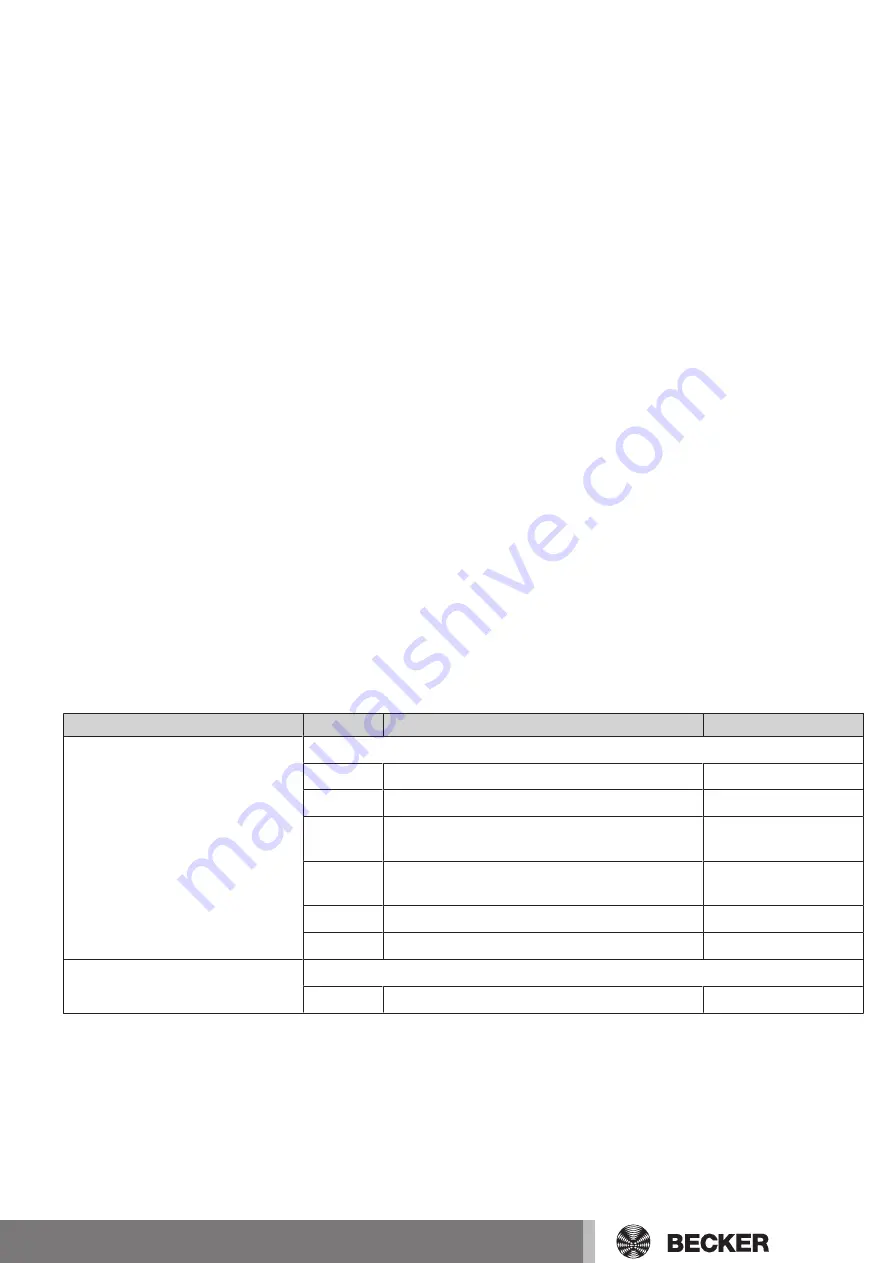
Wicket door switch and slack rope switch
A wicket door switch with redundant contacts can be connected to terminal SE2. Two slack rope switches can be connected in
series to the wicket door switch. The signal transmitters must meet Performance Level “c” in combination with the control unit. If
no wicket door switch is used, an appropriate substitute resistor (2k Ohm) must be switched on. If a slack rope switch without res-
istance is used, an appropriate substitute resistor (3k Ohm) must be switched on. The door is stopped when the wicket door is
opened or when the slack rope switch is triggered. The resistor between terminals SE2 and 12V must be removed at installation.
All switches functioning and not actuated: 4.62 kΩ to 5.75 kΩ
Short-circuit: 0 Ω to 4.62 kΩ
Error in the wicket door switch: 5.75 kΩ to 15.9 kΩ
Safety circuit open: larger than 15.9 kΩ
Spring break safety device
A spring break safety device can be connected to terminals NA2. Activation causes the door to be stopped. For the duration of ac-
tivation, all further door movement is prevented. The spring break safety device must be intrinsically safe and switches must be
forcibly actuated. The cable must be laid with short-circuit protection.
Anti-unrolling device
An anti-unrolling device can be connected to terminals NA2. Activation causes the door to be stopped. For the duration of activa-
tion, all further door movement is prevented. The anti-unrolling device must be intrinsically safe and switches must be forcibly ac-
tuated. The cable must be laid with short-circuit protection.
SE1 – safety input 1
The safety device SE1 only works in the CLOSE direction with reversal in the OPEN direction.
SE2 – safety input 2
The input’s operating direction can be set in P.4F4.
P.4F4: 0: CLOSE – with reversal
P.4F4: 1: OPEN – with reversal
P.4F4: 2: OPEN and CLOSE, stop function, dead-man travel possible
P.4F4: 3: OPEN and CLOSE, stop function, no travel possible
Safety input
To adapt the control unit to the respective safety edge, the parameters P.4E0 and P.4F0 must be set according to the following
table.
P.4E0 – safety input SE1 (effective in the CLOSE direction)
Function
Profile
Description
Testing
1.XX
Electric safety edge 1
The door stops and reverses when this is activated during travel in the CLOSE direction.
1.00
8k2 ohm
Internal testing
1.01
1k2 ohm
Internal testing
1.02
8k2 ohm, DW edge
CLOSE limit position,
after pre-limit-switch
1.03
1k2 ohm, DW edge
CLOSE limit position,
after pre-limit-switch
1.04
Safety device with PNP output
External testing
1.05
Safety device with NPN output
External testing
2.XX
Optoelectronic safety edge OSE
The door stops and reverses when this is activated during travel in the CLOSE direction.
2.00
Safety in CLOSE
19