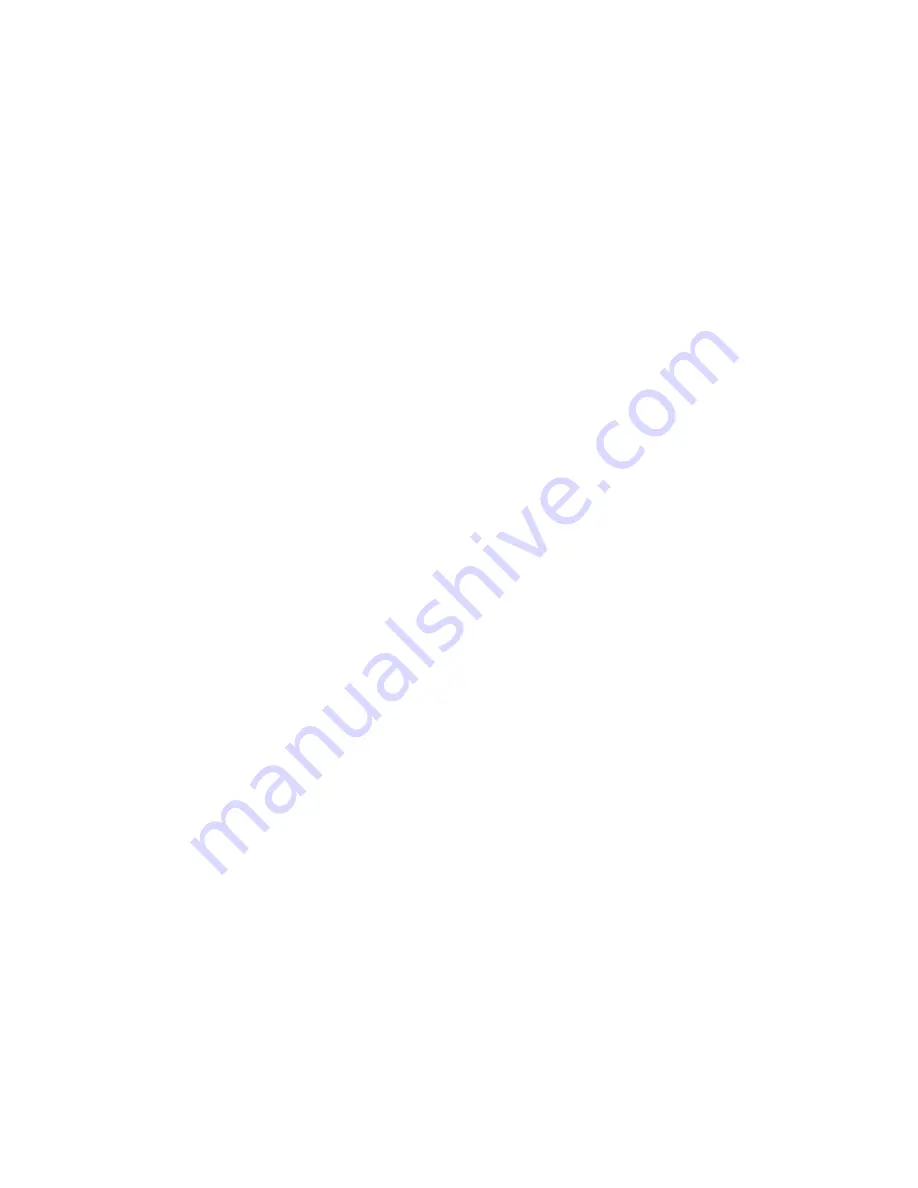
EMISSION CONTROLS AND FUEL SYSTEM 149
sure on the gauge. Fuel pressure should be
9-13 psi. Turn the engine OFF. Replace the
fuel pump if the pressure is not within this
range.
6. Remove the fuel pressure gauge, install
the fuel tube assembly, and check for leaks.
7. Reinstall the air cleaner and connect the
vacuum lines as originally connected.
Carburetor Overhaul and
Adjustments—AH Types
Efficient carburetor depends greatly on care-
ful cleaning and inspection during overhaul,
since dirt, gum, varnish, water in or on the
carburetor parts are mainly responsible for
poor performance.
Carburetor overhaul should be performed
in a clean, dust-free area. Carefully disassem-
ble the carburetor, keeping look-alike parts
segregated. Note all jet sizes.
NOTE:
The carburetor Specifications Chart at
the end of the chapter gives the various
carburetor applications. Determine which
carburetor you are dealing with and refer to
the following sections. The sections are
divided by carburetor type.
Once the
carburetor is disassembled, wash all parts
(except diaphragms, electric choke units,
pump plunger and any other plastic, leather
or fiber parts) in clean carburetor solvent. Do
not leave the parts in solvent any longer
than necessary to sufficiently loosen the
deposits. Excessive cleaning may remove the
special finish from the float bowl and
choke valve bodies, leaving them unfit for
service. Rinse all parts in clean solvent and
blow dry with compressed air. Wipe all plas-
tic, leather or fiber parts with a clean, lint-
free cloth.
Blow out all passages and jets with com-
pressed air and be sure there are no restric-
tions or blockages. Never use wire to clean
jets, fuel passages or air bleeds.
Check all parts for wear or damage. If wear
or damage is found, replace the complete as-
sembly. Especially check the following:
1. Check the float and needle seat for wear.
If any is found, replace the assembly.
2. Check the float hinge pin for wear and
the floats for distortion or dents. Repkce the
float ifjfiikhas leaked into it.
3. (?necK^he throttle and choke shaft bores
for out-of-round. Damage or wear to the
throttle arm, shaft or shaft bore will often re
quire replacement of the throttle body. These
parts require close tolerances and an air leak
here can cause poor starting and idling.
4. Inspect the idle mixture adjusting
needles for burrs or grooves. Burrs or grooves
will usually require replacement of the
needles since a satisfactory idle cannot be ob
tained.
5. Test the accelerator pump check valves.
They should pass air one way only. Test for
proper seating by blowing and sucking on the
valve. If the valve is satisfactory, wash the
valve again to remove breath moisture.
6. Check the bowl cover for warping with
a straightedge.
7. Closely inspect the valves and seats for
wear or damage, replacing as necessary.
8. After the carburetor is assembled, check
the choke valve for freedom of operation.
Carburetor overhaul kits are recom-
mended for each overhaul. These kits contain
all gaskets and new parts to replace those that
deteriorate most rapidly. Failure to replace
all parts supplied with the kit (especially
gaskets) can result in poor performance
later.
Overhaul kits contain specific procedures
for the model carburetor the kit applies too.
Some carburetor manufacturers supply over-
haul kits of three types—minor repair, major
repair and gasket kits. They basically consist
of Minor Repair Kits:
• All gaskets
• Float needle valve
• Volume control screw
• All diaphragms
• Pump diaphragm spring
Major Repair Kits:
• All jets and gaskets
• All diaphragms
• Float needle valve
• Volume control screw
• Pump ball valve
• Main jet carrier
• Float
• Complete intermediate rod
• Intermediate pump lever
• Complete injector tube
• Assorted screws and washers
Gaskets Kits:
• All gaskets.
After cleaning and checking all compo-
nents, reassemble the carburetor using new
parts, using the exploded views in the car
sections, if necessary. Make sure that all
screws and jets are tigiit in their seats, but do
not overtighten needle valves into their seats