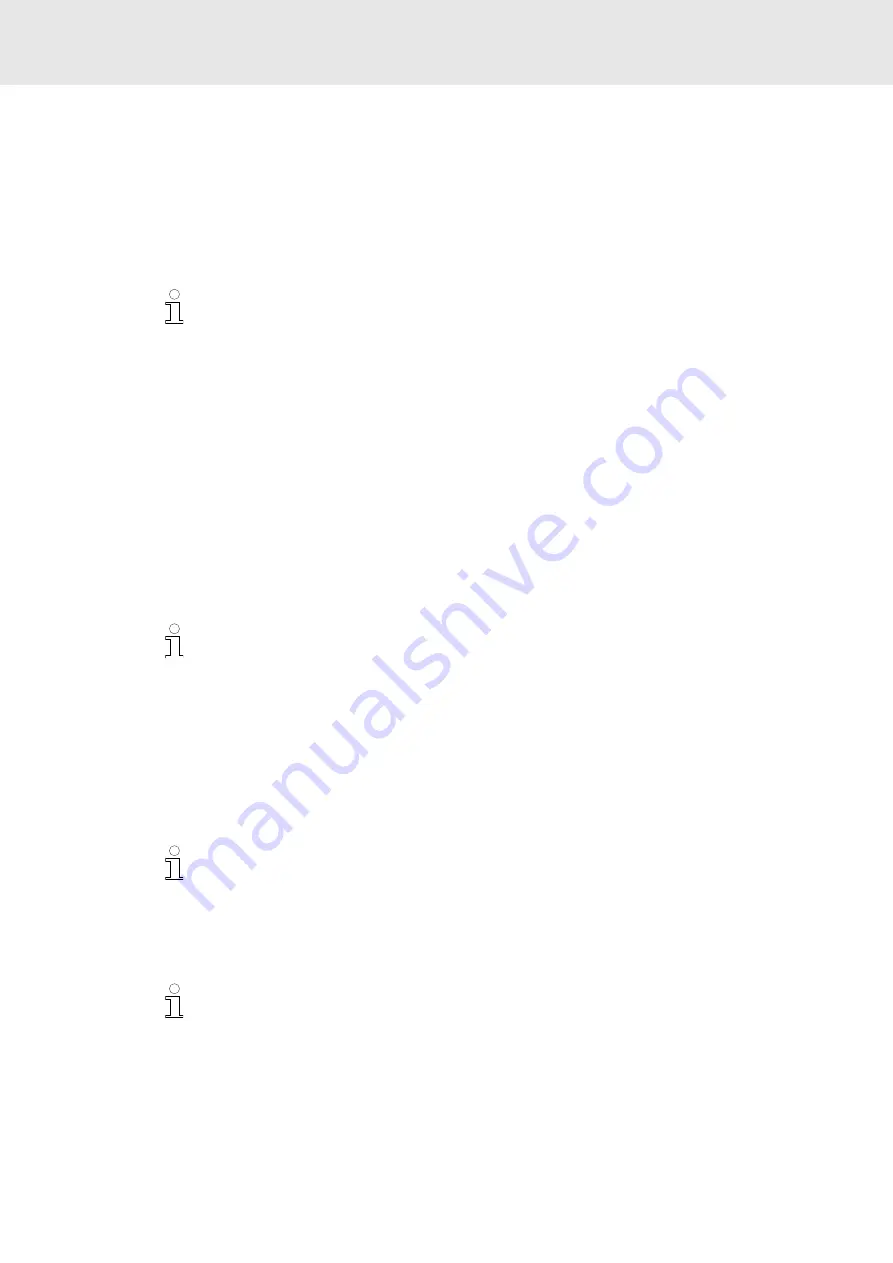
50 / 85
Servo-hydraulic actuator
Test sequence for validating the safety functions
Bosch Rexroth AG
RE62270-B, 01.21
●
Drive-internal command value provision and drive-internal enable
●
Drive-internal command value provision and external drive enable
●
External command value provision and external drive enable
●
Manual movement
8.4.3
Machine acceptance
A machine acceptance test from the drive's point of view is always required
when the safety technology of a servo-hydraulic actuator is parameterized for
the first time (initial commissioning) or modified.
Definition of “modified":
Safety technology parameters were changed or extended serial commissioning
was carried out (copy of a servo-hydraulic actuator as a template with a new
axis identifier and modified parameterization)
In the application of the safety functions of a servo-hydraulic actuator it is not
sufficient to carry out acceptances according to the above documentation. In
the following the deviations/extensions are described, which are relevant for
the machine acceptance and illustrate the specific interrelationships in a servo-
hydraulic actuator with safety functions.
Selection
For accepting the selection, the description according to the documentation
above may be applied without any restrictions.
Global monitoring functions
If global monitoring functions are activated, they can be accepted according to
the documentation mentioned above.
Please note that the monitoring functions refer to the externally connected,
safety-capable linear encoder, since it provides the feedback in the case of a
hazardous situation of the servo-hydraulic actuator.
The following checks must be carried out, if the monitoring functions are acti-
vated:
●
Check the safe maximum linear velocity
●
Check the linear velocity threshold for “safe standstill”
Monitoring in normal operation
If monitoring functions are activated during normal operation, they can be
accepted according to the documentation mentioned above.
Please note that the monitoring functions refer to the externally connected,
safety-capable linear encoder, since it provides the feedback in the case of a
hazardous situation of the servo-hydraulic actuator.
Special mode "EMERGENCY STOP" and “Safe standstill”
The special modes "EMERGENCY STOP" and “Safe standstill” can be accepted
according to the above documentation.
Please note that the monitoring functions refer to the externally connected,
safety-capable linear encoder, since it provides the feedback in the case of a
hazardous situation of the servo-hydraulic actuator.
Special mode “Safe motion”
If special “Safe motion” modes are configured, they can be accepted according
to the documentation mentioned above.
The following checks have to be carried out according to the configuration:
Summary of Contents for rexroth CytroForce-M
Page 1: ...Servo hydraulic actuator CytroForce M Operating Manual RE62270 B 01 21 ...
Page 10: ...10 85 Servo hydraulic actuator Representation of information Bosch Rexroth AG RE62270 B 01 21 ...
Page 20: ...20 85 Servo hydraulic actuator Bosch Rexroth AG RE62270 B 01 21 ...
Page 36: ...36 85 Servo hydraulic actuator Storage Bosch Rexroth AG RE62270 B 01 21 ...
Page 60: ...60 85 Servo hydraulic actuator Field data acquisition FDA Bosch Rexroth AG RE62270 B 01 21 ...
Page 66: ...66 85 Servo hydraulic actuator Replacement of components Bosch Rexroth AG RE62270 B 01 21 ...
Page 70: ...70 85 Servo hydraulic actuator Bosch Rexroth AG RE62270 B 01 21 ...
Page 72: ...72 85 Servo hydraulic actuator Bosch Rexroth AG RE62270 B 01 21 ...
Page 76: ...76 85 Servo hydraulic actuator Bosch Rexroth AG RE62270 B 01 21 ...
Page 82: ...82 85 Servo hydraulic actuator Declaration of incorporation Bosch Rexroth AG RE62270 B 01 21 ...
Page 84: ......