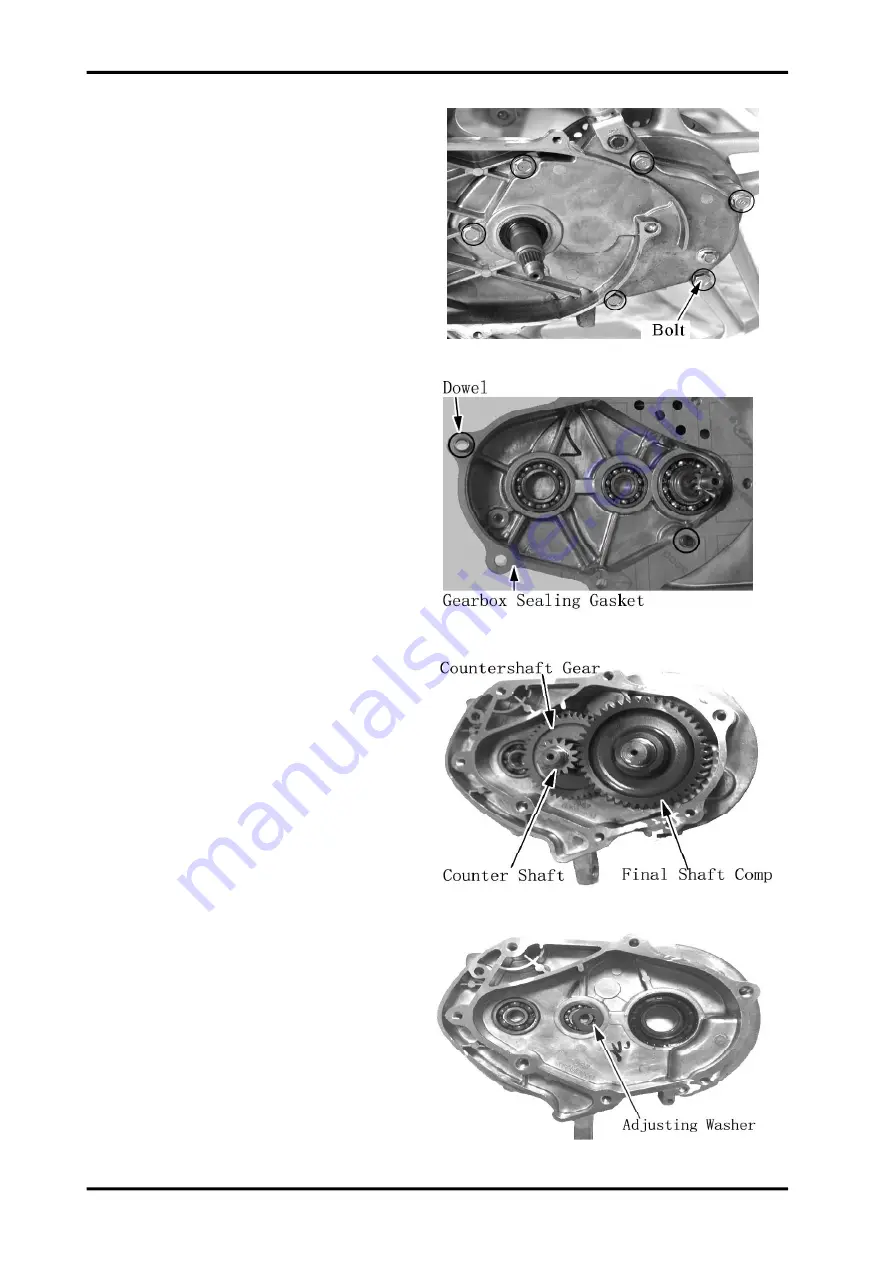
10-2
CFMOTO
Disassembly of gearbox
Drain lubricant from gearbox.(
→
3-10)
Remove:
-R
ear wheel( 4-3 )
-C
lutch assy.( 9-9 )
Remove bolt
Remove gearbox.
Remove dowel pin and gearbox sealing gasket
Wipe off the attached sealant on the joint face.
Remove final shaft comp.
Remove countershaft and gear.
Remove adjusting washer.
Summary of Contents for CF125T-19 2003
Page 1: ...WWW CFMOTO COM CFMOTO CF125T 19 SERVICE MANUAL CF150T VERSION A...
Page 2: ...All right reserved ZHEJIANG HONGQIAO POWER MANUFACTURING CO LTD 2003 5 WWW CFMOTO COM...
Page 23: ...1 19 1 Overhaul Information 1 Wiring Piping Diagram...
Page 24: ...1 20 CFMOTO...
Page 25: ...1 21 1 Overhaul Information 1...
Page 26: ...1 22 CFMOTO...
Page 27: ...1 23 1 Overhaul Information 1...
Page 28: ...1 24 CFMOTO...
Page 29: ...1 25 1 Overhaul Information 1...
Page 48: ...2 17 2 Vehicle body muffler 2 Outer Components...
Page 91: ...5 17 5 carburetor air filter secondary air inlet 5 Air cleaner Assembly...
Page 100: ...6 9 6 cooling system 6 Cooling System...
Page 158: ...10 8 CFMOTO...
Page 208: ...15 Battery Charging system 15 15 9...
Page 215: ...16 16 7 16 Ignition system...
Page 235: ...19 1 CFMOTO 19 Electrical Diagram...
Page 236: ...19 Electrical Diagram 19 2 CFMOTO...