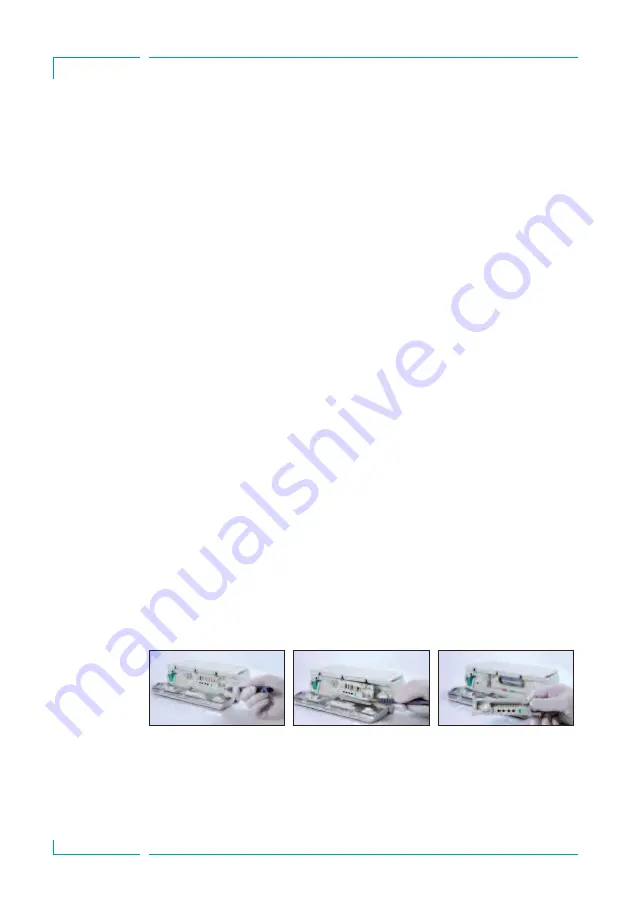
64
Technical Safety Check* / Service
The Technical Safety Check is recommended to be carried out every 2 years and
should be documented. Servicing work must be carried out exclusively by
trained personnel.
Check regularly
Check for cleanliness, completeness and damage. Use only according to
Instructions for Use. During an exchange interval of the disposable the pump
has to perform a self-test. Check the following items each time the pump is
switched on: self-check, audible alarm, process- and alarm control indication.
Disinfecting
Caution:
Before disinfecting the pump, always disconnect the pump
from the patient, switch off the device and disconnect from power and
other devices (e.g. staff call).
Clean all exposed surfaces using a clean, soft, lint-free cloth dampened with a
mild cleaning solution of warm, soapy water. Make sure to remove any visible
residue from all surfaces prior to disinfecting. The housing of Infusomat Space,
the slide guide and the inner tube guiding areas may be cleaned with EPA-regi-
stered hospital disinfectants containing 1- propanol or didecyl dimenthyl
ammonium chloride. Do not spray disinfectants directly on the pump, use a soft,
low lint cloth dampened but not saturated with product. After cleaning allow
device to dry for at least 20 minutes prior to use. The line guide element can be
removed using a pointed object (ballpoint pen) inserted in the lower right cor-
ner. The cover can then be immersed, to be cleaned, wipe “fingers” with a soft
cloth. Wipe magnifying- and displayglas on front of pump door only with a soft
cloth.
Note:
Keep instrument upright and do not allow any part of instrument to
become saturated with or submersed in fluid during cleaning operation.
Do not allow moisture or detergents to come into contact with the electrical
connections of the device (P2 or P3 connectors) or any device openings. To
reduce the likelihood of moisture ingress into the electrical connectors, the P2
WARRANTY / TRAINING / TSC* / SERVICE / DISINFECTING / DISPOSAL
Chapter 10