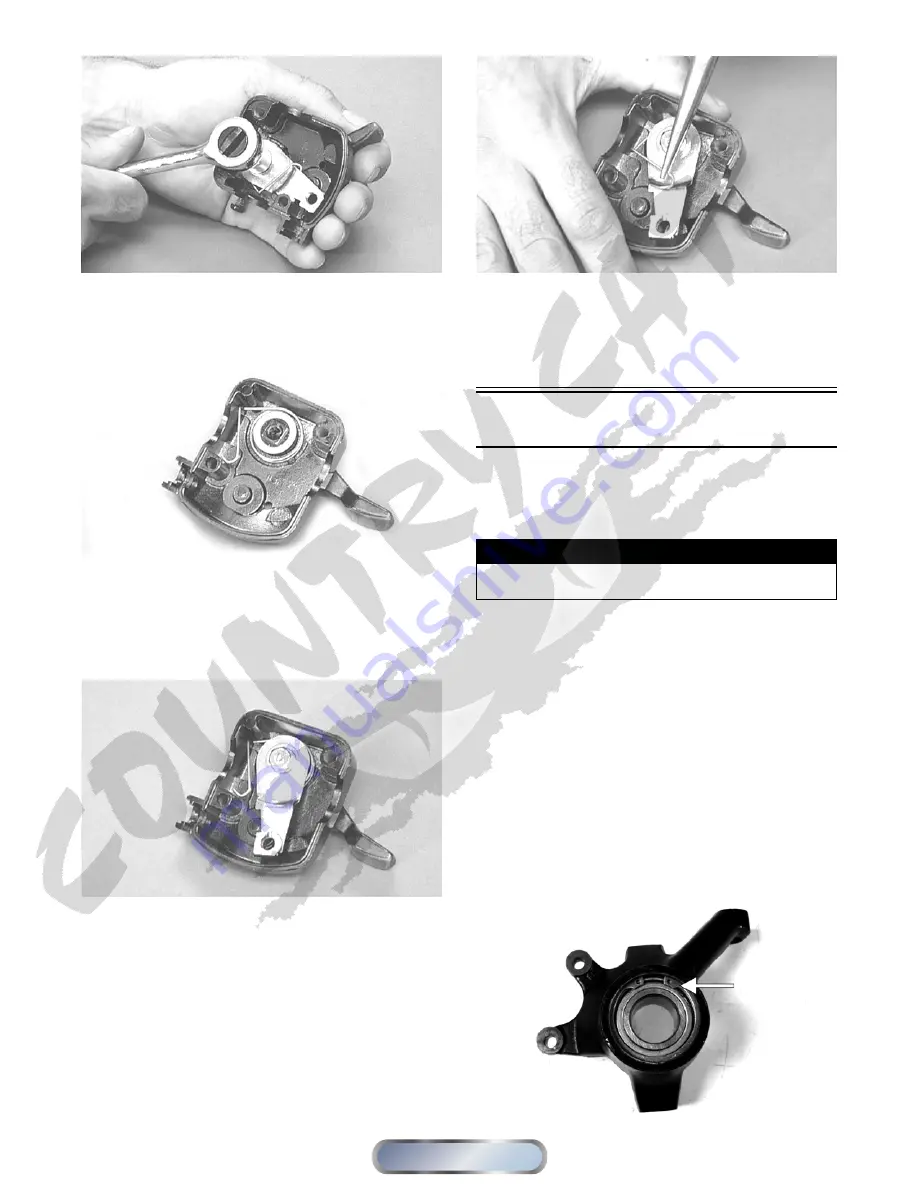
114
AF677D
4. Remove the actuator arm and account for a bushing.
Note the position of the return spring for installing
purposes.
AF678D
INSTALLING
1. Place the return spring into the throttle control; then
place the bushing and actuator arm into position.
Secure with the cap screw, lock washer, and washer.
AF679D
2. Using a pair of needle-nose pliers, place the spring
into position on the actuator arm.
AF680D
3. Place the two halves of the throttle control onto the
handlebar and secure with the two machine screws.
ADJUSTING
To adjust throttle cable free-play, see Periodic Maintenance.
Steering Knuckles
REMOVING AND DISASSEMBLING
1. Secure the ATV on a support stand to elevate the
wheel; then remove the wheel.
2. Remove the wheel cap from the hub; then remove
the cotter pin from the nut.
3. Remove the nut securing the hub.
4. Remove the brake caliper.
5. Remove the hub assembly.
6. Remove the cotter pin from the tie rod end and
remove the tie rod end from the knuckle.
7. Remove the two cap screws securing the ball joints
in the knuckle.
8. Tap the ball joint end out of the knuckle; then
remove the knuckle.
9. Remove the snap ring from the knuckle; then remove
the bearing.
PR287A
! WARNING
Make sure the ATV is solidly supported on the support
stand to avoid injury.
Manual
Table of Contents