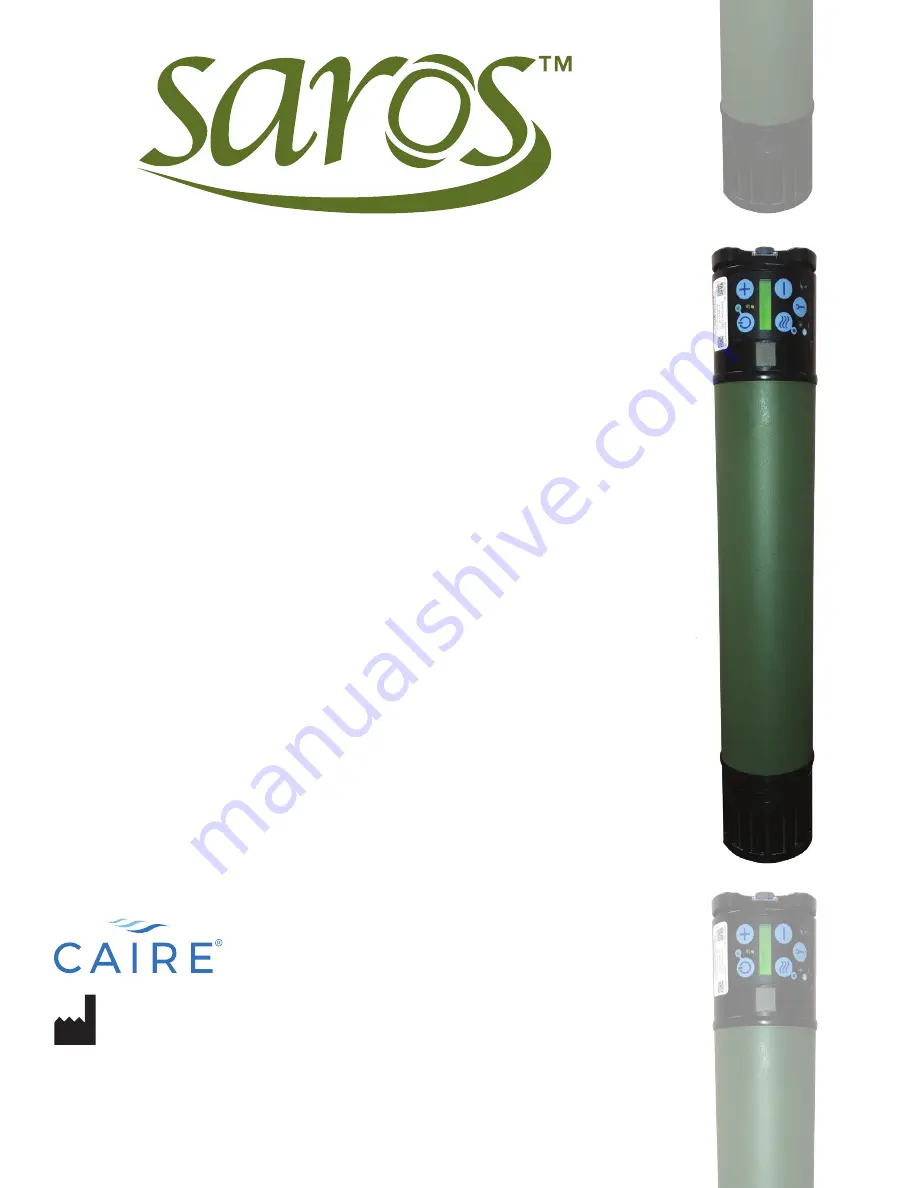
SERVICE MANUAL
MODEL 4000
Oxygen System
CAIRE Inc.
2200 Airport Industrial Dr., Ste 500
Ball Ground, GA 30107
www.caireinc.com
Copyright © 2020 CAIRE Inc.. CAIRE Inc. reserves the right to discontinue its products,
or change the prices, materials, equipment, quality, descriptions, specifications and/or
processes to its products at any time without prior notice and with no further obligation or
consequence. All rights not expressly stated herein are reserved by us, as applicable.
MN260 B
Summary of Contents for SAROS 3000
Page 56: ...Service Manual 56 MN260 B NOTES...