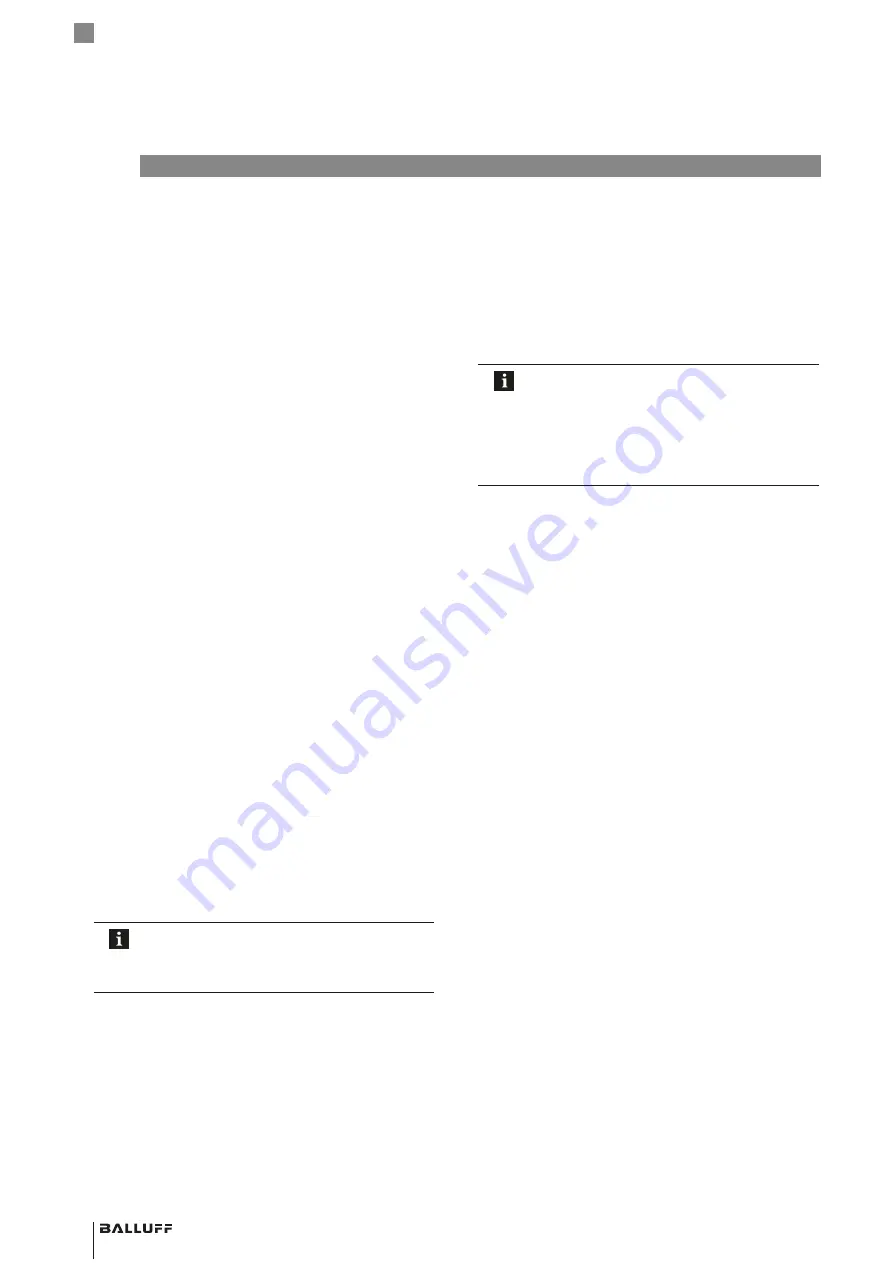
6.1
Basic knowledge about IO-Link
General
IO-Link integrates conventional and intelligent sensors and
actuators in automation systems and is intended as a
communication standard below classic field buses. Field-
bus-independent transfer uses communication systems
that are already available (field buses or Ethernet-based
systems).
IO-Link devices, such as sensors and actuators, are
connected to the controlling system using a point-to-point
connection via a gateway, the IO-Link master. The IO-Link
devices are connected using commercially available
unshielded standard sensor cables.
Communication is based on a standard UART protocol
with a 24-V pulse modulation in half-duplex operation. This
allows classic three-conductor physics.
Protocol
With IO-Link communication, permanently defined frames
are cyclically exchanged between the IO-Link master and
the IO-Link device. In this protocol, both process and
required data, such as parameters or diagnostic data, is
transferred. The size and the type of the frame and the
cycle time used result from the combination of master and
device features (see Communication parameters on
Cycle time
The cycle time used (master cycle time) results from the
minimum possible cycle time of the IO-Link device
(min cycle time) and the minimum possible cycle time of
the IO-Link master. When selecting the IO-Link master,
please note that the larger value determines the cycle time
used.
Protocol version 1.0 / 1.1
In protocol version 1.0, process data larger than 2 bytes
was transferred spread over multiple cycles.
From protocol version 1.1, all available process data is
transferred in one frame. Thus, the cycle time (master cycle
time) is identical to the process data cycle.
Operating the IO-Link device on an IO-Link
master with protocol version 1.0 results in
longer transfer times (process data cycle ~
amount of process data x master cycle time).
Parameter management
A parameter manager that enables device parameters to
be saved on the IO-Link master is defined in protocol
version 1.1. When exchanging an IO-Link device, the
parameter data of the previously installed IO-Link device
can be taken over. The operation of this parameter
manager is dependent on the IO-Link master and is
explained in the corresponding description.
The following parameters are stored in the BIP
(parameter management):
– Access Codes
– Application Specific Tag
– Output Inversion byte
Switching points are not stored because
sensors are not 100% interchangeable.
Device functions and master gateway
The functions of the position measuring system are
described in detail in sections 6.3 to 6.6. How process and
parameter data is implemented via the master gateway
can be found in the instructions for the IO-Link master.
6
IO-Link interface
10
english
BIP LD2-T017-01-EP _ _ / EP _ _ -S4
Inductive Positioning System
Summary of Contents for BIP LD2-T017-01-EP-S4 Series
Page 2: ...www balluff com...
Page 3: ...BIP LD2 T017 01 EP_ _ BIP LD2 T017 01 EP_ _ S4 Betriebsanleitung deutsch...
Page 4: ...www balluff com...
Page 32: ......
Page 33: ...BIP LD2 T017 01 EP_ _ BIP LD2 T017 01 EP_ _ S4 User s Guide english...
Page 34: ...www balluff com...
Page 62: ......
Page 63: ...BIP LD2 T017 01 EP_ _ BIP LD2 T017 01 EP_ _ S4 Notice d utilisation fran ais...
Page 64: ...www balluff com...
Page 92: ......
Page 93: ...BIP LD2 T017 01 EP_ _ BIP LD2 T017 01 EP_ _ S4 Manuale d uso italiano...
Page 94: ...www balluff com...
Page 122: ......
Page 123: ...BIP LD2 T017 01 EP_ _ BIP LD2 T017 01 EP_ _ S4 Manual de instrucciones espa ol...
Page 124: ...www balluff com...
Page 152: ......
Page 153: ...BIP LD2 T017 01 EP_ _ BIP LD2 T017 01 EP_ _ S4...
Page 154: ...www balluff com...
Page 161: ...5 1 BIP 1 2 3 BIP BIP 5 2 BIP BIP 5 www balluff com 9 BIP LD2 T017 01 EP_ _ EP_ _ S4...
Page 182: ......
Page 183: ...BIP LD2 T017 01 EP_ _ BIP LD2 T017 01 EP_ _ S4...
Page 184: ...www balluff com...
Page 191: ...5 1 BIP 1 2 3 BIP BIP 5 2 BIP BIP 5 www balluff com 9 BIP LD2 T017 01 EP_ _ EP_ _ S4...