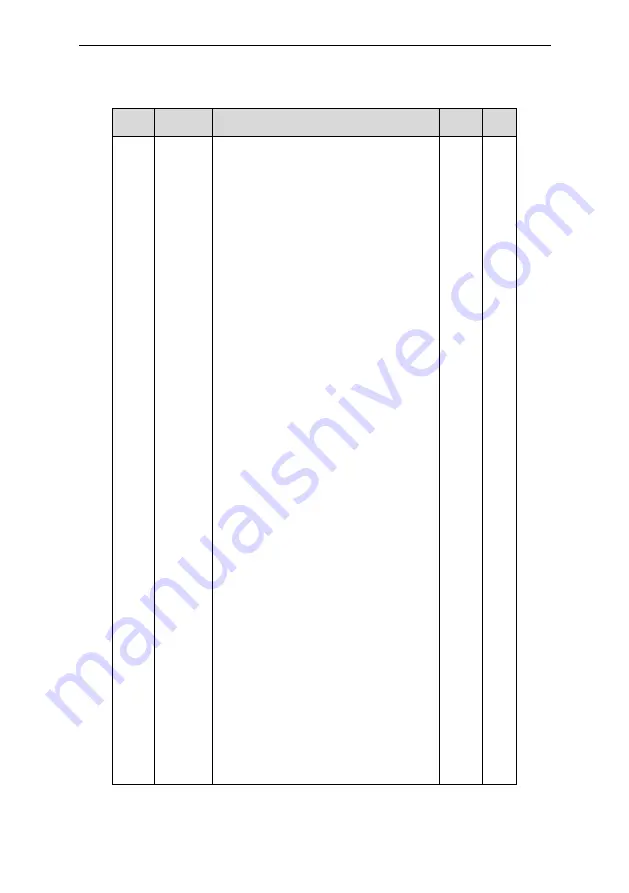
Astraada DRV-24 frequency inverters Function Parameters
28
Functio
n code
Name
Detailed instruction of parameters
Defaul
t value
Modify
Note: when analog AI2 select 0~20mA input,
the corresponding voltage of 20mA is 10V.
100.0% of the analog input setting corresponds
to the maximum frequency (function code
P00.03) in forward direction and -100.0%
corresponds to the maximum frequency in
reverse direction (function code P00.03)
4:High-speed pulse HDI setting
The frequency is set by high-speed pulse
terminals. Astraada DRV-24 series inverters
provide 1 high speed pulse input as the
standard configuration. The pulse frequency
range is 0.00~50.00kHz.
100.0% of the high speed pulse input setting
corresponds to the maximum frequency in
forward direction (function code P00.03) and
-100.0% corresponds to the maximum
frequency in reverse direction (function code
P00.03).
Note: The pulse setting can only be input by
multi-function terminals HDI. Set P05.00 (HDI
input selection) to high speed pulse input, and
set P05.49 (HDI high speed pulse input function
selection) to frequency setting input.
5:Simple PLC program setting
The inverter runs at simple PLC program mode
when P00.06=5 or P00.07=5. Set P10 (simple
PLC and multi-step speed control) to select the
running frequency running direction, ACC/DEC
time and the keeping time of corresponding
stage. See the function description of P10 for
detailed information.
6: Multi-step speed running setting
The inverter runs at multi-step speed mode
when P00.06=6 or P00.07=6. Set P05 to select
the current running step, and set P10 to select
the current running frequency.
The multi-step speed has the priority when
P00.06 or P00.07 does not equal to 6, but the
setting stage can only be the 1~15 stage. The
setting stage is 1~15 if P00.06 or P00.07 equals
to 6.
7: PID control setting
The running mode of the inverter is process PID
control when P00.06=7 or P00.07=7. It is
necessary to set P09. The running frequency of
the inverter is the value after PID effect. See
P09 for the detailed information of the preset
source, preset value and feedback source of
PID.
Summary of Contents for AS24DRV4075
Page 1: ...Operation Manual Astraada DRV 24 Frequency inverters ...
Page 2: ......