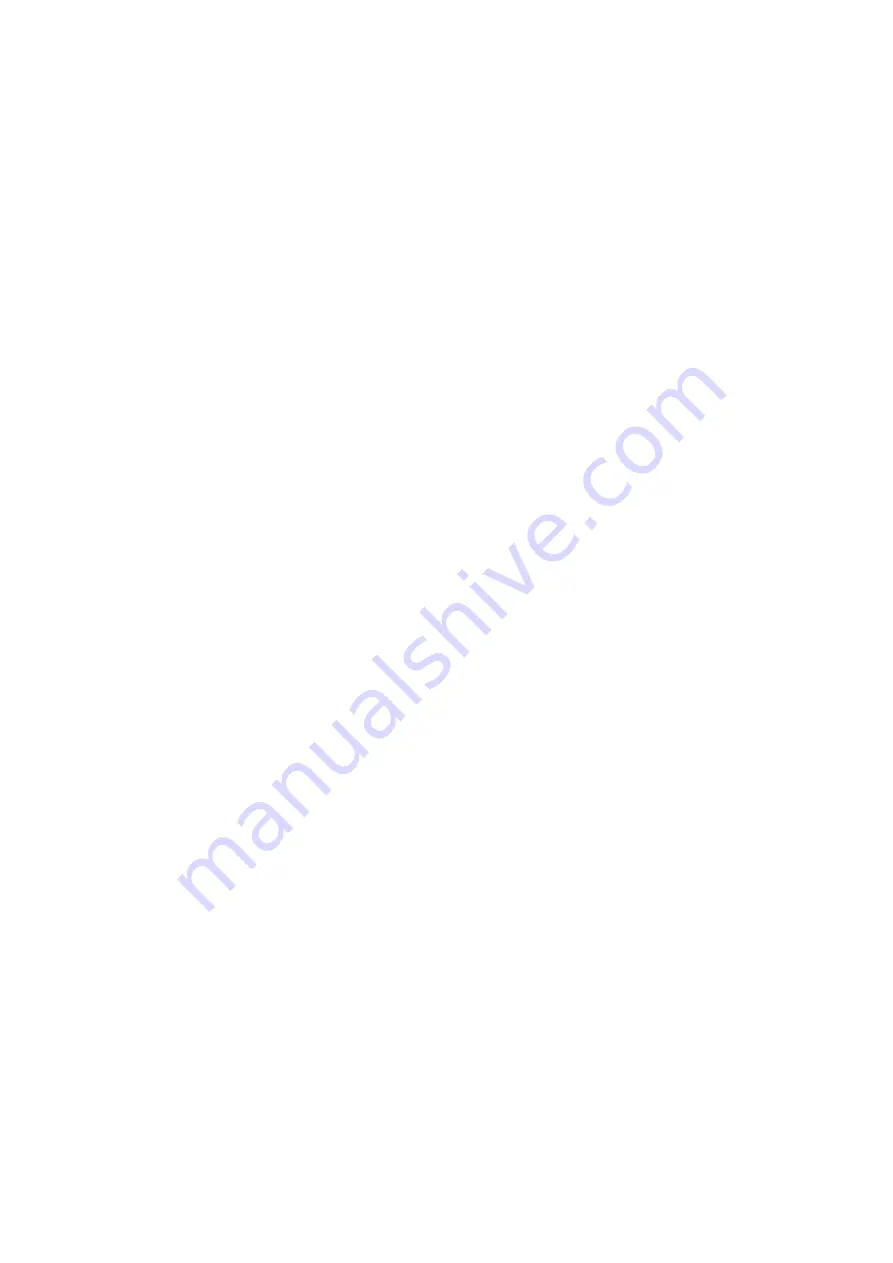
B 3
B
635_
D
E
M
.D 3
-24
01-
01.
07.
2.1
Vehicle
Construction
The paver finisher has a welded steel frame on which the individual components are
mounted.
The caterpillar drives compensate uneven areas on the ground; the suspension of the
attached screed additionally helps to attain a high paving precision. The continuously
adjustable hydrostatic traction drive allows the speed of the paver finisher to be
matched to all work conditions.
Operation of the paver finisher is faciliated by the automatic material handling system,
the separate traction drives and the clearly structured operating and control elements.
The following extra equipment (option) is available:
o
Automatic levelling/slope control system
o
Ultrasonic sensors for material transport (controller)
o
Additional cut-off shoe
o
Larger working widths
o
Automatic central lubrication system for the finisher and/or the screed
o
Protective roof
o
Further equipment and upgrade options on request
Engine: The paver is driven by a water cooled Diesel engine. For further details see
the technical data and the engine's instruction manual.
The particle filter (
o
) cleans the exhaust gas from the soot particles produced, reduc-
es the generation of harmful carbon-monoxyde and carbon-dioxyde gases, therefore,
it operates as a catalyser to minimize the load on the environment and health. A con-
trol light indicates the necessity of maintenance operations.
Caterpillar drive: Both caterpillar drives are directly driven by separate drives with-
out any drive chains that would require maintenance and servicing.
The tension of the caterpillar chains can be readjusted using tensioners.
Folding track cleaners are mounted before each crawler track (
o
), which ensures
the flat road section while paving. The minor obstacles found in the track lane are
pushed to the side by the machine.
Hydraulic system: The diesel engine drives the hydraulic pumps for all main drives
of the paver finisher via the attached distribution gear and its auxiliary drive shafts.
Summary of Contents for DYNAPAC Svedala Demag DF 115 C
Page 2: ...VALUE QUALITY THE ORIGINAL Your Authorized Dynapac Dealer...
Page 10: ......
Page 18: ......
Page 20: ......
Page 44: ......
Page 58: ......
Page 62: ...D 1 4 4 D_1 4_01_GB fm 4 22 Element2_konv_Kette_635 bmp 9 12 9a 5 8 14 A 6 7 13...
Page 64: ...D 1 4 6 D_1 4_01_GB fm 6 22 Element2_konv_Kette_635 bmp 9 12 9a 5 8 14 A 6 7 13...
Page 96: ......
Page 120: ...D 4 6 24 D_4 6_01_GB fm 24 38 2 2 Error messages...
Page 121: ...D 4 6 25 D_4 6_01_GB fm 25 38...
Page 122: ...D 4 6 26 D_4 6_01_GB fm 26 38...
Page 123: ...D 4 6 27 D_4 6_01_GB fm 27 38...
Page 124: ...D 4 6 28 D_4 6_01_GB fm 28 38...
Page 125: ...D 4 6 29 D_4 6_01_GB fm 29 38 2 3 FMI codes...
Page 134: ......
Page 146: ...E 01 12 E_01_GB fm 12 18 3 Auger extension auger type II Auger_DEM bmp...
Page 152: ......
Page 154: ......
Page 157: ...F 3 0 1 F_3 0_01_GB fm 1 4 F 3 0 Maintenance Conveyor 1 Maintenance Conveyor...
Page 161: ...F 4 1 1 F_4 1_01_GB fm 1 8 F 4 1 Maintenance Auger 1 Maintenance auger sub unit...
Page 168: ......
Page 180: ......
Page 181: ...F 6 0 1 F_6 0_01_GB fm 1 8 F 6 0 Maintenance Hydraulic system 1 Maintenance hydraulic system...
Page 220: ......
Page 221: ...F 10 0 1 F_10 0_01_GB fm 1 6 F 10 0 Checks decommissioning 1 Tests check up cleaning stopping...
Page 226: ......