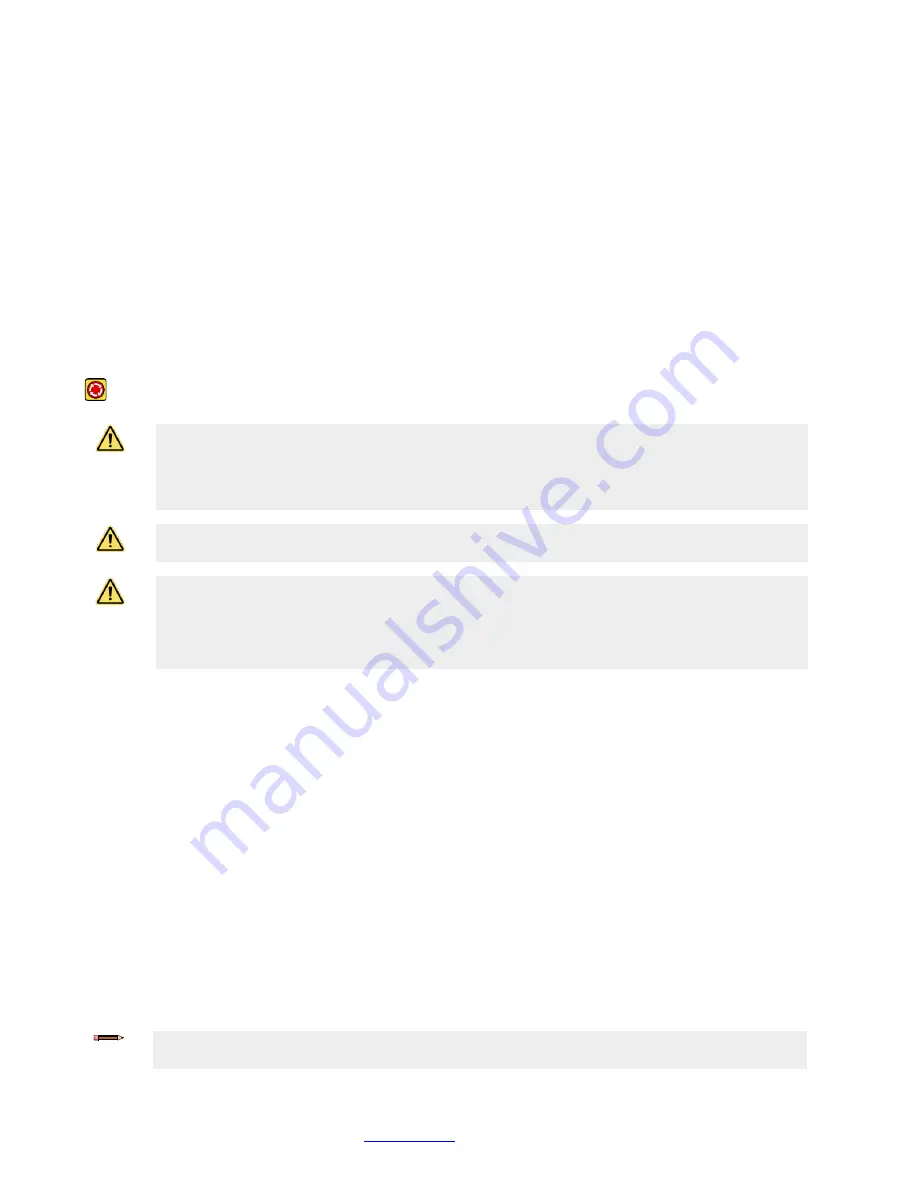
Programmable Safety Controller SCR P
www.bernstein.eu
- Tel: + 49 571 793 0
23
again (concurrency fault).
The 3 Terminal circuit detects a short to other power sources whether the contacts are open or closed.
3. Circuit meets up to ISO 13849-1 Category 4 if input devices are safety rated and provide internal monitor of the PNP
outputs to detect a) shorts across channels and b) shorts to other power sources.
4. Circuit meets up to ISO 13849-1 Category 4 if input devices are safety rated (see
Tip: INx & IOx input
terminal
s above). These circuits can detect both shorts to other power sources and shorts between channels.
6.4.1 Safety Circuit Integrity Levels
The application requirements for safeguarding devices vary for the level of control reliability or safety category per ISO
13849-1. While BERNSTEIN always recommends the highest level of safety in any application, the user is responsible to
safely install, operate, and maintain each safety system and comply with all relevant laws and regulations.
The safety performance (integrity) must reduce the risk from identified hazards as determined by the machine’s risk
assessment. See
Safety Circuit Integrity and ISO 13849-1 Safety Circuit Principles
on p. 19 for guidance if the requirements
as described by ISO 13849-1 need to be implemented.
6.4.2 Emergency Stop Push Buttons
The Safety Controller safety inputs may be used to monitor Emergency Stop (E-stop) push buttons.
In addition to the requirements stated in this section, the design and installation of the Emergency Stop device must comply
with ANSI NFPA 79 or ISO 13850. The stop function must be either a functional stop Category 0 or a Category 1 (see ANSI
NFPA79).
Emergency Stop Push Button Requirements
E-stop switch must provide one or two contacts for safety which are closed when the switch is armed. When activated, the
E-stop switch must open all its safety-rated contacts and must require a deliberate action (such as twisting, pulling, or
unlocking) to return to the closed-contact, armed position. The switch must be a positive-opening (or direct-opening) type,
as described by IEC 60947-5-1. A mechanical force applied to such a button (or switch) is transmitted directly to the
contacts, forcing them to open. This ensures that the switch contacts open whenever the switch is activated.
Standards ANSI NFPA 79, ANSI B11.19, IEC/EN 60204-1, and ISO 13850 specify additional Emergency Stop switch device
requirements, including the following:
• Emergency Stop push buttons must be located at each operator control station and at other operating stations
where emergency shutdown is required
• Stop and Emergency Stop push buttons must be continuously operable and readily accessible from all control and
operating stations where located.
Do not mute or bypass any E-stop button
• Actuators of Emergency Stop devices must be colored red. The background immediately around the device
actuator must be colored yellow. The actuator of a push-button-operated device must be of the palm or mushroom-
head type
• The Emergency Stop actuator must be a self-latching type
WARNING:
•
Do not mute or bypass any emergency stop device
• Muting or bypassing the safety outputs renders the emergency stop function ineffective.
• ANSI B11.19, ANSI NFPA79 and IEC/EN 60204-1 require that the emergency stop function
remain active at all times.
WARNING:
The Safety Controller Emergency Stop configuration prevents muting or bypassing of the E-
stop input(s). However, the user still must ensure that the E-stop device remains active at all times.
WARNING: Reset Routine Required
U.S. and international standards require that a reset routine be performed after clearing the cause of a
stop condition (for example, arming an E-stop button, closing an interlocked guard, etc.).
Allowing the
machine to restart without actuating the normal start command/device can create an unsafe condition
which could result in serious injury or death.
Note:
Some applications may have additional requirements; the user is responsible to comply with all
relevant regulations.