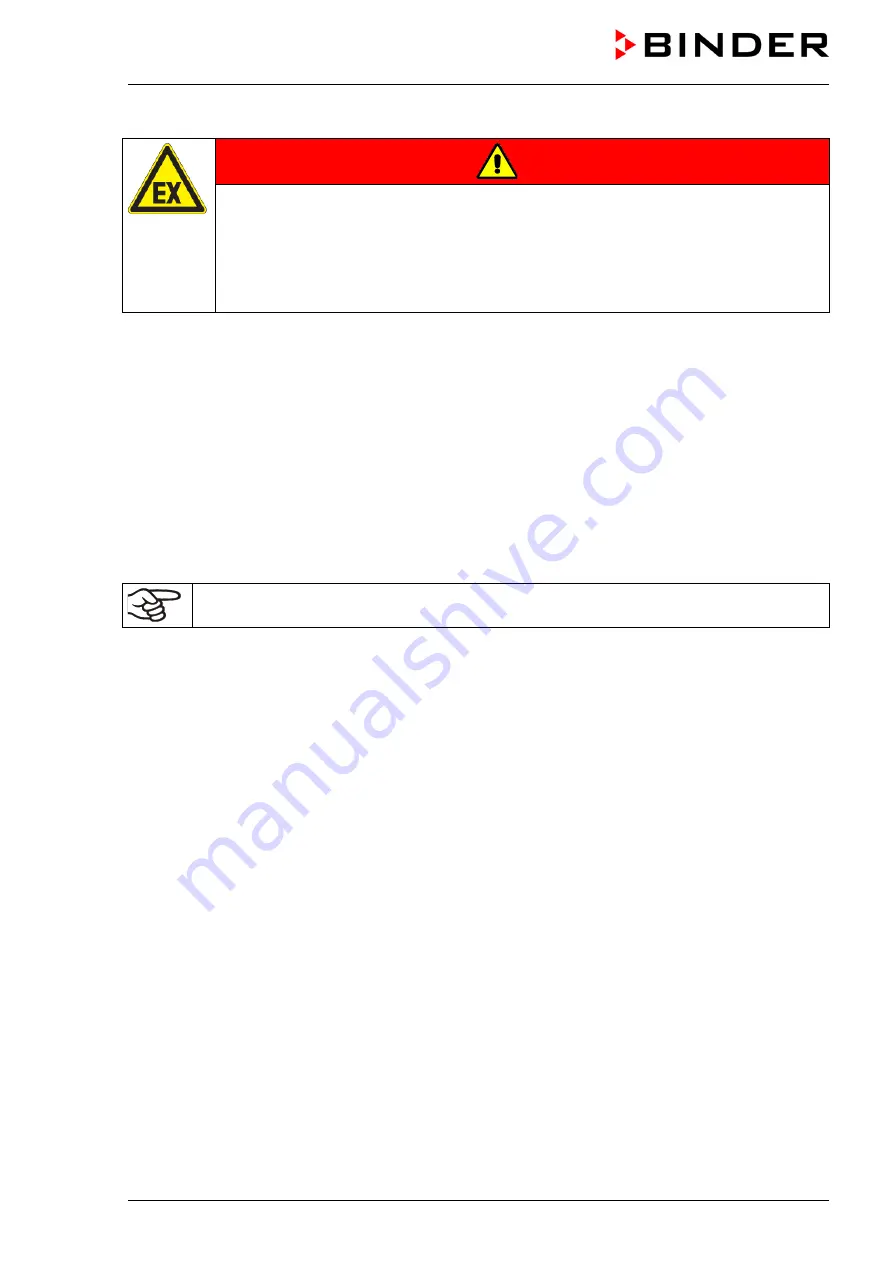
VDL (E3.1) 06/2020
Page 97/206
The chamber is not to be installed and operated in potentially explosive areas.
DANGER
Explosion hazard due to explosive mixtures in the vicinity of the equipment.
Serious injury or death from burns and / or explosion pressure.
∅
Ensure that NO solvents or explosive solvent-air mixtures are located in the area
around the chamber.
Disconnect the chamber from the power immediately if there is explosive atmosphere in
the area around the chamber outside the indicated loading area.
9.9
Evacuation
Starting situation: The vacuum pump / vacuum system is connected and ready for operation.
Preparation:
•
Make sure that the “Manual ventilation” plug (7) for emergency ventilationin case of a power failure,
which is located on the chamber rear, is closed
•
Make sure that the pressure control is activated.
•
Turn on the vacuum pump. The pump shall continue running during the entire drying procedure.
•
Set the desired pressure set-point on the controller (chap. 10).
•
Monitor the internal pressure on the controller display
As long as there is a vacuum, never try to open the oven by force.
9.10
Breaking the vacuum (flooding)
9.10.1 Ventilation after completing the drying procedure (flooding with ambient air or
inert gas)
The duration of the drying procedure can be determined via the pressure display on the controller. When
the decreasing pressure reaches the set-point value, the drying process is completed. If the drying moni-
toring (chap. 11.6) is activated, a corresponding message is displayed.
To break the vacuum (ventilation) after completing the drying procedure, set the desired pressure set-
point to atmospheric pressure (chap. 10). The ventilation valve opens, and ambient air or inert gas flow
into the inner chamber.
Regularly the universal connection for inert gas / ambient air “GAS/AIR” (4) is used for ventilation.
Chambers can be equipped as an option with an additional universal connection for inert gas / ambient air
“GAS/AIR2” (5), which can be used alternatively. To do this, the controller function “GAS/AIR 2” serves to
close the valve of the standard connection “GAS/AIR” (4). Then the valve of the optional connection
“GAS/AIR 2” (5) is used for ventilation (chap. 11.2). This allows convenient switching when both connec-
tions are used differently (e.g., for inert gas and ambient air).
Ambient air is sucked in through the universal connection for inert gas / ambient air (4) or (5). The ambi-
ent air is introduced into the lower part of the rear panel of the inner chamber and is evenly distributed in
the inner chamber. This supply of ambient air by under-flooding prevents turbulence of pulverized drying
material.
Following ventilation, remove the loading material.
If no further drying process is to be carried out, switch the chamber to standby mode on the controller or
pull the mains plug to switch off the chamber completely.
Summary of Contents for vdl 115
Page 192: ...VDL E3 1 06 2020 Page 192 206 28 6 Dimensions 28 6 1 VDL 23 Dimensions in mm ...
Page 193: ...VDL E3 1 06 2020 Page 193 206 28 6 2 VDL 56 Dimensions in mm ...
Page 194: ...VDL E3 1 06 2020 Page 194 206 28 6 3 VDL 115 Dimensions in mm ...
Page 198: ...VDL E3 1 06 2020 Page 198 206 ...
Page 199: ...VDL E3 1 06 2020 Page 199 206 ...
Page 200: ...VDL E3 1 06 2020 Page 200 206 31 Product registration ...
Page 207: ......