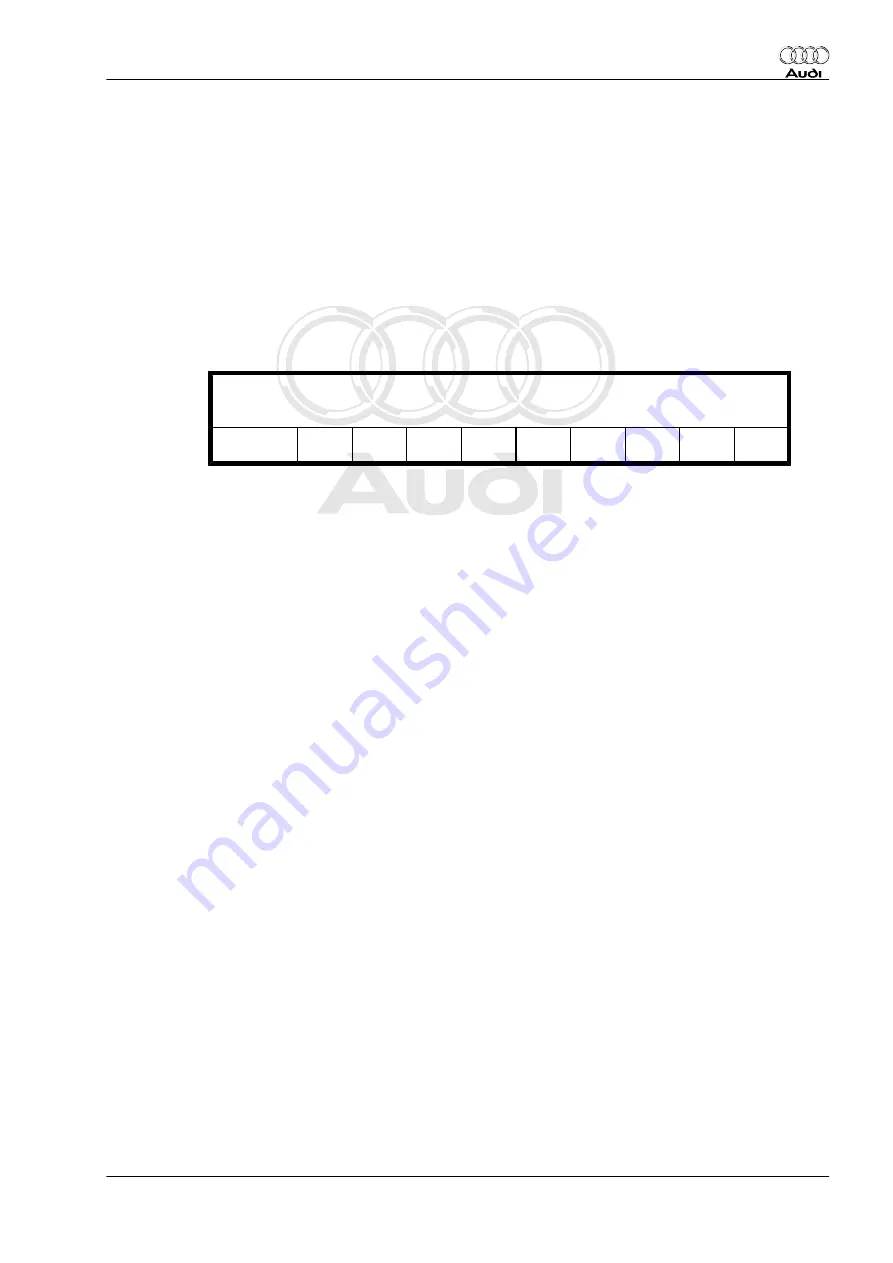
Protected by copyright. Copying for private or commercial purposes, in part or in whole, is not
permitted unless authorised by AUDI AG. AUDI AG does not guarantee or accept any liability
with respect to the correctness of information in this document. Copyright by AUDI AG.
Workshop Manual
Audi A8 2003 ➤
10-cylinder direct petrol injection engine (5.2 ltr. 4-
valve), mechanics
Engine ID
BSM
Edition 10.2013
Service
Service Department. Technical Information