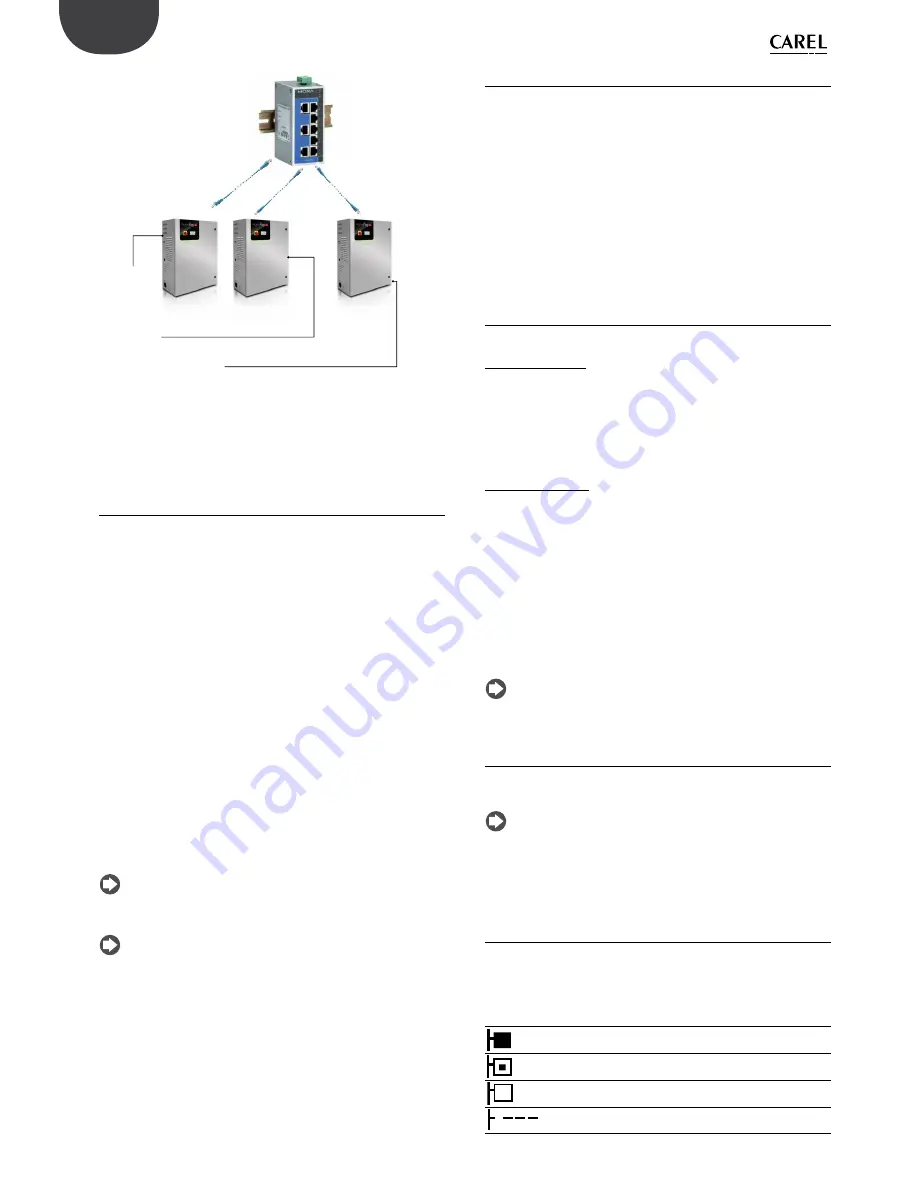
26
ENG
"humiFog direct" +0300073EN rel. 1.0 - 31.03.2017
Master
Slave
Slave
IP: 192.168.1.2
IP: 192.168.1.1
IP: 192.168.1.3
Fig. 7.d
Systems set up in this way will be able to cover the humidification
requirement. In this specific case, the Master will always be the unit
with the lowest IP address of those connected to the signal/probes. If
necessary, an additional humidifier (backup) can be installed to cover
request in the event of malfunctions on one of the units in the system.
7.4 Master/Slave system configuration
To configure the Master/Slave system, proceed as follows:
1.
Connect the probes or the external signal to the unit and complete the
configuration (control type, type of signal, maximum production …);
2.
Set the IP addresses of the individual units so that they belong to the same
subnetwork (subnet mask); the screen index for this configuration is Dg04
(D. Settings – g. Supervision). The IP address is set on the display on each
unit, assigning a different address to each unit in the same subnetwork.
If necessary, contact the local network administrator. Remember that the
default address for each unit is 192.168.0.1, and the default subnet mask
is 255.255.255.0. For further details see paragraph 8.1.1 “IP address and
network configuration”
3.
Connect the units making up the Master/Slave system to the local
Ethernet network via a switch. If using just two units, an RJ45 category 5
cable can be used, connected directly to the Ethernet ports on the two
c.pHC controllers.
4.
Configure the Master/Slave system by enabling the units one at a time
(this operation can be performed on the display on any of the units):
4.1 Display screen index Dd01 and then access configuration mode
by pressing “PRG”.
4.2 Enter the IP address for “Unit 1” and confirm by pressing “ENTER”.
4.3 Repeat the operations described above (4.1 and 4.2) for all the
other units in the Master/Slave system.
(The units will join the Master/Slave system (online) immediately
after being added to the network.)
Note:
the Master unit will always (automatically) be the one with
the lowest IP address out of the units connected to the probes or external
signal.
Note:
it may take a few seconds (max 10 s) for the Master to start
sending the production request to the Slave/Slaves. This is also true
when, automatically, the Master unit is changed (for example, in the
event of malfunctions).
7.4.1
Maximum Master/Slave system production
In the same way as for the individual unit configuration, for the Master/
Slave system the maximum capacity can also be set. To set the maximum
capacity, go to menu Dd03. The “Capacity” parameter identifies the
maximum production request for the Master/Slave system, and can
therefore be set by the user.
The “Maximum capacity” parameter (read-only), on the other hand,
indicates the sum of the sizes of each unit added to the system; this
value is therefore the maximum effectively available to the Master/Slave
system. Consequently, “Capacity” will always be ≤ “Maximum capacity”.
In any case, the maximum production can be defined for each individual
unit in the system by limiting production from its maximum according
to the size. In this case, “Maximum capacity” will be updated keeping in
consideration these reductions..
7.4.2
Unit production distribution logic in the
Master/Slave system
The activation logic of the units in the Master/Slave system can be set,
choosing between “Grouped” or “Balanced”, on screen Dd03.
Grouped distribution
•
the units are activated in series, one after the other, according to the
request.
Example:
M/S system comprising two 80 kg/h units, for a maximum total
capacity of 160 kg/h. While the request remains below 50% (80 kg/h)
only one unit will be activated (for example, Unit 1), as soon as the
request exceeds the 50%, the second unit will also be activated (in the
example, Unit 2).
Balanced distribution:
•
the units are activated in parallel at the same time, splitting the total
production request between the number of units in the M/S system.
Example:
M/S system comprising two 80 kg/h units, for a maximum
total capacity of 160 kg/h. If the request is 50%, both Unit 1 and Unit 2
will be activated at 50% of production (40 kg/h + 40 kg/h = 80 kg/h). If
the request is 90% (144 kg/h), both Unit 1 and Unit 2 will be activated
at 90% (72 kg/h + 72 kg/h = 144 kg/h).
For Grouped Distribution only, if the request does not require the use
of all the units, the automatic rotation function can ensure that the
individual units total the same number of operating hours. To enable
and configure the operating hours for unit rotation, set the “auto-rotation
time” parameter on screen Dd04.
Note:
if the “auto-rotation time” parameter is = 0, the auto-rotation
function is disabled.
7.4.3
Disconnect unit from the Master/Slave system
To remove a unit from the Master/Slave system, thus reducing the number
of units available in the system, use the “Disconnect unit” function on
screen Dd06. This can be done on any of the humidifiers in the system.
Note:
once the unit has been disconnected, this will no longer be
visible in the Master/Slave system, as its IP address will be removed from
the list. If a unit is disconnected erroneously, the system can be restored
on screen Dd01 (entering its IP). This must be done from the display on a
unit that is already connected to the system.
7.4.4
Display Master/Slave system
To display a summary of the Master/Slave system, go to screen Dd08.
The menu displays all the units (01, 02, …), the status of each unit and
current production as a percentage. The following table lists the Master/
Slave network unit status indications:
Symbol
Unit status in the Master/Slave system
Indicates the current unit being displayed (PGD or web server)
The unit is: online
The unit is: offline
Unit not configured and not included in the Master/Slave
system
Summary of Contents for humiFog direct
Page 2: ......
Page 4: ...4 ENG humiFog direct 0300073EN rel 1 0 31 03 2017...
Page 6: ...6 ENG humiFog direct 0300073EN rel 1 0 31 03 2017...
Page 43: ......