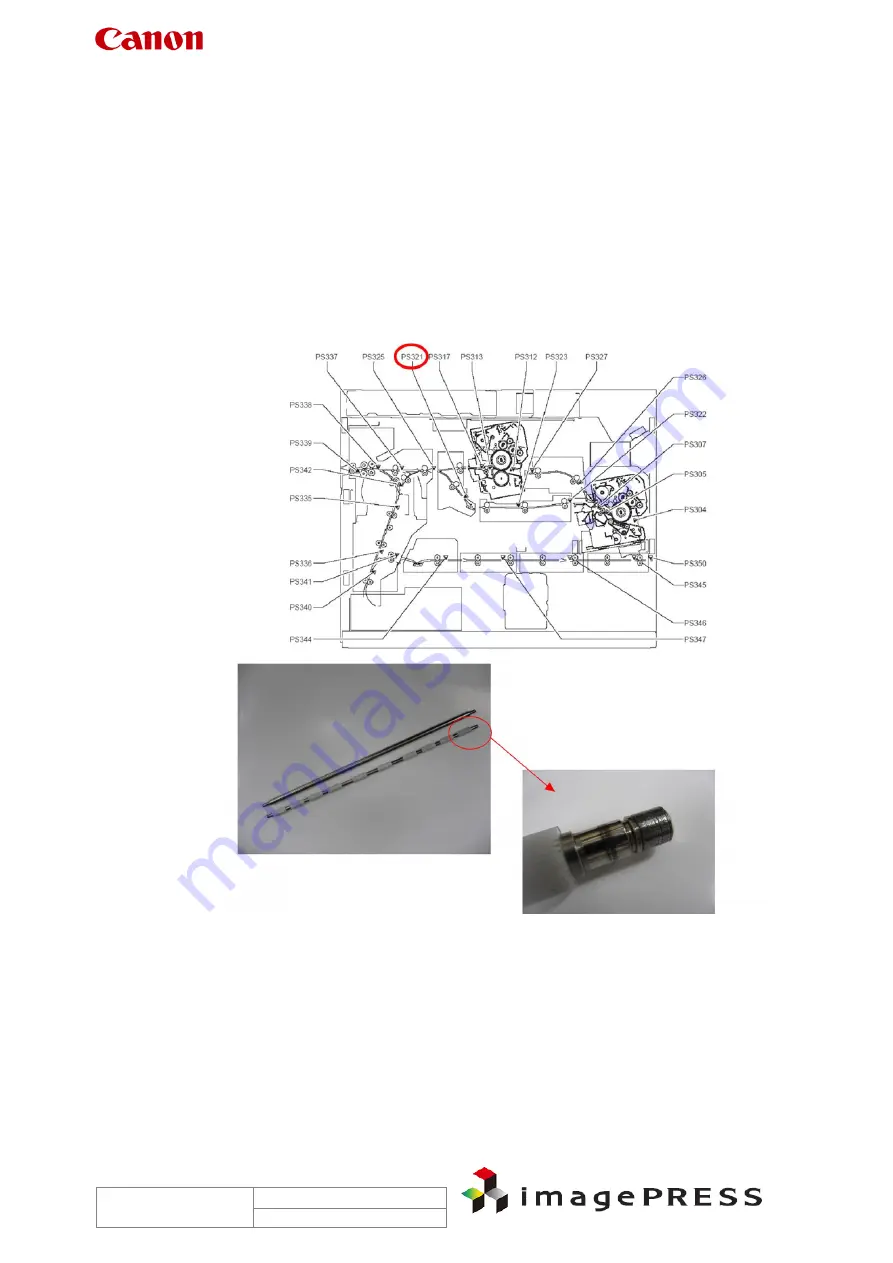
Trouble Shooting Information for C7000VP series
Page 95
Rev. 2.0
2010/09/17
4.2
012A JAM
Description
The shaft of the slave roller (FC7-1598) became chipped by friction with the bushing
(FS5-1592). An excessive amount of load was applied to the shaft and the roller became
unable to rotate. Accordingly, 012A jam (merger path lower sensor PS321 delay jam) was
generated.
Cause
The bushing, which is fixed onto the decurler grounding plate (FC7-1601), made a skew
contact with the shaft when it was fixed.
Field Remedy
Apply conducting grease on the bushing and mount the decurler earth plate ensuring that the
plate is straight.
This time, damage to the shaft occurred at the bypass decurler part, but a part of the same
construction is also used for duplexing decurler.
Summary of Contents for imagePRESS C7000VP Series
Page 17: ...Trouble Shooting Information for C7000VP series Page 17 Rev 2 0 2010 09 17 ...
Page 32: ...Trouble Shooting Information for C7000VP series Page 32 Rev 2 0 2010 09 17 ...
Page 33: ...Trouble Shooting Information for C7000VP series Page 33 Rev 2 0 2010 09 17 ...
Page 34: ...Trouble Shooting Information for C7000VP series Page 34 Rev 2 0 2010 09 17 ...
Page 35: ...Trouble Shooting Information for C7000VP series Page 35 Rev 2 0 2010 09 17 ...
Page 36: ...Trouble Shooting Information for C7000VP series Page 36 Rev 2 0 2010 09 17 ...
Page 37: ...Trouble Shooting Information for C7000VP series Page 37 Rev 2 0 2010 09 17 ...
Page 38: ...Trouble Shooting Information for C7000VP series Page 38 Rev 2 0 2010 09 17 ...
Page 39: ...Trouble Shooting Information for C7000VP series Page 39 Rev 2 0 2010 09 17 ...
Page 40: ...Trouble Shooting Information for C7000VP series Page 40 Rev 2 0 2010 09 17 ...
Page 41: ...Trouble Shooting Information for C7000VP series Page 41 Rev 2 0 2010 09 17 ...
Page 133: ...Trouble Shooting Information for C7000VP series Page 133 Rev 2 0 2010 09 17 ...
Page 134: ...Trouble Shooting Information for C7000VP series Page 134 Rev 2 0 2010 09 17 ...