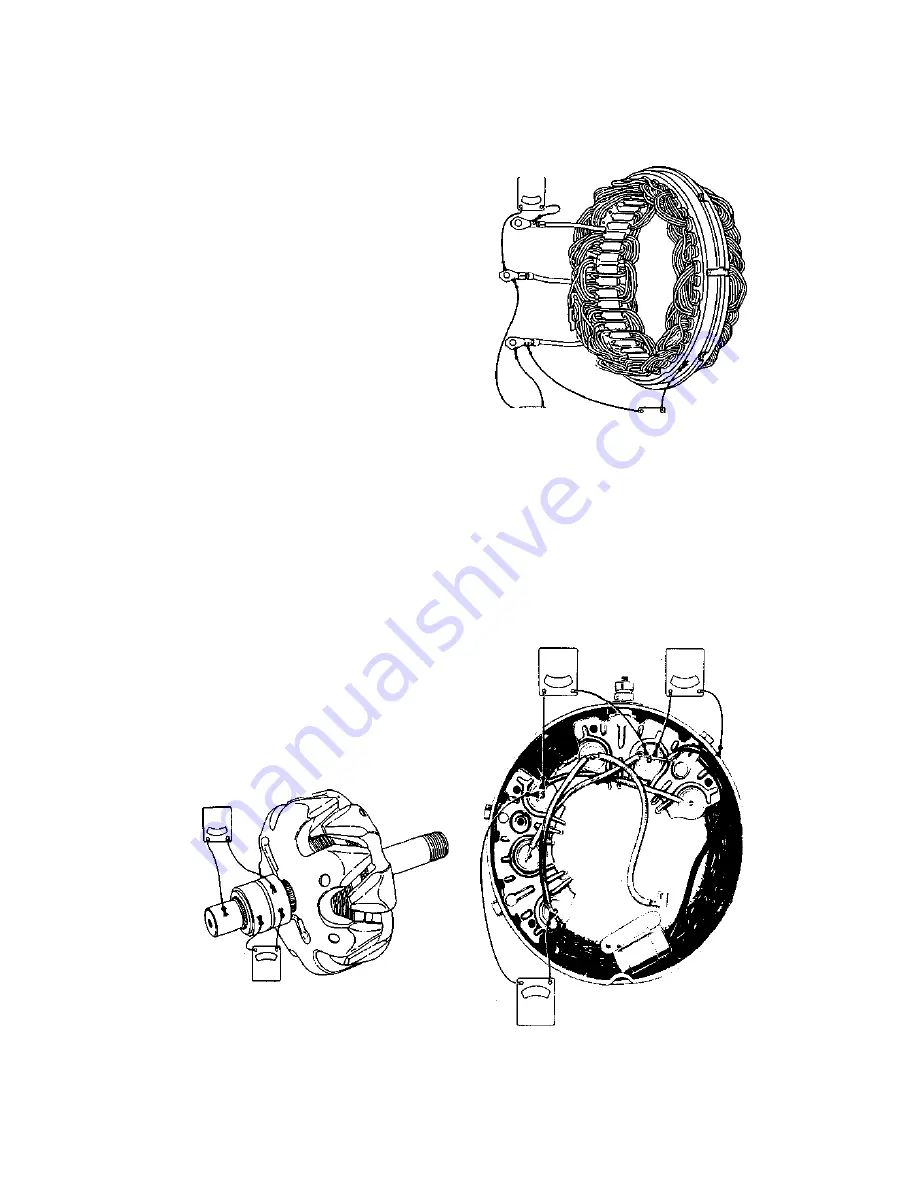
ENGINE AND ENGINE REBUILDING 77
3. Inspect rotor slip rings for scoring. They
may be cleaned with 400 grit sandpaper (not
emery), rotating the rotor to make the rings
concentric. Maximum out-of-true is 0.001 in.
If slip rings are deeply scored, the entire ro
tor must be replaced as a unit.
4. Inspect brushes for wear; minimum
length is
¥4
in.
ALTERNATOR COMPONENT TESTING
Rotor *
Attach one lead of a 110 volt test lamp or an
ohmmeter to either slip ring, and the other
lead to the rotor shaft or poles. A lighted test
lamp or low ohmmeter reading indicates
grounded field windings.
Attach the lamp or ohmmeter connections
to each slip ring. The windings are open if
the lamp fails to light or the ohmmeter read-
ing is high.
Connect a 12 volt battery and an ammeter
in series with the slip rings to check for shorts.
The windings are shorted if the reading ex-
ceeds 1.5 amps. An ohmmeter may be sub-
stituted for the same check and will show a
resistance reading of less than 6 ohms if the
windings are shorted.
Stator
Attach the test lamp or ohmmeter to the sta-
tor frame and one of the stator leads. A lighted
lamp or low resistance reading indicates
grounded windings.
Successively connect the test equipment
between each pair of stator leads. Open
windings will produce a high resistance and
prevent the test lamp from lighting.
Shorts require special test equipment. If
(CHECK FOR
TESTING ROTOR
GROUNDSKOHMMETER).
TESTING STATOR
(CHECK FOR OPENS)
OHMMETER
OHMMETER
(CHECK FOR
OPENS)
Stator testing—except "perforated
case" models
OHMMETER
CHECK FOR OPENS
Rotor testing
OHMMETER
(CHECK FOR
GROUNDS)
OHMMETER