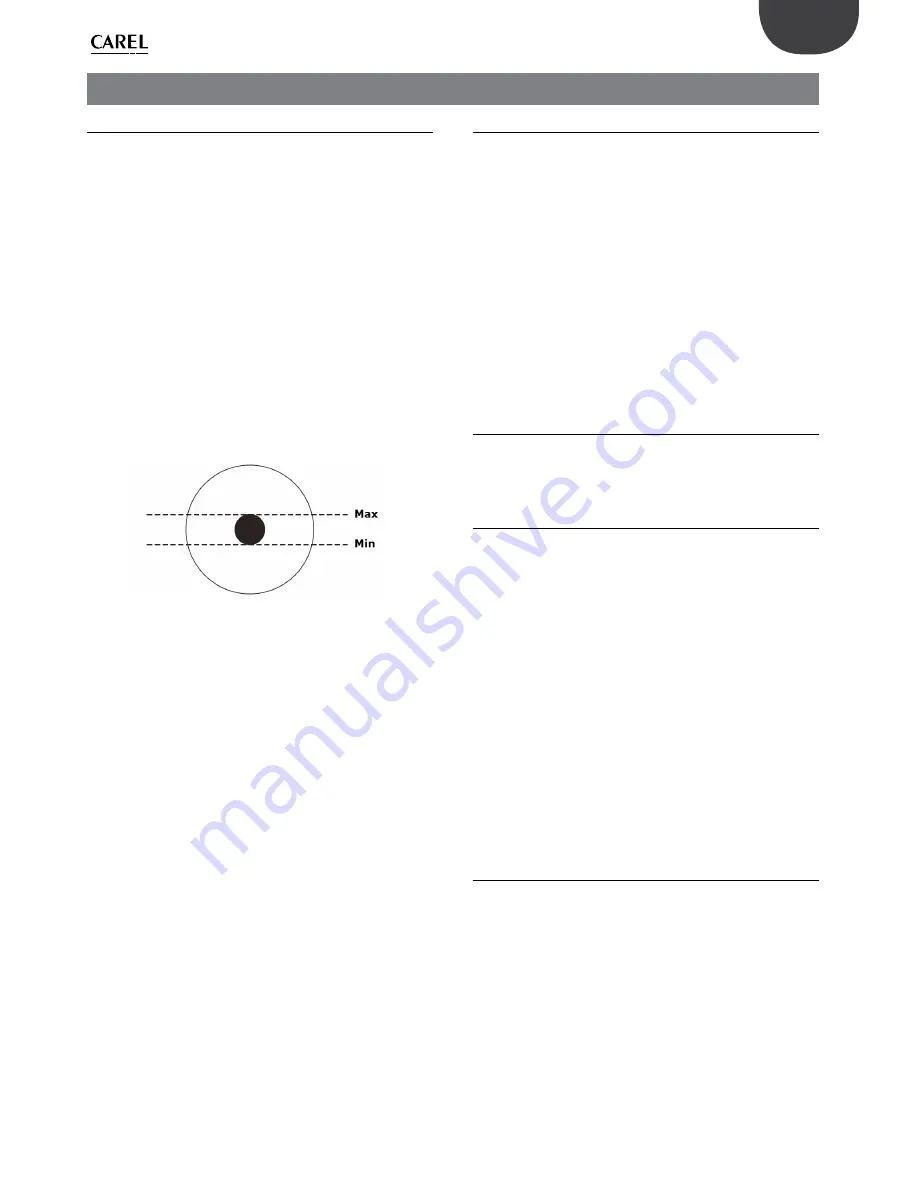
35
ENG
"humiFog direct" +0300073EN rel. 1.0 - 31.03.2017
10.1 Routine maintenance
Routine maintenance is recommended every three months, and mainly
involves visual inspection of correct operation of the main components.
The following is a list of recommended operations:
•
Check water inlet filter.
It is recommended to change the filter cartridge once every 6-12 months.
To change the cartridge, switch the unit off and close the feedwater line.
Empty the filter using the small tap at the bottom. Unscrew the white
holder from the nut at the top using the tool provided. Remove the filter
cartridge inside and fit a new one (P/N ECKFILT050). Tighten the holder,
ensuring that the O-ring is still in good condition to ensure tightness.
Close the tap under the holder and open the feedwater line.
•
Check pump oil level.
To check the level visually, use a mirror that allows a view of side of the
pump facing to the cabinet wall. There is a small mark behind a circular
transparent Plexiglas cover. The oil level is correct when around the
middle of the circle. If the level is lower than the minimum shown in the
figure, top up with oil to the correct level (oil P/N 5024646AXX).
Generally the oil level should remain constant and periodical top ups
should not be needed. If oil leaks are found, contact CAREL.
Fig. 10.a
•
Check the nozzles: make sure the spray cone from the nozzles is
regular.
Even when using demineralised water, some particle may at times
build-up on the nozzle opening, making the spray cone less uniform
and affecting absorption efficiency. If this happens, remove the nozzle
(unscrew using a 10 mm spanner) and clean it (immersing in acetic
acid tom remove scale) or replace it (P/N UAKMTP%000). Before fitting
the nozzle again, remove the residual Teflon from the thread and apply
sealant again to ensure water-tightness.
•
Check the fansi
Make sure that all of the fans on the blower units are working. In the
event of malfunctions, check the power supply wiring. If the wiring is OK,
replace the fan.
•
Check
that there are no water leaks inside cabinet and on the
distribution line and fittings.
11. MAINTENANCE
10.2 Special maintenance
Special maintenance involves all those operations that are performed
on a one-off basis in the event of malfunctions or breakages of certain
components.
The following components are those susceptible to breakage:
•
solenoid valves
•
pressure reducer
•
pressure switches
•
pump motor
•
pump
•
electronic controller
•
fuses
•
nozzles
•
nozzle manifold
•
fans on the blower units
To replace these contact specialist and authorised personnel.
For the spare part numbers, see table “9.5 Spare parts”.
10.3 Pump maintenance
The pump is the most complex mechanical device inside the cabinet, as
well as the heart of the high pressure system. It therefore requires specific
regular maintenance, comprising at least three operations (described
below).
10.3.1 Oil change
Important:
after the first 50 hours of operation, the oil in the pump needs
to be changed (P/N 5024646AXX). Failure to change the oil after the first
50 hours may cause damage to the pump and reduce its working life.
The first oil supplied, in fact, will accumulate debris due to transport and
commissioning, and a longer operating time cannot be guaranteed.
In normal operating conditions, except for the first oil change oil after
50 hours, it is recommended the change the oil every 3000 operating
hours. Expiry of the 3000 operating hours is signalled by the electronic
controller via the “3000 hour maintenance” alarm on the display.
To change the oil, follow the sequence described below (with the unit off
and the water line closed):
1.
Remove the yellow cap on the top of the pump and unscrew the oil
drain plug attraction the bottom (steel hexagonal plug).
2.
Empty the oil into a suitable container. Close the plug.
3.
Dispose of the oil in accordance with local standards.
4.
Fill the pump body with SAE 15W40 mineral oil, up to the level
suggested by the circular marker on the side of the pump (the
required oil content is around 350 ml).
5.
Finally, close the yellow cap on the top of the pump.
10.3.2 Gasket and valve replacement
The gaskets and valves require replacement every each 3000 hours,
as signalled on the display by the “3000 hour maintenance” alarm.
Nonetheless, in specific conditions of stress replacement may be needed
earlier.
Carel recommends to check the pump operation every 1000 operating
hours (signalled by a warning). If the pump makes noise, or is not able to
reach the required operating pressure (70 bars), the gaskets and valves
may need to be replaced sooner.
Summary of Contents for humiFog direct
Page 2: ......
Page 4: ...4 ENG humiFog direct 0300073EN rel 1 0 31 03 2017...
Page 6: ...6 ENG humiFog direct 0300073EN rel 1 0 31 03 2017...
Page 43: ......