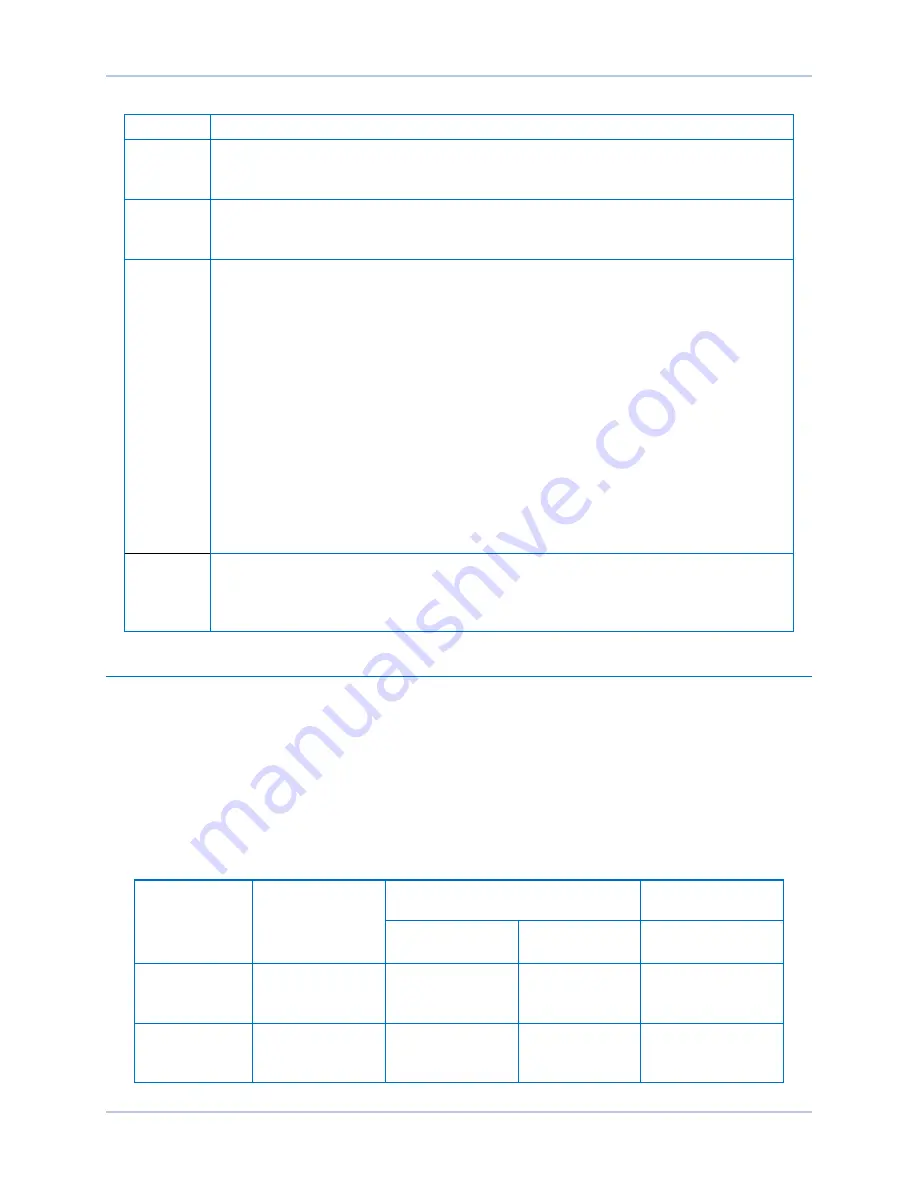
9440300990 Rev J
117
DECS-250
Terminals and Connectors
Table 5. Right Side Terminal and Connector Descriptions
Locator
Description
K
A second DECS-250 connects through a standard serial cable to this DB-9 connector
for the purpose of setpoint tracking. Setpoint tracking between a DECS-250 and
DECS-200 is possible.
L
This DB-9 connector is provided for PROFIBUS communication (style xxxxxxP) and
the future implementation of other communication protocols. Contact Basler Electric
for protocol availability.
M
Three terminal sets within this block include two CAN communication ports and an
IRIG input. The IRIG terminals connect to an IRIG source for synchronization of
DECS-250 timekeeping with the IRIG source. Both CAN ports are SAE J1939
compliant. CAN 1 is used to connect add-on modules such as the Basler Electric
CEM-2020 and AEM-2020. CAN 2 is used to communicate with a genset engine
controller.
The terminal numbers (shown below) are located on the mating side of the
connector.
•
96 - CAN 1 High
•
97 - CAN 1 Low
•
98 - CAN 1 Shield
•
99 - CAN 2 High
•
100 - CAN 2 Low
•
101 - CAN 2 Shield
•
102 - IRIG +
•
103 - IRIG
–
N
This optional Ethernet communication port uses the Modbus TCP protocol to provide
remote metering, annunciation, and control. A copper (100Base-T) port (style
xxxxx1x) uses a standard RJ45 jack while a fiber optic (100Base-FX) port (style
xxxxx2x) uses two fiber optic connectors (not shown).
Terminal Types
Spring terminals are supplied on DECS-250 controllers with a style number of xxxSxxx. These removable
connectors secure each wire with a spring-loaded contact.
Compression terminals are supplied for the operating power terminals (locator A), field power output
terminals (locator B), and current sensing terminals (locator C) when a style number of xxxCxxx is
specified. The remaining connectors use spring terminals.
Table 6 lists the acceptable wire sizes, strip lengths, and screw torques (compression terminals only) for
each terminal block. The locator letters used in Table 6 correspond to the locator letters shown in Figure
106 and Figure 107.
Table 6. Connector Wiring Specifications
Terminal
Block
Maximum
Wire Size
Compression Terminals
Spring Terminals
Strip Length
Maximum
Screw Torque
Strip Length
A, B, C
10 AWG
10 mm
2
(solid)
6 mm
2
(stranded)
0.4 in (10 mm)
6.64 in-lb
(0.75 N
•
m)
0.6 in (15 mm)
D, E, F, G, H,
I, J
12 AWG
2.5 mm
2
(solid
and stranded)
N/A
N/A
0.4 in (10 mm)
Summary of Contents for DECS-250
Page 2: ......
Page 6: ...iv 9440300990 Rev J Revision History DECS 250 ...
Page 16: ...xiv 9440300990 Rev J Contents DECS 250 ...
Page 20: ...4 9440300990 Rev J Introduction DECS 250 ...
Page 28: ...12 9440300990 Rev J Power Stage DECS 250 ...
Page 32: ...16 9440300990 Rev J Voltage and Current Sensing DECS 250 ...
Page 40: ...24 9440300990 Rev J Synchronizer DECS 250 ...
Page 52: ...36 9440300990 Rev J Auxiliary Control DECS 250 ...
Page 56: ...40 9440300990 Rev J Contact Inputs and Outputs DECS 250 ...
Page 84: ...68 9440300990 Rev J Limiters DECS 250 ...
Page 114: ...98 9440300990 Rev J Power System Stabilizer DECS 250 Figure 96 PSS Parameter Settings ...
Page 124: ...108 9440300990 Rev J Stability Tuning DECS 250 ...
Page 126: ...110 9440300990 Rev J Mounting DECS 250 Figure 103 Overall and Projection Mounting Dimensions ...
Page 127: ...9440300990 Rev J 111 DECS 250 Mounting Figure 104 DECS 250 Escutcheon Plate Dimensions ...
Page 198: ...182 9440300990 Rev J Timekeeping DECS 250 ...
Page 210: ...194 9440300990 Rev J CAN Communication DECS 250 ...
Page 304: ...288 9440300990 Rev J Maintenance DECS 250 ...
Page 316: ...300 9440300990 Rev J Specifications DECS 250 ...
Page 334: ...318 9440300990 Rev J Analog Expansion Module DECS 250 ...
Page 351: ......