Manual C3G Plus ...
Page 24: ...This page has been intentionally blank Operations and Maintenance Manual C3G Plus ...
Page 26: ...This page has been left intentionally blank INSTALLATION C3G Plus 2 ii 01 0498 SUMMARY ...
Page 48: ...This page has been intentionally blank Operations and Maintenance Manual C3G Plus ...
Page 122: ...This page has been intentionally blank Operations and Maintenance Manual C3G Plus ...
Page 127: ...C3G Plus INTEGRATION GUIDE 06 0400 4 5 SYSTEM I O ...
Page 160: ...This page has been intentionally blank Operations and Maintenance Manual C3G Plus ...
Page 182: ...This page has been intentionally blank Operations and Maintenance Manual C3G Plus ...
Page 188: ...This page has been intentionally blank Operations and Maintenance Manual C3G Plus ...
Page 190: ...This page has been left intentionally blank MAINTENANCE C3G Plus 7 ii 00 1097 GENERAL RULES ...
Page 225: ...X30 connector test device C3G Plus MAINTENANCE 01 0498 7 35 diagnostic ...
Page 264: ...This page has been intentionally blank 7 74 08 0702 MAINTENANCE C3G Plus LIST OF SPARE PARTS ...
Page 265: ...OPERATOR S NOTES C3G Plus NOTES ...
Page 266: ...C3G Plus NOTES ...