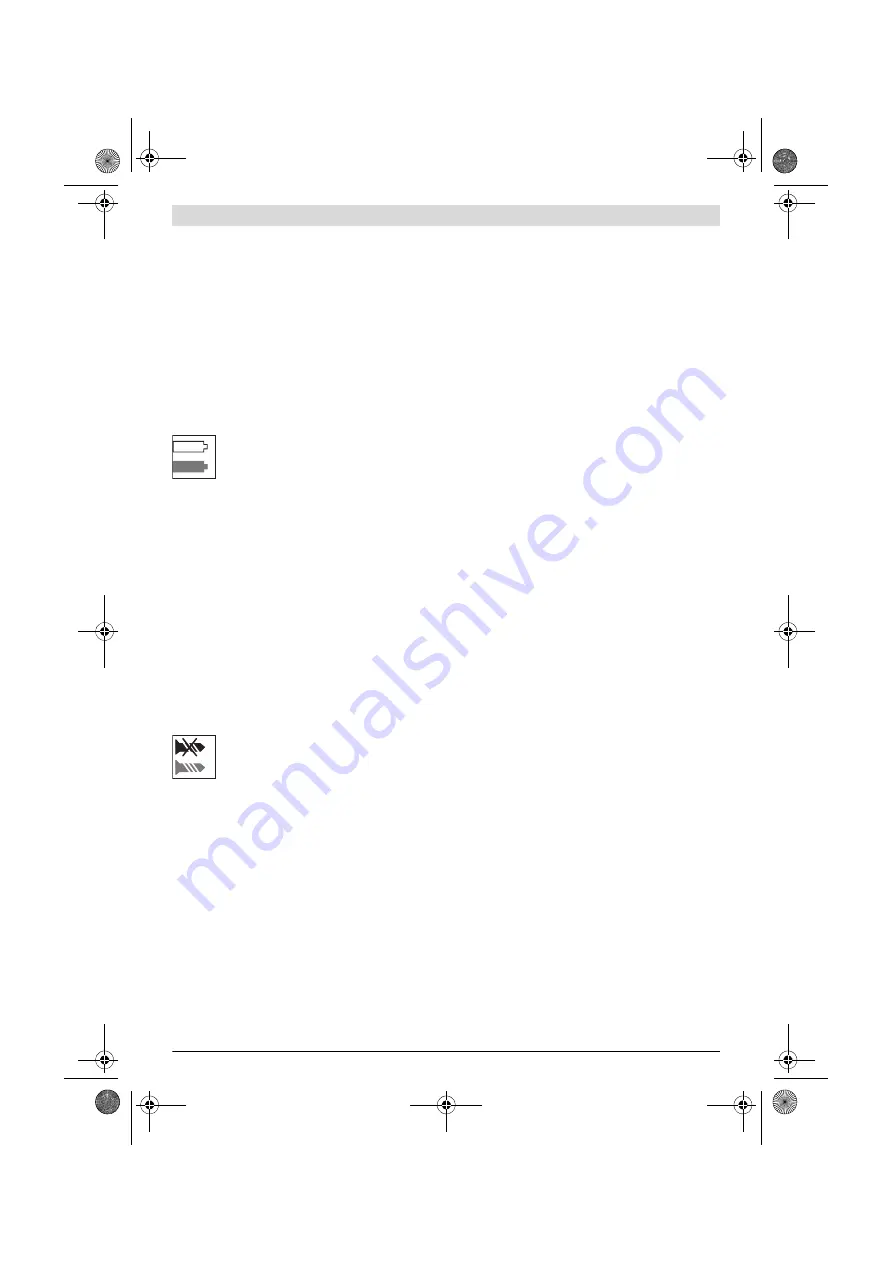
26
| English
3 609 929 C62 | (9.12.13)
Bosch Power Tools
For example, if you are using several EXACT tools set to a
torque of 4.5 Nm, you can use the red rings to marque their
set values. If you are using more EXACT tools in another part
of the assembly process where the torque is set to 7.5 Nm,
you can use another marking ring (such as black, blue, green
or yellow) to mark the torque range of these units. The differ-
ent marking rings are only intended as a quick reference for
production personnel to easily indentify which tool is set for a
given torque range.
Press off the marking ring
17
with a thin screwdriver blade, a
knife, or similar.
Always use the power tool with a marking ring to insure that
the housing body is sealed from dust and dirt.
LED Indicators
Battery Condition Indicator
If the charging of the battery
11
is necessary, the
LED indicator
10
blinks green and an acoustical
signal sounds. Only 6 –8 screwing operations
may be possible.
When the LED indicator lights up red, the capacity is no longer
sufficient for a new screw connection or the power tool has
been subject to overload. The power tool can not be switched
on anymore. The start lock remains active until the battery
pack is removed from the power tool and a charged battery
pack is inserted again.
When working with a voltage adapter, the red LED indicator
10
indicates an overload.
When the LED indicator
10
blinks red, the power tool is over-
heated and can no longer be switched on. Wait until the blink-
ing automatically stops after a short period before continuing
to work again with the power tool.
A considerably shortened operating time of the power tool af-
ter each charging indicates that the battery must be replaced
soon. Dispose of the used battery in accordance with the le-
gal/country-specific regulations.
Screwing Fastener Indicator
When the preset torque is reached, the shut off
coupling responds. The LED indicator
9
lights
green.
If the preset torque is not reached, the LED indicator
9
lights
red and an acoustical signal sounds. The screwing fastener
must be performed again.
Repeat Protection
When the shut-off coupling responds for a screwing fastener,
the motor shuts off. Switching on again is possible only after
a 0.7 second delay. In this manner, an unintentional re-tight-
ening of an already seated screw is avoided.
Adjusting the Angled Drive Head
The angled drive head
3
can be adjusted to a total of eight po-
sitions.
Hold the power tool with the open-end spanner
6
by the span-
ner flats
5
of the angled head flange.
Never clamp the tool by the housing shells!
Loosen the sleeve nut with the open-end spanner
4
by the
spanner flats
19
. Adjust the angled drive head
3
in 45° steps
to the desired position and retighten the sleeve nut again with
the open-end spanner
4
by the spanner flats
19
.
Hold the angled head flange with the open-end spanner
6
to
prevent turning.
Please observe the information of your bought-out flat drive
or inquire at your specialist shop.
Adjusting and Removing the Angled Drive Head
(see figure J)
The angled drive head
3
with tool bit holder
2
can be continu-
ously adjusted around 360°.
Loosen the lock nut
20
by inserting an appropriate tool into an
opening of the lock nut and turning the lock nut in the direc-
tion of the arrow
a
(left thread).
Turn the angled drive head
3
in arrow direction
b
until the de-
sired work angle is reached, but not more than once by 360°.
Fix the angled drive head
3
in this position by turning the lock
nut
20
in the direction of the arrow
c
against the angled drive
head. Tighten the lock nut
20
with a tightening torque of max.
50 Nm again.
The angled drive head
3
can also be removed completely,
e. g. when it is required to replace the marking ring
17
by one
with another colour or to adjust the worklight. Adjust the
worklight to the desired position first (see “Adjusting the LED
Worklight”, page 26) before adjusting the angled drive head.
Loosen the lock nut
20
by inserting an appropriate tool into an
opening of the lock nut and turning the lock nut in the direc-
tion of the arrow
a
(left thread).
Unscrew the angled drive head
3
in arrow direction
b
until it
can be removed.
Unscrew the lock nut
20
from the motor housing
33
in arrow
direction
a
.
Now, the marking ring can be exchanged or the worklight can
be adjusted.
– Turn the lock nut
20
in arrow direction
c
onto the motor
housing
33
and screw on the angled screw head again
turning in arrow direction
b
.
– Lock the angle nutrunner head by screwing the lock nut
20
in arrow direction
c
.
– Retighten lock nut
20
again with a tightening torque of ap-
prox. 50 Nm.
Adjusting the LED Worklight (see figure K)
For these industrial cordless angle wrenches, the angled
screw head must be removed first, see “Adjusting and Remov-
ing the Angled Drive Head”, page 26.
Adjust the worklight as described below.
ANGLE EXACT
2
|
3
|
6
|
7
|
7–900
|
8
|
10–650
|
14–420
|
15
|
17
|
23
|
25–200
|
30
|
30–300
ANGLE EXACT
14CF
|
22CF
|
29CF
ANGLE EXACT
25–250
|
30–380
|
40–280
|
50–210
|
60–170
ANGLE EXACT
25–250
|
30–380
|
40–280
|
50–210
|
60–170
OBJ_BUCH-412-002.book Page 26 Monday, December 9, 2013 5:34 PM